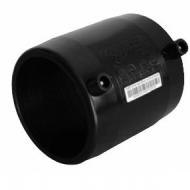
Electro fusion fittings. Electrode Couplings
Coupling pe
Electrosized couplings are divided into several categories, depending on the purpose. Each of them is equipped with an electric heating device, which is built into the coupling. This fact facilitates the welding of polyethylene pipes or other materials with each other.
What are electrically welded couplings for polyethylene
Assembling of pipelines and networks, is made with the use of fittings. They are used in the following cases:
- for large-scale construction of a gas pipeline;
- in systems, as well as water pipes with industrial water;
- when transporting various chemical elements, which do not come into contact with polyethylene.
These products are manufactured in several configurations. It depends on the diameter and size required for the installation of technical products. Depending on whether the coupling goes to water or gas, the diameter will vary from 20 millimeters to 3.15 centimeters. However, universal materials are widely used, which have found wide application in the assembly of any kind of pipelines.
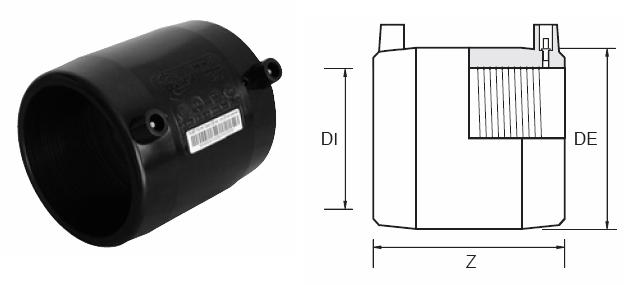
Structure of electrowelded products from polyethylene
All electrically welded materials have a rather complicated structure. The spiral, which is in, is made of a special alloy. It repels the various that are formed during operation. In addition, the spiral serves as a kind of criterion for quality welding. As the alloy of the spiral does not give the temperature to external components, welding works on electrically welded couplings pass quickly and without problems. The output is one single device.
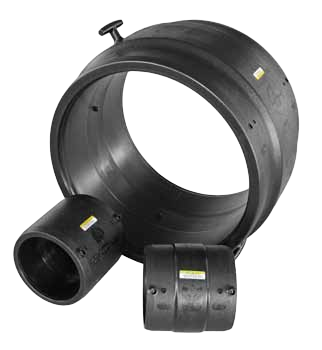
The main advantages and disadvantages of electrically welded couplings designed for polyethylene
1. To serve such couplings will be not less than 50 years.
2. Accessibility for the general public.
3. There are no restrictions for the operation and assembly of the structure on inaccessible pipe laying areas.
4. Components that are suitable for all forms of polyethylene pipes, due to its versatility.
5. Complete collection of all parts of the device is performed in a matter of hours.
6. Pipeline devices made with the participation of electrically welded couplings are particularly robust and reliable.
7. Provide a shorter build period.

But aside from considerable advantages, the couplings also include several drawbacks, which sometimes are somewhat limited in working with such material:
1. If the location of the joint on the pipe is subject to the influence of an alkaline or acidic medium, this factor can have a very negative effect on the material used.
2. They do not tolerate high pressure in working order.
3. You can not use them in heating and hot water, because more than 40 degrees Celsius, for them, is disastrous.
However, all the above disadvantages of the parts due to, their qualities such as the strength and simplicity of the mounting connection, are erased. And every year, the scope of their application, is only expanding.
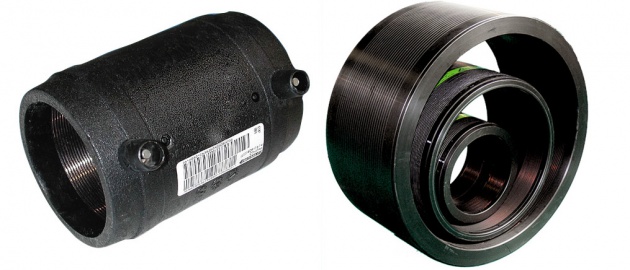
How is the installation using electrically welded parts
Installation works are performed by supplying an electric current to the heating part, which is in the clutches with built-in heating parts. Subsequent increase in temperature, gives the inner walls of the product and part of the pipeline to be welded, resulting in the formation of a boundary that has a complete seal and a high-quality soldering of the material.
Installation itself using fittings includes the following items:
- from the very beginning, the pipe, which must be connected to the general structure, is cut off clearly at a right angle. Categorically you can not leave any roughness or roughness. After a smooth cut, the product is cleaned of adhering dirt;
- further, the cutting site is carefully cleaned with a special technical tool. In doing so, observe the diameter for the entrance to the electro-welded fitting. After all, the connecting parts must be degreased, for which a piece of clean cloth with acetone or other solvent applied on it is used;
- the sides intended for welding are carefully fixed in. In some modifications of fittings there are already these fasteners, into which the ends of polyethylene pipes are then inserted. It should not be forgotten that the distance between welded pipes located in the middle of the coupling must not exceed the thickness of the walls of the polyethylene pipe;
- welding works are carried out, for successive pipe fittings. Welding passes automatically, the smart device can independently set the temperature corresponding to this type of welding in addition, set the percentage of voltage and the time limit of welding. In the process, the welding terminals are connected to the contacts of the electrowelded section, and all information from the barcode is automatically transmitted. This code has all electrically welded couplings;
- once the welding work is completed, the joints are immediately checked. They must be completely sealed. To check, the joints are soaped and then compressed air is fed through the pipe.
For a mounted system to serve for a long period of time, the work must be done by qualified craftsmen. If used in the process of electrically welded couplings, designed specifically for polyethylene pipelines, the output is a strong and solid construction.
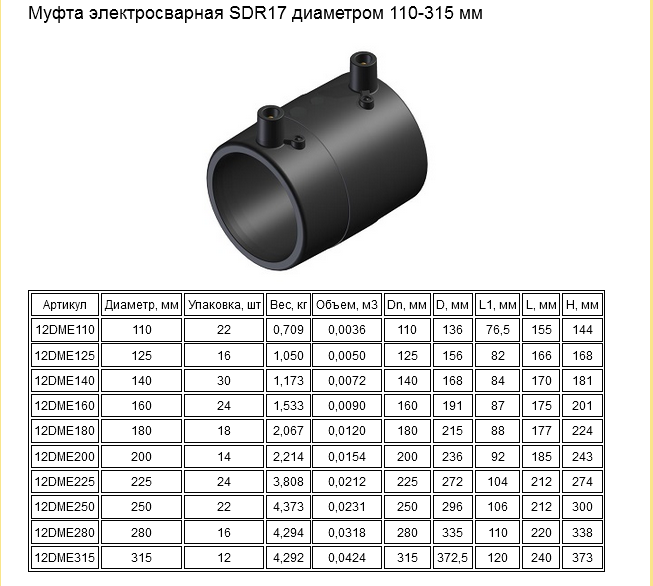
In what areas have been used electrically welded couplings
Due to the fact that the installation of such connections is carried out quickly enough, they are simply irreplaceable for emergency and emergency work. In the case of the impossibility of using other elements for butt welding on the construction of a pipeline of increased complexity, couplings are used. And the built-in spiral in electrically welded couplings makes it possible to carry out installation in difficult conditions, for example - trenches.
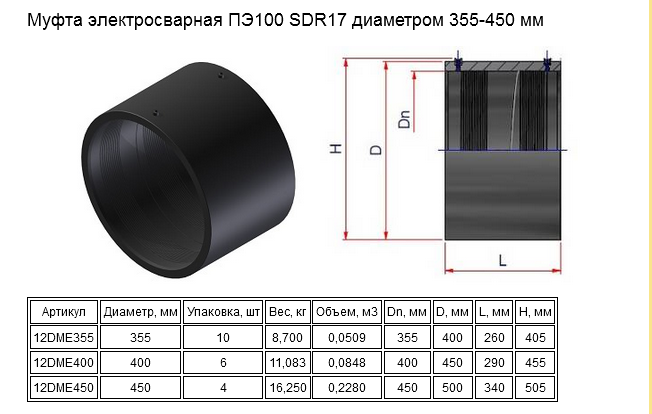
Working pressure: 6 bar Gas - 10 bar Water
SDR 17
Polyethylene type: PE100
What electrically welded couplings to choose from
Experts advise to purchase Italian, German and Austrian couplings. The products of these countries have proved themselves well. Well-known manufacturers do not manufacture fittings of their various secondary raw materials, which, of course, positively affects the quality of the elements. It is worth paying attention to the Russian manufacturers, the details of which are widely represented on the domestic market.
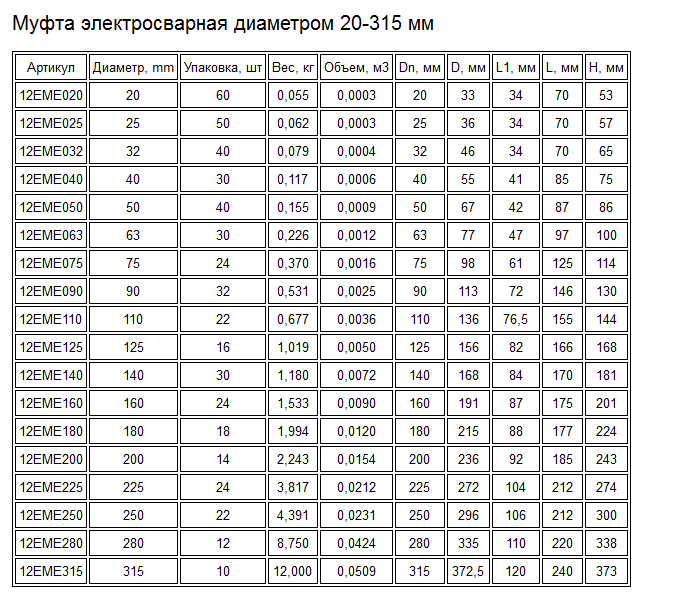
Operating pressure: 10 bar Gas - 16 bar water,
SDR: 11
Polyethylene: PE100
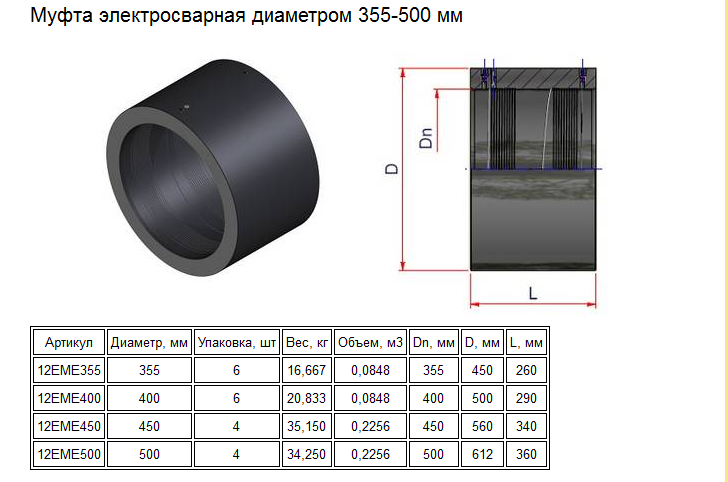
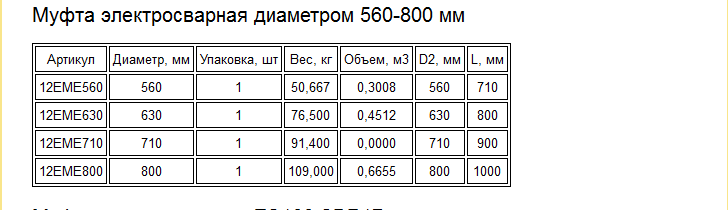
Summing up
If in the near future, there are plans to install and repair a pipeline or some part of it, the purchase of clutches with an integrated heating element will be the right solution. After all, everyone wants to get a reliable, strong and durable design, which does not require additional effort in its maintenance.
During the installation of the pipeline, it will be necessary to use connecting elements that can guarantee the integrity of the system.
To facilitate the adhesion of plastic materials to each other, it is advantageous to use electrically welded couplings for polyethylene pipes.
This type of fittings is equipped with an electric heating system built-in design. These products are divided into several types, which are used in certain cases.
Coupling is used to combine different types of polymer pipes that are used in cold water supply systems.
It can be both artesian and technical water. They are also often used in the construction of a pipeline to transport natural gas and chemicals that do not interact with the HDPE polymer.
The PE100 SDR11 coupling behaves well as a connecting part of systems with an internal pressure of 16 atmospheres if the temperature of the transported liquid does not exceed 40 ° C. And the heating part, which is equipped with this type of products, produces a melt of polyethylene to a viscous species.
When the connection has taken place and completely cooled, the parts of the pipeline become one monolithic structure.
The PE100 SDR11 coupling, like the other fittings, is equipped with a chip that displays a barcode. It contains detailed instructions on the material: the time frame of heating, the required current and the time of complete cooling.
This kind of encoding is not only convenient, but also practical, since the scanner is scanned in seconds, and the welding tool is automatically configured for the necessary parameters for high-quality work.
The electrically welded coupling PE100 is equipped with a spiral, which is made of a special alloy, which does not allow its contamination and ensures high quality of welding operations.
The metal from which the spiral is made does not provide temperature compensation, therefore welding works are carried out quickly and lead to the formation of a single monolithic structure.
Installation
The PE100 coupling is installed as follows. Electric current is supplied to the heating spiral, under the influence of which the polyethylene pipe walls melt, forming a high-quality joint. The whole installation process takes place in the following stages:
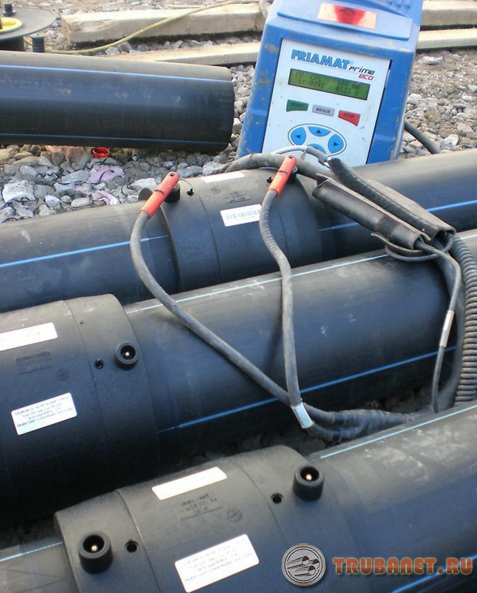
The connection element PE100 SDR11 according to the nomenclature assumes that it must withstand the nominal pressure PN16. And products of this brand are considered the most frequently used.
Compression products for polyethylene pipelines are usually made of polymers, but the collet or sleeve is made of metal. The body for combining with PE pipes is poured from plastic.
The maximum use of the diameter of compression couplings, which is considered to be economically viable, is 6 cm. Pipelines made of polyethylene with a larger cross-section than 6 cm are not advisable to be joined by a compression coupling, although manufacturers produce models measuring 10 cm in diameter.
Compression coupling for polyethylene pipes (collet) makes it possible to make the connection collapsible, and the construction with the connector makes the connection an all-in-one.
This should be taken into account when constructing the pipeline, especially if it is immured or buried in the ground.
Since this connecting element for polyethylene pipes fixes their ends on its nipple by means of a crimping element, the press clutch connects the elements of the pipeline by means of a sleeve, which is crushed by special clamps. And if you can unscrew the nut, then align the sleeve - no.
And in any other cases, when the implementation of the butt joint is not possible.
Video 3
According to the installation technology PE100 SDR11 can be performed in a wide range of temperature conditions, which allows for installation and repair work in winter cold and in summer heat.
Correct choice of electrically welded fittings
Today, in the construction market, you can see a huge range of electrically welded PE couplings from different manufacturers. Initially, it is worth paying attention to customer reviews and recommendations of professionals.
Video 4
Equipped with built-in electric heating devices and are designed for or other connecting elements. Such products can be of different types and purposes.
Types of electrically welded couplings for polyethylene
With the help of electrically welded fittings, various networks and pipelines are installed, to which polyethylene is resistant. They are used in construction:
- water supply systems for drinking and industrial water;
- pipelines for gas transportation;
- transport systems for chemical elements that do not react chemically with polyethylene.
It is applied pe electrowelded clutch at a working pressure of no more than 16 atmospheres and a temperature of the working medium not exceeding 40 degrees.
Such products are produced in several varieties depending on the diameter and purpose. The diameter can vary from 20 mm to 315 mm and differ in performance characteristics, for which pipeline they are intended - for gas or water, although to date they produce electrically welded elements of universal purpose, which are successfully used on all types of pipelines.
Advantages and disadvantages of electrically welded polyethylene couplings
Polyethylene clutches with built-in electric heating device have such performance characteristics that can be attributed to their advantages. Advantages of electrically welded couplings:
Electro-welded polyethylene couplings also have a number of drawbacks that must be considered when selecting the connecting elements and installing the entire system.
Disadvantages of electrowelded couplings are:
- impossibility of using such connections for heating wiring and hot water supply system, as they are designed for operating temperature up to 40 degrees;
- such materials can not be used if the pipeline has high working pressure;
- these compounds are afraid of a strongly acidic and alkaline environment, so when using these factors must be taken into account.
Despite the small shortcomings of these details from polyethylene, their use is increasing every year. The reliability and speed of installation play a role here, which is very important when used in the elimination of various accidents.
Design of electrically welded polyethylene joints
Electro-welded elements have a complex design. The coupling contains a closed special spiral, which is made of a special alloy. This helix prevents various impurities, and also makes the welding quality high. The material from which the helix is made in this connection does not provide temperature compensation, and therefore welding of electrowelded couplings occurs rather quickly, and the components to be joined become one monolithic construction.
Installation using electrically welded elements
Mounting of clutches with built-in heating element takes place by feeding electric current to their heating elements. Under the influence of high temperature, the walls of the connecting piece and part of the pipeline melt and provide a high-quality and hermetic joint. The installation of the entire system with the help usually takes place in several stages:
If the installation of the structure is performed by experienced specialists in accordance with all building codes and rules, then such a system will serve for a very long time. Using electrically welded couplings for polyethylene pipes as connecting products, when installing a pipeline system, a visually uniform and monolithic system is obtained.
Scope of electrowelded couplings
The use of electrowelded couplings covers a fairly large area. They are used in the construction of pipelines of various purposes and engineering communications. Most often clutches with a built-in spiral are used in repairs in cramped conditions, for example in trenches. Due to the rapidity of welding of such connections, these connecting parts are indispensable for emergency work. Their application is permissible in the construction of complex pipeline structures and branches from an existing pipeline, where it is impossible to perform butt welding for any reason.
It is common to use such fittings when installing piping systems with a diameter of up to 110 mm. The technology of welding couplings allows you to perform work in a wide range of temperatures, that is, the use of such elements is indispensable for repairs in frost or hot summer. When welding, the entire process can be logged, which makes it possible to use this technology when welding gas pipelines.
Which electrically welded couplings are worth choosing
In the modern market there is a large number of electrically welded couplings made of polyethylene of various manufacturers. Welded elements of production of industrial companies can be found:
- Austria;
- Germany;
- Italy;
- Russia.
Choosing fittings for installing pipes, you must first rely on customer feedback and follow the advice of experts. In large specialized stores, you can find electrically welded joints of famous brands from different manufacturing countries. Here you can carefully consider each product and get the most comprehensive information on its installation. In such stores, there is usually a large selection of special soldering irons for welding systems. Many experts recommend the use of electrically welded couplings of foreign production, there is logic in this, as the use of recyclable materials for the manufacture of such fittings is practically excluded, therefore, they will be more reliable.
Conclusion
If you plan to conduct a new pipeline or upgrade an existing one, then couplings with a built-in electric heating element will be indispensable as joints of polyethylene pipes. In this case, the whole structure will be strong and airtight, and its maintenance will not cause trouble.
Electrofusion pipe fittings are attached to the ends using electrodiffusion welding. A current is applied to the heating coil mounted inside the connecting element. The supply voltage and time are adjusted automatically by the machine, depending on the settings. When the current is passed, the fitting elements of the fitting and the surface of the pipes at the junction point are heated and melt. Strong molecular bonds are formed in the thickness of the seam. The fitting provides a reliable, hermetic, all-in-one connection.
Assortment of products
Electrofusion fittings of HDPE are produced by a wide range of products. The range includes tees, couplings, transitions, plugs, saddle branches, stopcocks and other products. The use of fittings during the installation of pipelines allows builders to connect pipes of different diameters, to block the working flow, create tie-ins, change the route of the system, and solve many different tasks. With electrically welded connecting elements, the work is performed qualitatively and as quickly as possible.