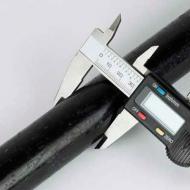
How to properly connect the gas pipes. How to connect gas pipes
With the development of technology, a certain type of material is increasingly less used. Several solutions can be used to implement the same tasks. This applies to both construction and laying of communications. First of all, you need to know how to connect the gas pipes. The article will tell you about the types of connection and technology.
Types of pipes
Up to a certain point, seamless metal pipes were used for gas mains. But their service life is limited by the corrosive effects to which they are exposed due to precipitation and other factors. Therefore, along with them, also began to apply:
- Polyethylene. Much cheaper in production than metal mining, the material is also resistant to design pressure in the mains. High elasticity, as well as tightness of joints are very handy in soils, which are characterized by abrasion. Plastic is a dielectric, so it does not conduct current. This is a guarantee of safety in the event of problems with the electrical network.
- Rubber. To a greater extent, this material is used to connect the central channel with the consumer, whether it is a boiler, gas column or something else. A composition is selected that does not crumble due to exposure to sunlight.
- Stainless steel. To be more precise, a braid is made of this material. The inner sleeve is a PVC sleeve.
- Copper. Not so long ago, it was officially approved for low-pressure channels. Advantages are the resistance to corrosive effects of both water and other substances.
The choice of the product will depend on the specific conditions and the already installed system.
Ways of connection
Each of the listed types of pipes can be articulated in one or more ways. Of the main distinguish these:
- Threaded. Most common, as for connecting or laying small sections of the pipeline from the meter. It is carried out with the use of additional sealing materials of natural or artificial origin.
- Soldering. It is applied to pipes made of polyethylene, and also in some cases and copper . In respect of the former requires the availability of professional equipment, without which it is impossible to carry out the action qualitatively. It is most often used on large-diameter main pipes where there is no possibility of using another method.
- Welding. For metal pipes, it can be done with an autogen or an arc welding machine. In the case of the former, there is less likelihood of stress occurring in the parts to be welded. The seam turns smooth and airtight. When using the second option to achieve this result is a little more difficult, but for a professional it is also possible.
- Flanged. It is used on trunk pipes, as well as in those places where the line is adjacent to the reducer and must enter the house. It is an articulation with the help of two rings, between which the sealant is laid, after which they are tightened with bolts and nuts.
- Inset. A rather complicated procedure. Can be performed both under pressure, without stopping the feed, and without it. In the first variant, the method of extinguishing the flame by the autogen itself was used in the past. To date, systems and tools have been developed that significantly simplify the task and increase safety.
Note! Some types of articulations can be freely implemented independently. But especially with regard to the latter, specialist help is required. If you do not have the necessary skills, you can cause irreparable harm to yourself and others around you.
Threaded connection
This method is used for both intermediate and end sections of metal pipes. If there is no thread on the spout, it must first be cut. To do this, you need these tools:
- klipp;
- lerca;
- lubrication;
- file.
Before starting work, you need to determine how much the cut should be. It all depends on which connecting fitting or nut from the hose will be used. The sequence is as follows:
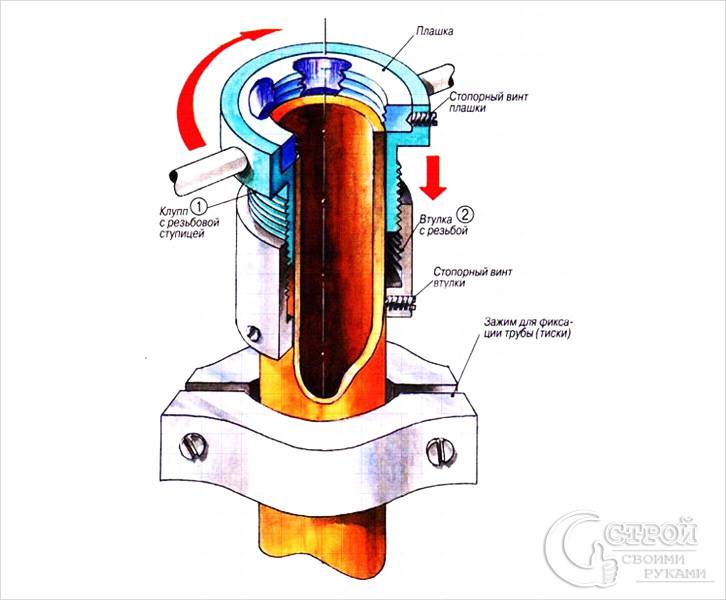
Read more about the thread cutting technology on the pipe.
Next, you need to seal the future joint. To ensure that the winding does not rotate, before the beginning of all operations, it is required to make perpendicular notches on the thread using a file or pliers. For this, a tow or special Teflon tape is used. The latter should be denser than that normally used on water pipes.
Flax must be well spread. From the main spit is separated a small strand and is leveled. What specific amount is required will have to be determined empirically. The cut is placed on the middle of the thread. One end is 2 full turns. After that, the ends intersect with each other, one fits under the other and another turn is made. Then twist the two parts. The whole surface is smeared with sealing paste. The required parts are connected:
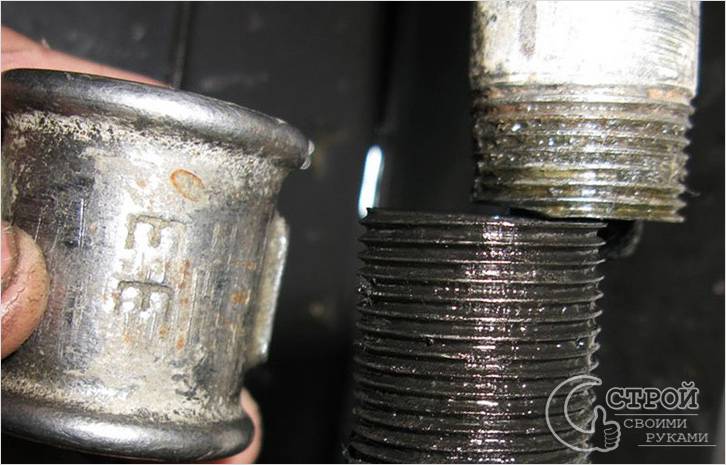
Note! In some areas, the use of hoses with braided stainless steel is prohibited. This is due to the fact that with a strong bending, the inner part is damaged and the leakage is difficult to detect. If it is not timely to eliminate it, the consequences can be catastrophic. In other cases, do not allow the use of white PVC hoses and require the purchase of only black rubber.
Welded connection
The concept of a welded joint is applied to both metal pipes and polyethylene ones. To solve the first problem, the arc method will require the following tools:
- inverter or transformer welding machine;
- electrodes;
- protective mask;
- gloves;
- a malleus or a suture brush.
The works are carried out in this way:
- If possible, it is better to fix the workpiece well. This is necessary for greater convenience to the master.
- In order to ensure complete tightness, a gap of 2 mm between the pipes is required. This will allow the flowing metal to cling to the ends.
- It is fixed by small stitches in several points.
- In the main process, the electrode should be led from the bottom to the top.
- It is important to ensure that there is no overheating. A consequence of this may be an unnecessary tension at the joint, as well as burning metal nearby.
- Some masters impose two seams. One serves to fill the space, and the second goes as insuring.
- Do not mix the scale immediately. You should wait at least 15 seconds. Thus, the necessary grasping will occur and there will be no microcracks.
When using gas welding equipment, the requirements for fixing the workpiece will be the same as in the previous case.
- The first thing is to open the current from an oxygen cylinder, then with an acetylene gas.
- If there is air in the hoses, the fuse can not occur immediately.
- The flame is adjusted to the required value.
- The welding site is well warmed up.
- After that, a special electrode is brought up. To lead it is necessary so that it forms an influx, but does not drain down.
- At the end of the process, the part is cooled.
Note! Check the joint for any connection option in one simple way. A soap solution is prepared. It should foam well. It is applied to the required place. If there are bubbles, it means to have a fistula. It is strictly forbidden to test with open fire. It can be explosive.
For polyethylene pipes, there is also the concept of welding, but it is carried out by a different method. In this case, an apparatus is used which is capable of outputting a small voltage and controlling the desired temperature. But the main thing in this case is the connecting fitting. In its design, a heating element is incorporated. As the process proceeds, it begins to melt the space around itself, which leads to the formation of a homogeneous mass, which after curing seals the seam.
The step-by-step solution looks like this:
- The ends of the pipes are prepared. To do this, they are cut using a special cutter. You can not do this with a hacksaw. The planes should be absolutely level, without torn chamfers and burrs.
- A mark is made from the edge. The distance to it is half the size of the fitting plus 2 cm.
- With the help of a special scraper or machine, a layer of oxide is eliminated. This should be done evenly, by going to the same size. In order to be easier to navigate, you can apply additional perpendicular lines, as cutting is easy to judge the correctness of the performance.
- Eliminate all burrs and chips.
- Docking areas are wiped with a suitable solvent or napkin with alcohol.
- Before putting the mark on the fitting is put on. If one of the pipes is stationary, then the clutch is clogged to full size. The second element is brought in and the connector is neatly displaced to evenly close the nozzles.
- Plug connectors from the welding machine are connected to the clutch contacts.
- The optical scanner reads the information printed on the barcode and starts the process.
- The unit itself will determine what temperature and voltage are needed, and also how long the cooling period will be. It is important to fully endure all the stages. Only in this case it is possible to speak about reliability.
- After completion of the welding, all information about the time, date, operator, temperature and voltage must be applied.
Such tools are usually used at main gaps, where pipe diameters exceed a value of 80 mm.
The process of electromotive pipe welding is shown in the video:
Soldering
It will be more correct to say soldering. It is also used for polyethylene pipes. The condition for its implementation will be the mobility of the two articulated parts. Otherwise, the process will be broken. In terms of efficiency, it is not inferior to electric coupling. To perform the work you need a modular unit. Its components are a hydraulic unit, a cutter, a soldering iron and a centralizer. To properly use it, act as follows:
- In special clamps, liners are fitted to the size of the pipe being treated.
- The nipples are clamped. Do not be zealous, if you tighten the bolts, the butt will lose the shape of the circle, which will lead to problems.
- The areas to be soldered are cleaned of dirt and dust.
- A chip cutter, if present, is eliminated with a construction knife or other device.
- On the hydraulic unit, the valve slowly opens until the components start moving on the centralizer. The pressure value is marked as working pressure.
- The details are divorced, between them is inserted the face. It starts and shifts again. After several turns of knives, the device can be picked up.
- To check the correctness and smoothness of the joint, the branch pipes are again shifted and well inspected.
- Joints are degreased with a solvent or an alcoholic napkin.
- The soldering iron is put on a warming-up.
- After reaching the set temperature, it is installed between the parts.
- The table shows the pressure for soldering and the centralizer modules are shifted again. They are held in tension until an inflow of 1 mm.
- After that, the pressure is released, and they warm up for a few more seconds.
- The parts move apart and the heater is retracted. For 5 seconds, they must be reconnected under voltage for another 5 seconds. After this, the force is removed and the cooling time is waiting.
Before the end of the time interval, which is indicated for cooling, it is by no means possible to clean the vise or in any way to tilt the pipes. This can lead to depressurization.
Flange connection
Flange connection is used for pipes of various materials. The method of its implementation is almost the same. For polyethylene pipes, you will need:
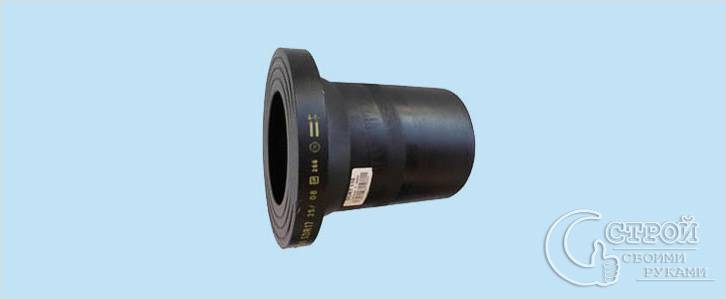
In the case of metal pipes, there is another option that does not require the use of welding.
- The alignment of the ends is carried out. They must be perpendicular to the axis of the pipe. It is important to remove all burrs.
- The pipes are fitted with loose flanges and move further away from the edge.
- The next step is stretching the elastic band. It will be necessary to leave the ledge about 10 mm.
- The rings move towards each other and abut against the seals.
- Fixation is carried out by bolts, as described above.
This method is used infrequently and in those areas where there is not much pressure. Most often, the flange is required in order for a crane to be fitted to the rupture.
Box
Such work may require special qualifications and permission from the relevant authorities. It is produced in two ways:
- Hot method. In this case, a gas cutter or arc welding machine is used. The process is reduced to cutting out in the main pipe a hole and fixing the corresponding transition element. At the same time, the pressure must be reduced to the limits of 40-150 kg / cm 2 at the site of work. If the approach is wrong, it can result in fire and accident.
- Cold method. In most cases, pressure changes are not required. All actions are carried out using a special device. This is what we will consider further.
First of all, the site where the work will be done is well cleaned up. The heater, paint and rust are removed. A special adapter with a flat valve is welded to the prepared place. The quality of the welded joint is checked by the crimping method. It should be without shells, and also able to withstand the planned pressure. Then the sequence is:
- The assembly of drilling equipment is performed. In this case it is important not to forget to install a magnet on the base of the drill.
- A connector for the drill is attached to the previously installed adapters.
- Measurements are made of how much the stem should be lowered.
- The intermediate chamber is tested for presumed pressure by an air compressor.
- Rotation from the motor is transferred to the drill through the reducer. This makes it possible to reduce the speed.
- After passing through the walls, the crown rises to the required level and the flap closes.
- The pressure in the chamber is reset, and the drill is removed with the pipe part.
- An additional nozzle is installed through which the pipe is inspected and the debris and other debris are removed.
- The surplus of pressure is reset again. Removed all the additional parts and installed a branch line.
- The flap is removed, and the connector under it is closed with a welding seam.
This article describes most of the available ways to connect gas pipes. What will be required in a particular case, will depend on what is provided by the project.
Video
This video shows how to connect a gas column to a gas pipeline:
How to connect gas pipes
More and more people are trying to do all the necessary work on their own, just how to be if the person simply does not have certain skills and knowledge? In this situation, you just need to follow the instructions that professionals can give. This article provides information on how to connect gas pipes yourself with the help of special tools and auxiliary materials.
If you have decided to independently carry out work on connecting the gas pipeline, then before starting the process, you need to study all the safety techniques. Check the integrity of the pipes that are located along the central highway.
Shut off the gas supply all over the house. If the work is carried out in an apartment, it is best to close the risers for neighbors for a while. If this is not possible, turn the special key that is on your gas pipe, thereby blocking the flow.
Note! If necessary, purge the remaining gas to avoid the possibility of an explosion in the event of a spark. Only after you make sure that no gas comes from, you can proceed directly to work.
Types of pipe connections
There are several basic ways to connect gas pipes, or rather:
- Welding - is carried out exclusively by specialists who have permission to work with the welding machine. Each employee must have a personal identification card.
- Threaded or fitting - also includes the welding of light pipes, while the sockets are sealed with hemp fibers. The whole process of work very much resembles the connection of sewer pipes. It is worth noting that the fiber is impregnated in advance with a solution of linseed oil or linseed oil. It is also possible to use couplings that can have both long and short threads.
- Flanged - one of the most common methods of connection, since it has a fairly light construction of the assembly. True, according to experts, it is less reliable than welding.
All the above-described connection methods are used by professional masters using specialized equipment.
In order to independently connect gas tubes in a house or apartment, you need to prepare the following tools and materials:
- gas adjustable wrench;
- tow and grease;
- hoses or pipe joints;
- if necessary, a connector having a thread on both sides.
Technological process
If you cut off the gas supply and blew the pipes, as recommended earlier, then the next step is to cut off unnecessary parts of the gas pipes. To do this you can use the Bulgarian, and if you do not have one, then a hacksaw for metal will do, but in this case the process will be long and more complicated.
After you have removed an unnecessary part of the gas pipe, you need to brew one end of it thoroughly or weld it.
If you need to connect one end of a pipe with a gas slug, then you need to cut the thread on the sawn part. To do this, there is a special nozzle, putting it on, you need to scroll several times.
Further on the made thread is wound a tow, which is impregnated with a lubricant and the connection with the hose is made. All these works are carried out using a gas swivel key. If you plan to install a new pipe, then you can use a special connecting adapter. This element has on both sides a finished thread and a nut that twists on the main and on the new pipe.
This method can be used in apartment buildings, but you only need to make sure there are no leaks. To do this, you need to open the gas supply, then apply a soap solution to all pipe joints.
Note! If as a result of this action bubbles appear on the surface, all connections must be re-tightened.
If previously you yourself have never engaged in similar work, it is best to entrust this matter to professionals.
The important point - to properly wind the thread on the thread. We offer you a video material that will help to cope with the task.
And from this clip you will learn how to seal the connections of gas pipes.
http://www.stroitelstvosovety.ru
The most important stage is laying the gas pipeline to the building from the main highway. During the execution of these works, there will necessarily be a need for connecting the pipelines.
How to connect gas pipes when connecting the house to the highway?
Threaded connection of gas pipes
An important parameter in the connection of steel pipelines is their cross-section. For sizes ½-2 inches, welded steel pipes with thread are used. For sizes over 2 inches, seamless single-piece steel pipes in a jute shell with a socket or threaded connection are used.
Gas pipeline steel pipelines are combined in a manner similar to the water pipe elements using fittings. To seal the joints, special hemp fiber, impregnated with linseed oil or linseed oil, is used. At the same time, it is not allowed to use any seals that make it difficult to disassemble the gas pipes. Installation of overhead cranes is also carried out without compaction.
After laying or repair, the gas pipeline must be checked at the end of the work. To do this, it is necessary to cover all the outlets and to supply the pipeline with air under pressure several times greater than the gas pressure. If within 5 minutes. pressure drops more than 20 mm of water column, there is a loss of tightness. In most cases, the gaps are fixed at the junction points of the pipes, but the whole section should be checked.
Given the correct choice of fittings are a sufficiently reliable connection for gas pipes. They should be pressed as tightly as possible to the pipes, if possible without using an additional seal. This precaution is necessary in order not to complicate the possible disassembly of the pipe. When connecting steel gas pipes with a fitting, the working pressure should not exceed 5 bar.
In boiler houses gas pipelines are connected by threaded couplings on a short and / or long thread. To seal joints use a linen strand with a mint, mixed with lead white or waxed on natural linseed oil. Sealing strand is wound on a thin, even layer.
Welding of gas pipes
For the alignment of pipelines, electric arc and gas welding devices can be used. First, the edges of the pipes to be joined are prepared. To get a quality seam, they must be cleaned of any contaminants. After this, you need to make a bevel. It makes it possible to obtain a strong and hermetic seam, since the molten metal completely fills the bond area.
In most cases, manual or semi-automatic arc welding is used. In arc welding, the optimum diameter of the electrodes is from 3 to 4 mm. The thickness of the walls of gas pipelines should not be more than 5 mm. In addition to preparation of the edges (a width of at least 1 cm), additional bevels must also be made. Then the centering and stitching are carried out evenly in 3-4 places. After that, welding is done in 2 layers. To obtain a sealed connection, it is important to capture adjacent areas of the products when making the final seam.
When gas welding is usually enough for one pass. The thickness of the walls of gas pipelines should not be more than 4 mm. Otherwise, the weld zone will overheat, which will adversely affect the strength of the joint. To avoid failure, the end of the seam should be performed with some overlap. When selecting the additive material, the steel grade of the gas pipe should be taken into account.
Polyethylene pipes
Polyethylene pipes have a high density, since they are produced under low pressure. Gas pipes made of polyethylene do not suffer from corrosion, do not crack at temperature differences, have other important advantages in safety issues. For example, polyethylene is not subject to electrochemical effects, remains neutral to gases and liquids. Elasticity and strength makes it possible to use this material at temperatures up to -45 ° C.
In this case, polyethylene pipes weigh a little and are simply connected. For the alignment of pipelines, simple welding machines and electric welding fittings are used that are simple to handle and do not require significant investment. An important detail: at the present time only steel pipelines are built in the house, and polyethylene can be used already inside buildings.
There are many types of pipes. Each species has its own meaning and function. The choice in most cases depends on the type of communications and the functions performed. There are also universal pipes that can be used in different systems. But they also need to be known and distinguished.
The matter is that, in case of wrong choice, there can be very different consequences. And if choosing the wrong pipes of cold water supply can only damage the material situation of the owners and neighbors, the wrong connection or choice of gas or heating pipes can cost health and even life.
Therefore, you should not hesitate, especially with gasification.
Types of gas pipes
Until quite recently, the question of the types of pipes for gasification would not have existed, because they were of one single material-steel. And all, no alternative and choice. But the times are coming, the technologies are not standing still, and now the steel is quietly replacing the polymer. Namely, special polyethylene, which is produced under low pressure, respectively, has a high density.
In addition, polyethylene has a number of enviable advantages, and in terms of safety of use.
Gas pipes HDPE do not rust, do not give in to corrosion and do not give cracks, even at temperature drops. For gas, this stability is very important, because there should be a constant pressure, and a microcrack is fraught with a dangerous leak.
Polyethylene does not react chemically and remains neutral to liquids and gases. Due to its strength and elasticity, the material can be mounted even at subzero temperatures and does not lose its strength and its wiring capabilities to -45 degrees. In addition, it is not a conductor of the electric current, respectively, is not subject to electrochemical destruction.
And one more advantage - light weight and easy connection, which adds popularity.
However, the following important detail should be taken into account here. Gas pipes, built into homes, are laid exclusively of steel, polyethylene is already used inside the apartments.
Connections of gas pipes
An important detail in the connection of gas pipes is their cross section. That is, in the case of ½-2 in. Cross-sectional dimensions, welded pipes of threaded steel are used. In the case if the cross section exceeds 2 inches, seamless seamless steel pipes are used. They go in a special jute shell. The connection at them goes threaded or bell-shaped. The combination of gas-pipe steel pipes is similar to that of water-conducting elements. Special fittings are used for this. In order to compact the joints, you should use a special hemp fiber, which can be impregnated with linseed oil or linseed oil. Also, there are limitations: seals, which make it difficult to disassemble pipes, can not be used strictly.
Also, when the pipes are combined, the floor cranes, which are installed, are not compacted. In doing so, all elements must fit tightly.
In the case of repair work, the inspection of the gas pipes at the end must be mandatory. To do this, it is necessary to supply air to the pipes under pressure, which is several times higher than the gas pressure. Be sure to close the bends before checking. In the end, if within 5 minutes the pressure falls by more than 20 mm.v.s, it will speak of loss of tightness. Most often it happens at the junction, but you need to check the entire pipe section.
What in the end?
The fittings that exist for gas pipes are a durable and reliable connection, but they should be chosen correctly. They should be as tight as possible to the pipes, but do not have an extra seal. It is also possible to connect gas-conducting elements by welding. Depending on the material from which the products are made, the welding method and the welding machine are selected. In the case of steel pipes it is standard electric, for polymers the apparatus is easier to handle and requires less expenditure.
In any case, working with gas pipes, it is necessary to be extremely careful and cautious, especially when it comes to correctly connecting the elements.