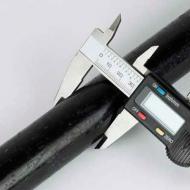
Soldering polyethylene pipes end to end and using an electric coupling
Today, products made of polymer materials are used in many areas of our lives and industries. But especially popular is HDPE - low pressure polyethylene. This material is distinguished by its durability, durability, thanks to its low specific gravity it is easy to install. Polyethylene pipes often make pipelines for various purposes. Welding of HDPE products is performed to connect individual blanks. In this article we will talk about the varieties and features of welding pipes from HDPE.
Types of connections
For the connection of polyethylene pipes, the following methods can be used:
- Plug-in connectors. To perform such a docking of blanks from HDPE, steel flanges will be needed. The main feature of this principle of docking is that during the operation the pipeline can be disassembled.
- Non-removable. In this case, disassemble communications will not work. To make such a connection, the blanks must be welded. For this, one of the following methods can be used:
- butt welding of polyethylene billets;
- welding of products from HDPE by means of couplings.
To assemble pipelines from large diameter elements, thermoresistive fittings or butt welding are used. When using both, a reliable monolithic connection is obtained.
Butt welding of HDPE products
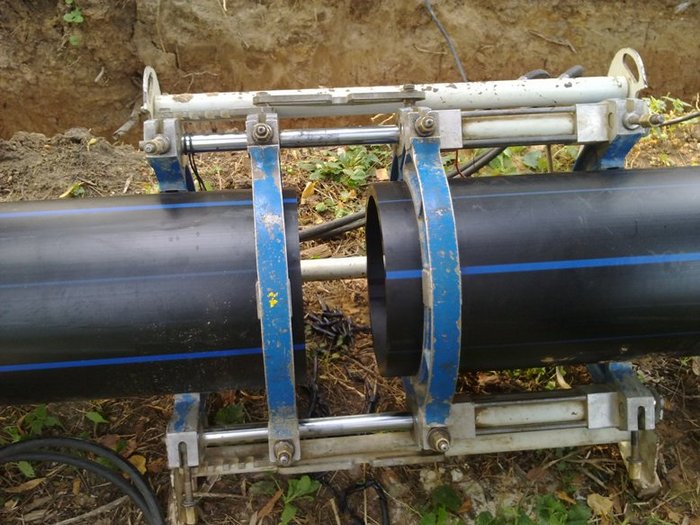
Butt welding of HDPE pipes requires the use of welding equipment. Due to the fact that additional parts are not used during welding, the installation process is much simpler. In this way, only blanks from HDPE can be welded.
Attention: quality butt welding of products from HDPE will be obtained only on the condition that it will be performed by means of a single seam. Due to this, the durability of joining of the parts to be joined will be maximum.
Welding of polyethylene butt-end pipes is the most effective and versatile technology, because at the same time the flexibility of the material is maintained throughout the pipeline. This method can be used regardless of the type of pipeline laying used (trench, trenchless or open).
Soldering of polyethylene pipes is performed in the following order:
- To begin with, the ends of the blanks to be joined must be installed in the centralizer of the welding equipment.
- After the parts have been aligned and fixed, use cotton wool and alcohol to clean the ends of dust, dirt and grease.
- Then the ends to be welded are processed with the aid of a fusing device. End trimming is stopped when uniform chips with a thickness of no more than 0.5 mm begin to form. Now the workpiece can be extracted and checked by hand parallelism of the ends.
- If an unacceptable gap exists between welded surfaces, the trimming operation must be repeated.
- After this, soldering of pipes is carried out. To do this, with the help of a heating element with non-stick coating, the ends of the workpieces are heated to the required temperature.
- When the ends are sufficiently melted, the welded products are bred, and also we remove the heating element from the weld zone.
- After that, the welded ends can be closed and the pressure of the clamp increased until it reaches the required value.
- The welded seam should be kept under pressure for a specified period of time.
- After that, the quality of welding is checked. To do this, assess the appearance of the grate, width and height.
Muff welding of blanks from HDPE
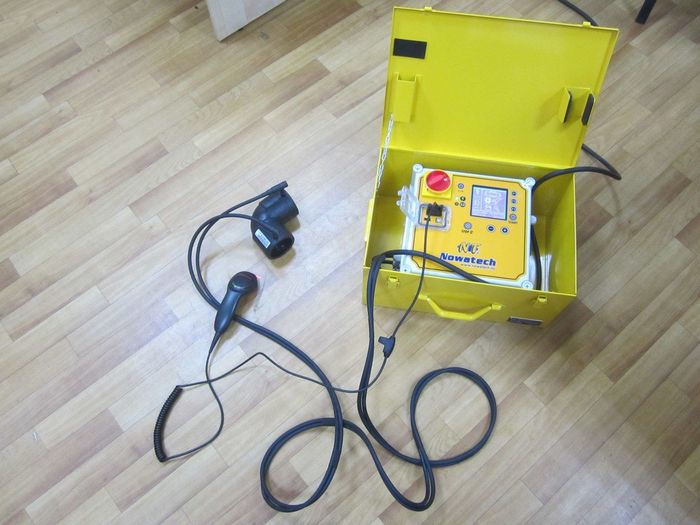
Welding of HDPE pipes by the muff method is carried out with the help of a special welding unit called a soldering iron, as well as a set of special nozzles that can differ in diameter. The size of the nozzle is selected, based on the diameter of the welded polyethylene pipes.
Coupling soldering of pipelines from HDPE is carried out with the use of fittings. The configuration of these products can be different. They can be in the form of corners, tees or couplings. With this method of soldering, the ends of the blanks and fittings are welded.
Important: the main advantage of coupling welding is that it can be carried out in hard-to-reach places where axial displacement of blanks is difficult.
Heating of polyethylene parts is carried out by contacting the workpiece with the heated metal part of the welding unit. It consists of two twisting parts:
- the mandrel heats the inner surface of the fitting;
- the heating pipe is inserted into the sleeve.
To install this nozzle into the hole of the soldering unit, the sleeve and mandrel must be twisted together.
Soldering of polyethylene pipes with a muff method involves the following preparatory measures:
- The workpieces must be cut using special scissors to the desired size. It must be ensured that the cut is strictly perpendicular to the longitudinal axis of the product.
- Before soldering, the ends of the blanks to be joined must be cleaned.
- To prevent undesirable cooling during the welding process, the ends of pipes that are not currently being connected are closed with plugs.
- After that it is necessary to clean the surface of the nozzle for welding from the particles of material that could remain after the previous work.
Now you can proceed to the very process of welding, which is performed in this sequence:
- First, the nozzle must be heated to the welding temperature. When the value reaches the required level, the indicator on the body of the soldering iron will signal.
- After that, the HDPE pipe must be inserted into the sleeve until it stops. In turn, the fitting is put on the mandrel as far as it will go. Since the diameters are slightly different, some effort will be required to perform the procedure.
- We select pipe welding time according to special tables, where this index is indicated for products of different diameters.
- During the insertion of the tubular element and the fitting of the fitting, the surplus material from the surface of the preforms is melted and extruded outward. As a result, an annular roller is formed along the edge of the welded elements.
- Pressing when inserting parts should be stopped at the moment when the workpiece and the fitting reach the stop. It is very important to comply with this condition, because otherwise the connection will not be strong enough. Since it is difficult to accurately determine the depth of the workpiece immersion, it is necessary to measure this value in advance and mark the pipe.
- Then remove the welded workpieces from the nozzle. After this, install the pipe into the fitting in such a way that it is firmly seated in the ring roller. Allow the connected components to cool. In this case, do not twist them and subject them to various mechanical influences.
Electrofusion welding
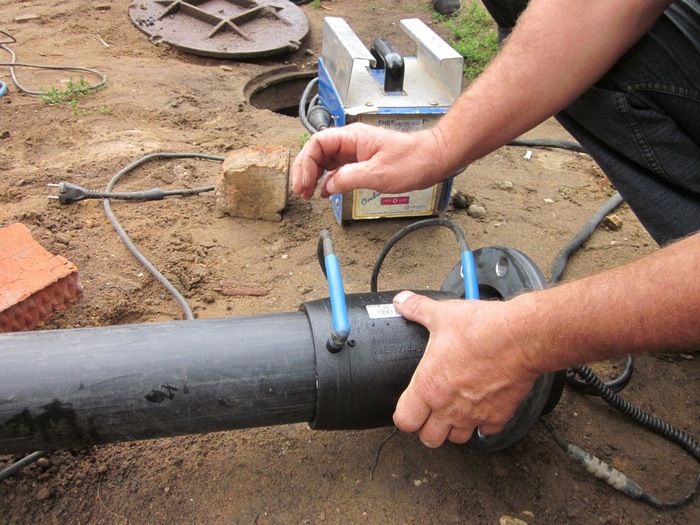
To perform such a connection, a special electrical coupling is needed, into which the embedded heating elements are mounted. If you compare this welding to the butt, it will cost more because of the need to purchase expensive electrical couplings.
However, this technique has its advantages:
- Since no grate is formed on the inner surface of the pipes, the permeability of the pipeline does not decrease.
- This method of welding is convenient to use in a limited space, where you can not install the overall welded aggregate.
To connect the two blanks to the rectilinear section of the pipeline, use conventional electrical couplings. However, in some cases, it may be necessary to use electrofusion tees and saddle bends. To perform the work you will need an electrofusion unit for welding.
The welding procedure is carried out using a polyethylene welded fitting. This is a special product that has built-in spirals, which serve as heating elements. At the same time, part of the material of the fitting, which is melted by a heated spiral, is connected to the polymer material of the workpiece, forming a solid monolithic pipeline. By the way, the spiral remains in the received seam forever.
Important: Electrofusion technology makes it possible to obtain a compound of high strength. However, because of the high cost of this method, it is used in the installation of pressure communications for the transportation of gas and petroleum products.
Welding electrical couplings is carried out in the following sequence:
- With the help of special cutting equipment, the pipes are cut into pieces of the right size.
- Next, the blanks must be cleaned of dirt and degreased at the welding site. The same treatment should be subjected to the electrical coupling.
- Then, on the tubular elements, marks are made that will allow to control the depth of insertion of the pipe into the coupling.
- To prevent unwanted cooling of the elements during the welding process, the free ends of the pipes are muffled.
- Using special wires, the welding unit is connected to the electrical coupling, the start button is pressed.
- After a certain period of time, the unit will turn off automatically, which will mean the completion of welding.
- The compounds thus obtained can only be operated after an hour.
Attention: the main condition for obtaining a quality weld is the immobility of the parts in the process of welding and cooling.
The following requirements are imposed on the welded joints obtained:
- The annular bead of the welded seam should overlap the mark made on the workpiece before welding.
- The permissible displacement of pipe segments relative to each other is no more than 10% of the thickness of the walls of the HDPE element.
- If the thickness of the walls of the welded workpiece is not more than 5 mm, then the height of the roller for a qualitative weld should be approximately 2.5 mm. In the case of welding pipes with a wall thickness of 6-20 mm, the height of the roller should be more than 5 mm.
When choosing the method of welding the blanks from HDPE, it is necessary to take into account the operating conditions of the engineering utilities being installed. Only taking into account this factor, it is possible to perform a reliable and high-quality pipeline, which will effectively work all the time allotted to it.
The range of construction products is growing every year. In the market there are modern materials that facilitate the construction stages, and increase the productivity of workers. Consumers tend to use pipelines with a long service life when planning internal systems in homes. A suitable alternative that meets consumer demands is the branch of internal communications from plastic. How to solder plastic pipes?
Another advantage of such technologies is the emergence of the ability to independently repair or replace water supply and heating networks. How to solder plastic pipes for water supply?
Let's look at the types
Metal-plastic
Polyethylene
Such communications are subdivided into subspecies:
- Polyethylene - are used for laying out broods inside buildings and external routes. It is possible to use them on high pressure pipe connections and at low ambient temperatures.
- PVC is used to reduce the cost of repairs.
- Metal-plastic - the most practical products, the useful life of more than 50 years. Ideal for replacing hot water.
The wide application of this material is due to a number of reasons. The positive properties of such structures, in contrast to metallic ones:
- Long service life.
- Low corrosion.
- Easy to install.
- Does not require special skills.
- Environmentally friendly material.
- Economical and affordable in use.
- Light and easy to transport.
- Not susceptible to harmful effects of microorganisms.
Your water supply system
Coupling assembly
Polyethylene models are mounted by the spike method or by means of couplings / fittings (coupling assembly). How to solder plastic pipes for water supply?
To conduct new water supply networks, PVC and polyethylene products are suitable without reinforcement and reinforcement. Preparation requires the creation of a scheme of future water supply with the indication of the lengths of branches, its position and all necessary fittings for installation. Correct calculation of the lengths and number of bends will simplify the technology, increase the speed of the task and prevent rework.
Soldering iron
Truborez
For soldering polyethylene connections you need:
- Soldering iron.
- Truborez
- Trimmer for cutting pipes and cutting edges of cut ends.
- Chalk stripper paper
- Coupling (if coupling)
The heating device is a special device with a sole with attachment to it of special nozzles of various diameters. There are devices that come with two or more nozzles at the same time.
The stages of the technology of laying hydrocommunications will tell you how to learn how to solder:
- Measure the tape with the required length.
- Cut the cutter length.
- Snag the cut ends. This is an important step in the process of soldering. Sections should be smoothly sanded and cleaned. For more confidence, you can also degrease the alcohol solution.
- We are getting rid of the ends. If, when installing life support networks, a coupling is used, then at one end of the structure we install the coupling / fitting and warm up together with the future return in the nozzle of the desired diameter of the soldering iron. After warming up the ends immediately connect and wait for the complete cooling of the assembly. The presence of the bead indicates the quality of welding.
Attention! When installing heat and water supply with a splice seam, it is strictly forbidden to drop water or moisture in the cavity or on the surface. When heated, water, turning into steam, deforms the plastic structure, as a result of which it loses its strength.
What to look for
The temperature modes for soldering are described in the instructions to the tool. On modern products automatic heating mode is installed depending on the size of the installed network and the depth of welding. On previous grades, the heating force was selected manually.
At what temperature should plastic pipes be soldered? With the adhesion of polyethylene risers, we set the temperature regulator around 220 ° C, for polypropylene - 260 ° C. On the heating mechanism there is an indicator that indicates the readiness of the device for use. The indicator lights up only in heating mode.
The duration of soldering depends on the circumferential radius of the pipeline, and can range from 5 to 40 seconds. Do not overheat the ends. This can cause the formation of a blockage in the place of adhesion.
If you want to install a single-size water supply, you should not overpay for the number of nozzles and the presence of a temperature mechanism.
If a large volume of long-term production is planned with the use of networks of various sizes along the circumference, we acquire a universal device for connection with the latest technical capabilities and characteristics.
Nuances of soldering
Know the technology of joining autonomous communications is not enough. For high-quality installation you need to know a number of features of laying and soldering housing branches. How to solder plastic pipes? To ensure the professional assembly of technological structures, it is necessary to remember some nuances of the connection:
- For the soldering assembly provides a warm-up time. This time is from 5 to 20 minutes.
- The production of house-to-house life support should be carried out at a temperature above zero.
- After the soldering of the ends it is required not to allow them to be scrolled or moved, it is enough to exclude the distortions smoothly. You need to let them cool. The scrolling of the joint can lead to leakage in the future. For cooling, it takes the same amount of time to solder it.
- The required power of the soldering tool is 1200 W.
- Home soldering irons are designed for soldering up to a diameter of up to 32 cm. If you need to assemble large diameter products, then we purchase a professional device for soldering.
- There should be no gaps between the edge of the pipeline and the internal thread of the fitting. Gaps may leak at high water pressure. Excessive force when compressing the elements can lead to a decrease in clearance in the cavity and worsen the work of the entire structure.
- Remove residual material from the nozzles after each produced pack. Since the nozzles have a special coating, remove the carbon should be a wooden device to avoid damage to the integrity of the surface. Scratches on the surface of the nozzle will worsen the technological characteristics of the device and will render it unfit for further use.
Do you think how to make heating?
The installation of heat supply has a number of difficulties. The device of heating models can be carried out in premises with low temperatures, which complicates the soldering process. For heat supply systems are developed depending on the temperature of the water supplied to the system and the operating pressure. The use of plastics in construction has increased productivity, and reduced costs for the necessary material.
Pipes for heating are reinforced with fiberglass, which makes this material durable and durable.
Health and working conditions
In the manufacture of works related to heating joints of the heating main, we comply with the safety rules to exclude injuries and burns:
- We solder in special protective gloves.
- We follow the cleanliness of the floor in the room. Dirt adversely affects the quality of welding and the appearance of the entire structure.
- The soldering iron is installed on a flat horizontal surface.
- To get started, it is necessary after the device has fully warmed up, after turning off the ready indicator.
- The seal is not switched off from the mains during the entire installation.
It is not difficult to solder the plastic pipes with your own hands. The soldering process does not require the presence of professional skills or experience. Everyone can install life support networks in his own home. The required composition of the required tool includes only the soldering device. Other auxiliary tools can be replaced with improvised tools, a pipe cutter with a sharp knife. Pipeline from polyethylene constructions and PVC is a reliable, durable and environmentally friendly system for supplying water and heating.
Video recommended: Secrets of mounting polypropylene pipes
Helpful information?
The modern sanitaryware market pleases consumers with the choice of the most suitable option, but at the same time requires knowledge of the properties of materials and the ways of their installation. The quality of the pipeline largely depends on the quality of the connection of the individual elements, the most reliable, durable, hermetic of which is soldering.
Soldering copper pipes is not an easy task, you will need a special toolBrazing of copper pipes
Copper is not cheap metal, but the pipeline from it has competitive advantages, allowing to remain copper systems at the peak of demand. Competently conducted from copper will ensure a long and trouble-free life of the water distribution throughout the life of the house, exceeding half a century. The practicality of processing such products is the simple soldering process - it is low-temperature, easily carried out in a domestic environment with a gas burner or an electric soldering iron.
Set of tools
A complete set of tools, tools and materials used in the process for soldering are as follows:
- means for expanding, cutting and stripping of pipes: an expander, a pipe cutter or a grinder with the thinnest disc, a facet scraper, a sanding pad, a metal brush;
- tool for heating the metal and melting the solder: burner gas or electric soldering iron for 250 W;
- materials with which the connection occurs: flux and solder of tin alloy with copper, antimony, silver or other additives;
- auxiliary materials - napkins for removing excessive flux, supports, gloves, measuring and marking tools.
Copper tubes are connected without fittings - the edge of one expands with the help of a pipe expander, another segment is inserted into it. The connection is heated, and the seam is poured with molten tin solder - a reliable sealed joint is obtained, capable of withstanding a sufficiently high pressure and high temperatures. Correctly to solder pipes from copper it is possible, having understood with principles of an occurring process:
- after cutting the tubes before soldering, the ends are carefully cleaned - all burrs are removed, and the edge is ground to a bright yellow color. This must be done in order to remove oxides from copper, which prevent soldering;
- after stripping is covered with a special composition - flux, which removes oxygen, preventing oxidation during welding, helps the molten solder penetrate deep into the joint;
- flux-covered segments are put on top of each other and heated with a burner or soldering iron. The soldering technique in this case differs from the work of the burner only in the absence of an open flame;
- to the heated surface under the flame, solder is brought - the tin melts, is tightened into the joint, evenly spreading along the circle of the joint;
- after cooling, the excess of tin will fall off, and the seam will be sealed tightly.
Council. In everyday life, it becomes necessary to connect aluminum tubes, which are more difficult to process than copper. This will require aluminum solder and equipment for soldering aluminum - a burner capable of heating the metal to 400 ° C. Specificity of the procedure is that the flux is not used, and the solder is not injected into the flame, but is applied to the joint: it melts from contact with the hot metal.
Soldering pipes from polypropylene PVC (plastic)
Polymer products are brazed at lower temperatures than the metal. They are afraid of an open flame, so special electric soldering tools, called welding machines, are used for welding.
Technology of welding products from polypropylene (PP) is fundamentally different from working with copper. The joining of the metal sections is the insertion of one piece into the other, and then the sealing of the seam by means of a weld of a softer metal. In the case of polypropylene, both segments are melted, mixed, completely penetrated one into the other, and when solidified, an intact homogeneous compound is formed. Such welding was called diffuse from the Latin word diffusion, meaning mixing. Soldering propylene pipes means to perform three actions:
- melt the ends of the segments to a soft state;
- connect one with the other without unnecessary turns;
- wait until cooling - as a result, a uniform, one-piece section is formed.
Soldering pipes for heating and running water at home
Due to the simplicity of the procedure, they are carried out at home in their own hands. For this you need to purchase:
- welding machine electric for welding polypropylene;
- attachments to the device (included in the kit for the device);
- face;
- fitting;
- accessories: marker, knife, tape measure.
Soldering of propylene pipes by one's own hands consists in the sequential execution of the following operations:
- Cut pipes according to predetermined dimensions, if necessary, prepare fittings.
- Prytsevat ends - remove from the top 1-1,5 mm protective layer. This can be done with a face trimmer or by sanding with sandpaper.
- Prepare the welding machine - equip it with nozzles along the diameter of the pipes and plug it into the network. Polypropylene melts at a temperature of 250 ° C. The device has a temperature relay and a heating indicator. When the desired temperature is reached, the device delivers an audible or light signal indicating that the welding process is ready.
- Insert the pipe and fitting in the appropriate nozzles and maintain the time strictly according to the instructions, avoiding neither overheating nor underheating.
- Remove the heated parts from the nozzles, then solder by inserting one element into the other. At this stage, the actions must be confident and clear - it is forbidden to move the elements back and forth or rotate along the axis.
- Allow the polypropylene to cool down - leave the structure for a while without mechanical influences.
- Check the connection visually for defects: if the technology is observed, the seam will be uniform and durable.
Correct soldering of large HDPE polyethylene pipes at normal temperature
They are of two types:
- low-strength - are manufactured under high pressure and acquire a low density;
- high-strength (HDPE) - are manufactured under low pressure, but acquire a high density.
Another name for high-strength polyethylene pipes - HDPE is deciphered as low-pressure polyethylene. The words "low pressure" in the name mean the conditions under which the products were manufactured and are not relevant to the sphere of application. Low pressure polyethylene (HDPE) is used in high pressure and temperature conditions in gas or water mains. Properly soldering polypropylene pipes is not an easy task.
Since HDPE products are produced in a wide variety of diameters (20 mm to 1 m 20 cm) and wall thickness, there is not one method of connecting them and many types of equipment for soldering polyethylene pipes. Welding of polyethylene pipes is carried out by one of the following methods:
- butt (or butt);
- bell-shaped;
- electromotive.
Welding of butt-end pipes in industrial conditions is produced by an expensive and bulky machine with a mechanical or hydraulic drive. The set of the device includes guides for centering, a face for smooth cutting of the edges to be joined, a heating element, drives and timers. By itself, butt-end technology is simple, but the equipment is not cheap: the price of a welding machine for pipes is an average of 250 thousand rubles, and about 50 thousand is a separate heating element.
Soldering scheme for polyethylene pipes soldering iron in hard-to-reach places
Soldering of polyethylene pipes occurs according to the following scheme:
- the joined products are inserted into the tube welding machine, mn, centered;
- between them is inserted an automatic trimming device, which evenly cuts the HDPE, removing the shavings;
- opposite ends are joined, visual control of alignment and tightness of the edges;
- the welded ends are degreased, a heating element is installed between them;
- there is heating and melting of the ends at a given temperature for a certain time;
- the heating element is removed and the connection cools down during the period specified by the timer;
- a strong connection is obtained, which does not affect the flexibility of the pipeline.
Home conditions occur on the same principle, but the devices used are simpler - a soldering iron for polyethylene pipes. Costs from 30 thousand rubles, is a welding mirror, coated with Teflon and capable of withstanding high temperatures - up to 300 ° C.
Parameters for welding polyethylene pipes end to end: temperature, heating and cooling time - depend on the diameter and thickness of the walls, they are exhibited by welders on a special table. To avoid errors in many devices, the parameters are set automatically.
Electrofusion welding of tubes is an industrial type and consists in melting a section of the pipeline under the clutch, to which the electric current is fed, and the temperature rises. Electro-couplings for polyethylene pipes consume a large amount of electricity at work and are considered more expensive, but they help out in cases where it is impossible to use the device with large dimensions. They can be used at home.
Soldering of pipes from reinforced polyvinyl chloride
You can solder using the same apparatus used for welding polypropylene analogues. The walls of PVC products are thicker and harder, so fittings are necessary for their connection. Their melting point is lower, therefore this species is not used for hot water supply - the walls of the pipeline are deformed under the influence of high temperatures. Soldering is carried out by an electric welding machine with nozzles on which the ends of the joined products are melted. To properly solder PVC pipes, you need to do several things:
- clean edges;
- reinforcement, if any, remove;
- the melting point should not exceed 200 ° C.
Tools, devices, sequence of actions are the same as when working with polypropylene samples.
SEE VIDEO
Polypropylene, polyethylene or PVC pipes in everyday life are often referred to as one common word plastic, and the principles of their connection have much in common. Correctly to solder pipes is able not everyone, but everyone can learn.
Pipes based on plastics are an excellent substitute for steel, concrete and others in the construction of sewage and gas mains. Soldering of polyethylene pipes is used to obtain a high-quality one-piece transport system.
Usually soldering is carried out by a butt or electric clutch method. Both technologies have a common physical principle. It is based on the action of interpenetration of molecules, from two connected surfaces of PE or PVC products. However, there are a number of significant differences between these two technologies. In order to expand all the features of butt and electrofusion welding, we will consider them separately.
Technology of soldering pipes from polyethylene to butt
Butt soldering is most in demand when installing pressure pipelines, sewerage and gas pipelines. In order for welded joints to meet the strength characteristics, at the preliminary stage, the conditions for joining the welded parts should be fulfilled:
- installation of pipes can be carried out if they are made of the same material;
- welded pipes must have smooth and clean end surfaces;
- the soldering is carried out under strict alignment of the PE pipes with the use of a centralizer.
Turning directly to welding, you need to take into account the temperature regime of the process. At this stage of installation work, the fact that polyethylene, PVC, and other similar plastics have a significant degree of linear and volumetric expansion when heated, is taken into account. Rapid heating results in an uneven temperature distribution with the formation of large pressure drops at adjacent points in the joint zone, which can cause undesirable stress concentrations within the seam. Further soldering technology for PE pipes is reduced to the following operations:
- With the help of a heating element, which is installed between welded pipes, the ends begin to warm up taking into account the specified temperature regime: HDPE pipes - up to 220 ° C, LDPE - up to 200 ° C. The ends to the heater are manually switched on. Then, using a hydraulic clamp, they are reliably adhered to the thermocouple under a pressure of 0.6-0.8 kgf / cm².
- Having sustained the necessary time, the pipes are diluted to the sides, the heater is removed, and the ends of the pipes are connected at a pressure of 1.0-2.0 kgf / cm², depending on the polyethylene grade.
- The last operation - cooling the seam, occurs naturally when the pressure is held for a certain time.
- At the end of the technology, the strength of the welded joint, its size and the configuration of the bead are checked. After removing the pipe from the clamps, the seam is marked, assigning a serial number to it.
Throughout the process is constantly monitored by pressure and time. Change and reconciliation of these parameters occurs according to the cyclogram.
Electrofusion method is used when pipes have different wall thicknesses. Scope of application: low pressure pipelines (drainage, gravity sewerage), tie-in into already laid pipeline, repair and replacement of elements. The main difference of the coupling from the butt joint is the better soldering of the pipes with a significant difference in their diameters.
Another advantage of such soldering is the speed, ease of operation and the ability to conduct them in small areas. The principle of welding with the use of electric clutches is the melting of the ends of the pipes by the embedded metal spiral, and the technology of this process looks like this:
- the ends of HDPE or LDPE pipes are cleaned of dirt and degreased;
- on one of the ends of the pipe is put on the electrical coupling and clamped by means of the positioner;
- after aligning the ends of the pipes, the coupling is shifted back so that the joint is exactly at its center;
- the operating voltage is applied to the clutch terminals, the heating process is carried out automatically;
- the soldering is considered finished according to the readings of the fitting holes from which molten polyethylene should appear;
- the cooling of the seam should pass without forced cooling in the state of complete immobility.
Plastic pipes PE and PVC confidently replace the metal in everyday life and industry. This is due to the fact that they often exceed the latter by such characteristics as chemical inertness of the material, relatively easy installation, ease of maintenance, insignificant local resistance in the highway, and a long warranty period of service (up to 50 years). With regard to technology, it should be noted that soldering PE pipes requires a significant degree of culture of installation work and a good knowledge of the subject. This issue can be solved by training specialists on the basis of specialized educational institutions.
Pipes made of polyethylene HDPE are used in almost all modern communication systems, from water supply to gas pipelines and channels for cable pulling. They are durable, elastic and wear-resistant. Correct installation of the pipeline system from polyethylene will ensure its reliability even in the places of joints of pipe segments, and knowledge of how to connect HDPE pipes by oneself will save money for their installation.
Types of piping systems from HDPE
From polyethylene of low pressure pipes for different purposes are made, which go for the installation of the following systems:
- Water supply,
- Gas,
- Sewer,
- Drainage,
- Casing for the device of water wells,
- Insulating for power or coherent cable.
IMPORTANT! The HDPE pipe can be used both for internal communications and for the installation of external highways in open spaces and underground.
Installing the pipe into the system
HDPE pipes are produced in standard lengths - 6 and 12 meters in length, as well as in coils or coils of long length - 100-500 meters. During their installation in the system in a particular room, it is necessary to perform the following operations:
- Cutting (cutting) of polyethylene pipes for soldering or fitting. This operation should be carried out very carefully, so that the cut is maximally even, without cracks and burrs, perpendicular to the surface of the pipe. Such a cut can be carried out with the help of:
- A manual or electric pipe cutter, which cope with pipes with a diameter of 15 to 30 mm,
- Circular cutter for domestic pipes with diameters from 15 to 160 mm,
- The so-called "pipe guillotine" used to create a quality cut pipe from 63 to 350 mm in diameter,
- Band saw, which is the most expensive professional tool and can create clean and smooth cuts of pipes up to 1600 mm in diameter.
- Straightening of the rings of the bay into straight lengths is required when buying a large pipe footage. The difficulty is that when straightening the pipe, you can accidentally damage it. Here it is necessary to remember that the pipe material is HDPE, which is a thermoplastic polymer. Therefore, for a small change in shape, it is enough to hold the items for a short time in a warm place (in a heated room, in the sun) or water them with hot water. After that, they will easily bend.
- The formation of an angle by bending straight lines. In this case, more heating of a certain area is required than when the arc is straightened. To do this, use the same hot water, a construction hair dryer or a simple gas burner.
ATTENTION! To bend the HDPE pipe, it should be heated very carefully, as with a small heating it can break on the bend, and too high a temperature can damage it.
Ways of connection
Methods of connecting polyethylene pipes can be divided into two main groups: installation with additional parts (couplings and fittings) and direct welding of joints.
Welding
Welds provide the most lasting permanent joint with full joint sealing, withstanding loads similar to solid surfaces. Soldering is applied to pipes with a diameter exceeding 50 mm and requires a special welding machine.
Welding of segments of HDPE pipe can be carried out:
- Buttock. In this case, a special evenness of the slices and their displacement relative to each other by no more than 10% of the thickness of the pipe walls is required. The work proceeds consistently:
- Sections of pipes are cleaned of all contaminants and degreased (eg, alcohol or other substances),
- Both ends are heated to the viscosity of the polymer,
- The pieces of the pipe are connected with the application of pressure and fixed immovable until completely cooled. In this case, you need to ensure that the seam is smooth, without cavities and protrusions to ensure its reliability.
- With the use of an electrically welded coupling. It also requires an apparatus for working with such couplings that have a built-in spiral and can quickly melt when it is heated:
- The cleaned and defatted ends of the pipe are fixed in the coupling,
- The terminals of the apparatus are connected to the outlets of the spiral before the start of its melt,
- The pipe is fixed until it cools down completely.
How to do it, look at the video.
IMPORTANT! Welded couplings are usually used in hard-to-reach places, where simple welding is difficult: when creating frames or repairing already assembled systems, in wells, etc.
Installation
Direct erection means the creation of detachable joints with the help of fittings of all available types: couplings, angled bends, tees, 4-way pullers, etc. Such joints are usually carried out in systems where the super strength of the joints is not required, or in areas where dismantling and reconstruction may be required (for example, in a private house for connecting an external irrigation system for a summer period).
Unconstrained installation can be carried out in the following ways:
- The connection of pipes with the help of bell-shaped fittings, equipped with sealing rings, for which it is sufficient to simply attach the respective pipe elements to each other and press them well.
- The fitting connection of the compression elements takes place in several stages:
- the clamping nut is tightened on the pipe cut;
- the pipe is put on the fitting fitting tightly to the stop;
- the clamping nut is screwed with the keys.