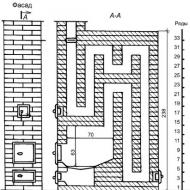
How to properly assemble the fitting of the tube. Application of compression fittings. Types of fittings
Add to bookmarks
Correct connection of polyethylene pipes: types of connections and installation methods
Nowadays PE pipes are especially popular in the building materials market. They are used for the construction of various technological pipelines, engineering utilities for industrial and domestic purposes.
Polyethylene pipes are used for the construction of various technological pipelines, engineering utilities for industrial and domestic purposes.
Most often they are used for cold water supply, transportation of various chemicals, and also as non-passable channels for electric and telephone networks. It is important to make a good connection of polyethylene pipes. Below we will consider the main types and categories of detachable and one-piece connections for PE pipelines.
There are two types of connection of polyethylene pipelines:
- A non-detachable joint by the method of butt or muft welding. Carrying out this connection of polyethylene pipes, heating of the ends of pipelines is carried out with the subsequent docking under pressure to form a continuous seam.
- A detachable connection using crimp connections, compression fittings (collet coupling) and steel flanges. This type of docking is simple, but it is less practical and requires additional costs for the purchase of fittings.
Welding with electrothermal couplings
To perform this type of welding of rolled products from polyethylene, it is necessary to have special couplings and welding equipment. Couplings for welding have heating elements in their body, which subsequently shrink (weld) the coupling. This method is used for welding polyethylene rolled in cramped conditions (pits, trenches). Electro-coupling is able to withstand a pressure of 1.6 MPa. The downside of this method is that it requires much more material costs than a butt.
Scheme of connecting pipes using an electrothermal clutch.
The welding process can be divided into several stages:
- centering of the pipe and the coupling on the required axis;
- preparation, cleaning and degreasing of the external surfaces of pipes at the junction;
- coupling nozzle and connection of the welding machine;
- immobilization of the connection;
- welding with heating, melting of polyethylene and shrinkage of the coupling;
- power off and cooling of the coupling.
Butt-joint with heat application
This type of PE pipe welding is used for diameters above 50-63mm. The butt joint is performed in several stages:
- Before welding, the axes of welded pipelines are aligned in the centering machine.
- After fixing, the end parts of the pipelines are leveled and cleaned of fats, dust and dirt.
- Machining of the ends on the trimming machine.
- Verification of parallelism with mandatory checking of the interplanar gap.
- Heating of the end parts of pipes using a thermal tool.
- Welding followed by cooling.
- Removal of tools, inspection of the outer surface of the welded seam.
Connection using steel flanges
In some cases, when welding can not be performed, flanges are installed. Flange coupling refers to detachable connection types and is most suitable for connecting PE products with pipeline fittings and steel pipelines. Flange joints of pipes are made using adapter sleeves, which are tightly welded to the ends of PE pipes, or with the use of flanges made of metal. Between the flanges must be packed sealing material (rubber, polyester, etc.). The advantage of this method of installation is that in the future it will be possible to disengage the flanges and perform the cleaning of the system. Flanges of water pipes can be flat and profile (with a collar, stop or cone).
Plug-in connection using compression fittings
Connection of pipes without welding is possible with the use of compression mounting elements. Often, this method is used for small diameter pipes (up to 63 mm) and systems with a large number of branches, since any welding will entail an increase in installation costs. Achieving tightness is due to the internal seal of wear-resistant rubber and a cut metal sleeve. To perform the work you will need a set of profile keys and a special knife for a right angle. The collet is capable of withstanding a pressure of 2.5 MPa. The assembly of the connector is easy and simple, the main thing is that the dimensions of the fittings exactly match the size of the water pipes.
Fertilization of pipes is less common. The rolling is connected to the bell, and the tightness is achieved by sealing the bell with a rubber ring. Such mounting is more suitable for non-pressure systems based on polyethylene. Finally I want to note that when choosing the type of PE pipe connection with fittings, it is necessary to take special responsibility for the selection of tools and equipment for installation.
Now you can easily choose the suitable methods for installing conventional and profile polyethylene pipelines without any problems.
Due to the wide popularity of various types of polyethylene pipes, there is a growing demand for docking elements called fittings. HDPE pipe fittings make it easy to install and in a short time. At the moment, enterprises produce many different compounds. Fittings for HDPE pipes are made of different types of polyethylene, copper or brass.
Fittings for HDPE pipes are used:
- For connecting pipes with the same diameter.
- For joining pipes with different diameters.
- To arrange the ramifications provided by the pipeline diagram.
- For mounting pipe turns.
- To install the plug on the PE pipe.
- For connecting pipes with different fittings.
Places for joining PE pipes should be:
- Reliable.
- Durable.
- Waterproof.
- Resistant to possible effects of chemical elements.
Classification of fittings
Professional pipelines installers distinguish between HDPE pipe fittings by:
- Method of installation: compression, welded, electrically welded.
- Stiffnesses: flexible and rigid.
- Connector: detachable and one-piece.
There is another classification of connecting elements:
- Direct, used for docking HDPE pipes of the same diameter.
- Reduction, used for connecting pipes of different diameters.
We will analyze in more detail the first classification of fittings.
Fittings for various pipe connection methods
Depending on the chosen method of installation of the pipeline, distinguish:
- welded fittings;
- electric-welded connecting elements;
- compression fittings.
Welded connecting elements
Welded fittings can be produced in two ways:
- by the method of low pressure, which occurs under high pressure (cast fittings);
- butt welding of small pipe segments (welded fittings).
Welded fittings are available in diameter from 63 mm to 315 mm.
This type of fittings is designed for joining pipes with welding. The low cost of welded fittings causes a wide range of their application. Virtually all branches and plugs provided by the pipeline design can be made with welded connectors.
Most often, welded fittings are used for the installation of gas pipelines and systems in which the temperature of the transported liquid does not exceed 40 ° C.
Electro-welded connecting elements
Electrowelded or thermistor fittings are used to mount the pipeline structure in hard-to-reach places, that is, where it is not possible to conduct conventional butt welding.
Equipped with a heating wire located on the connecting parts. Under the influence of temperature these spirals heat up and melt the polyethylene pipe. After cooling, a strong welded seam is obtained.
Compression joints
Compression fittings for HDPE pipes are designed for joining pipes without using welding. By means of such butt elements, a detachable connection is obtained.
Fittings of this kind consist of:
- polyethylene housing;
- o-rings located at the junction points;
- clamping rings, protecting the connection from mechanical damage;
- bushing, pressing the pipe;
- cover-nuts, securely closing the place of docking.
Produced from various materials. The diameter of the joints varies from 16 mm to 110 mm.
Features of mounting with compression fittings
To properly connect the pipes or make the necessary branches with compression fittings, follow the following instructions:
- The HDPE pipe is prepared and the compression fittings are loosened by several turns.
- The pipe is marked with a marking indicating the depth to which the pipe should be inserted into the fitting. Before installation, it is advisable to lubricate the area of the pipe to be joined, with water or a light soapy solution.
- Before the drawn mark, the pipe is inserted into the prepared fitting. To fully enter the PE pipe into the O-ring, an effort is required. Otherwise, the connection will not be sealed.
- The cap-nut is tightened until the end of the thread.
With the correct installation of compression fittings, a sufficiently strong and tight connection is obtained.
Separation of fittings for joint stiffness
By the degree of rigidity, the fittings are distinguished:
- Tough. Such connections completely exclude the possibility of moving the pipes.
- Flexible, which allows the longitudinal displacement of pipes to 3 - 5 mm and the rotation of the pipes at a small angle. If you use a flexible fitting, all the properties that are necessary for the connection point are kept unchanged.
Flexible connections are most suitable for laying pipelines in the ground, but also more costly. Therefore, they are used only in cases of extreme necessity.
For installation of the simplest systems of pipelines hard fittings are more often used.
Types of fittings
When installing the pipeline, both detachable connections and one-piece connections may be required. This is due to the presence of the joint pipe and its use. For example, HDPE pipes for water supply: fittings at the first stage of installation are used to connect the pipeline to the pumping station. At some point in time, it may be necessary to replace the pump and a detachable connection will simplify the necessary work as much as possible.
Detachable connections
In most cases, the installation is carried out with the compression fittings described above. But there are other ways of arranging this joint:
- Flange connection. The cast or brass flange is attached to the pipe by welding. This kind of connection is mainly used for large diameter pipes or for joining a polyethylene pipe with a metal pipe.
- Threaded connection. Fastening of pipes is carried out by means of thread prepared in advance on pipes and fittings. It is considered the least reliable. Can be used for laying cable conduits or systems with low fluid pressure.
- Flare connection. It is used extremely rarely. It is carried out by fixing one end of the pipe in the expansion of the fitting or the other end of the pipe. It is most often used for laying pipelines for cables.
Brass fittings for HDPE pipes can be used for detachable connections.
Non-detachable connections
Non-detachable joints are most often used to connect structures that are underground or in concrete, since this type is considered the most reliable. Pipe welding can be carried out in the following ways:
- Buttock. The most common method of joining pipes of the same diameter;
- Nest welding. For this method of pipe joining, fittings with an internal diameter equal to the same pipe parameter are used.
- Press or edge welding. It is used for docking pipes with structures, for example, wells.
- Electrofusion welding. It occurs with the help of electrical couplings and is considered the most reliable method of connection.
Molded and electric-welded fittings are used for equipping one-piece connection.
Types of fittings
All fittings differ in their design features and accordingly in their application. Depending on this, the fittings can be divided into:
- Couplings that occur in three main types:
- Equal-pass, connecting pipes with the same diameter.
- Compensating, mainly used to switch to a pipe with a smaller diameter.
- Flanged, used to connect pipes having a large diameter.
- Adapters. With their help, various valves or another type of pipe, for example, metal, are connected to the pipeline.
- Taps. Used to change the direction of the pipes, turn the system. Standard bends are available with a swivel capability of 45º, 66º or 90º. Some firms are engaged in the manufacture of fittings according to the customer's parameters. If a bend with a different degree of angle measure is required for mounting the system, then such a fitting can always be ordered from the manufacturers.
- Sedelka. Are intended for arrangement of various branches. A saddle on a HDPE pipe can be of two types:
- Clamps, crimping pipes from all sides.
- Pads used to cut a new pipeline into an existing system.
- Crossings and tees. They are used for installation of branch pipelines and for connection to the network of other devices.
- Caps. Used to temporarily block incoming liquid or gas into the pipe.
A certain type of fitting is intended for mounting a specific pipeline design.
Fittings are manufactured to facilitate the assembly of polyethylene pipes. Correctly selected set of connecting elements as much as possible shortens the time required for installation of the pipeline system and greatly facilitates the work on connecting the pipes.
Couplings are called fittings designed for a single task - connecting each other segments of pipes and converting them into a single pipeline.
Couplings are different, and the main differences between them are in the materials used and the design itself.
We in this article will consider the PND couplings that create for indoor and outdoor water supply or sewage systems.
Contents of the article
Features and purpose
HDPE as a material is a kind of polyethylene. Polyethylene is called a derivative of the polymer, in fact, it is it.
Polymer products in our time hold the leading positions in the market, which is quite natural, given their common relevance along with amazing characteristics.
Polyethylene is also a cheaper version of the polymer, designed primarily for laying sewers and technical water supply systems.
HDPE is deciphered as low pressure polyethylene. It is produced in special chambers under conditions of low pressure and predetermined temperatures. HDPE is much stronger than conventional polyethylene, it does not abrade, pipes from it have excellent ring stiffness.
At the same time, HDPE pipes and fittings are still as well resistant to external influences of any type, they are easily welded by means of diffusion apparatus and weigh a little.
Muffs from HDPE - is an integral part of HDPE products. Without them, the connection of the HDPE pipes would turn into a nightmare when each piece had to be mounted to the working position and welded by hand.
The peculiarity of interaction between materials imposes certain limitations on us. For pipes of HDPE, couplings and fittings of the same material and the same diameter can be used.
For example, it is reasonable to put back fittings with a diameter of 63 mm and the same material for HDPE products with a diameter of 63 mm. Only in this way will you be sure that nothing will collapse with time, and the working connection will last a maximum amount of time.
As we have already noted, the couplings must fully meet the characteristics of the pipes used on them, and the conditions in the pipeline itself.
Pipes in modern communication systems are by no means the only acting element. Any pipeline conveys the carrier. The carrier is transported under certain pressure and in a certain amount. In order not to overload the system once again, all the elements of the pipeline are selected very carefully. This also applies to couplings.
So, when choosing a connection fitting from the HDPE, it is necessary to watch that it:
- maintained a sufficient level of pressure;
- approached by diameter;
- had the same class of material;
- approached the working temperature range.
These four conditions are not the only ones - but the most important ones. Each fitting at sale is accompanied by the documentation, in which its characteristics are indicated.
Standard PND clutches withstand pressure from 10 to 25 bar depending on the model, their diameters start from 30-63 mm, reach 110 mm and this is only the inner tubes, the outer HDPE pipelines are assembled with couplers with diameters of several hundred millimeters.
One of the most critical conditions is the operating temperature. HDPE as a material - simply excellent, but with high temperatures in its original performance can not cope. Products from it begin to melt and permanently deform.
That is why the PND tries not to use heating and hot water supply as components for pipelines. The same applies to HDPE couplings.
Types and Distinctions
Let's consider the basic versions of HDPE couplings intended for joining pipes. Their main difference is the design. Different fittings are intended for use in different situations, respectively, and their design is different.
Compression polymer clutch
In terms of designs are divided into:
- compression;
- welded;
- electrowelded.
These three groups are most often used. We'll get to know them better.
Compression
Very similar to threaded, only they are rightly considered to be an improved variation of them. The compression fitting is equipped with a special nut that tightens the connection and makes it more reliable.
In addition to the nut there are a lot of seals in them, and the design itself is seriously improved in comparison with standard threaded products.
Nevertheless, the compression HDPE couplings are very common. Their running diameters start from 63 mm and reach 120-150 mm. All that is more - is a rarity, since compression products still do not have the advantages of welded.
Overview of HDPE compression couplings (video)
Welded
The welded coupling is a coupling that is connected to the pipe by welding. Steel and metal billets are welded using a welding machine. This type of connection has its pros and cons.
The advantages include tightness, the ability to weld the coupling in any place, the overall strength, etc. Cons - the inability to do the work yourself. At least you need to have a welding machine, protection and at least minimal skills.
Without a welder when working with metal you can not do. Another thing is the work with the PND. Polymers are welded by simply warming up their parts to the melting point, and then connecting them in a preheated state.
For qualitative welding, it is sufficient to have a diffusion apparatus at hand. The rest is a matter of technique. The resulting nodes are not inferior to the metal in terms of airtightness or strength, but are realized many times faster and easier, and most importantly - completely with their own hands.
Electrowelded
Electro-welded couplings are slightly different from standard ones. Electro coupling - fitting, intended for assembly of lines practically in an automatic mode. This means that it works on its own, you just need to connect the device and install it in the right place.
Electro coupling has a similar shape to the usual variety. It also consists of a solid HDPE body, has a certain diameter, for example, 63 mm. Its main difference is built-in cable housing for heating.
They perform 90% of all work. These cables penetrate the coupling body, and their outputs are installed in two places and are called terminals. Connect the current feeder or portable transformer to the terminals. Current flowing under certain conditions, provokes heating cables, and those in turn warm polyethylene around themselves.
At one point, the polyethylene reaches the melting point. This will be the beginning of the process of welding the electrical coupling. Then everything happens according to the standard procedure. Polymer in the molten form enters into symbiosis with the polymer of the pipe, forming a solid monolithic connection. You do not even need a welding machine.
It is enough to connect the current feeder to the terminals, and then remove it when the process is complete. After 30 minutes the clutch will fully grasp and will be ready for operation.
Under this scheme it is very convenient to work, especially for those who are engaged in external water supply and sewerage systems. The local products have huge diameters. Connecting them by hand is hard and ungrateful work. The presence of HDPE greatly simplifies the work of a person, increases his productivity.
Add to bookmarks
- All-in-one (butt joints with a special welding machine and electrofusion).
- Split (flanged and flanged with a special seal).
If pressure is applied to the pipeline during operation, butt welding or box welding is used. However, the flange connection in its reliability is not inferior to the previous two methods.
Pay attention to the fact that the strength of polyethylene pipes in combination with their plasticity and, in addition, high reliability make their application practically indispensable in places with high seismic activity and in places where ground movement is periodically observed.
The connection of the pipes is done by butt welding.
When the question arises, how is most effective, it is desirable to give preference to one of the following welding methods, which will seem to you the most optimal. If you prefer butt welding, you need to remember that it is produced using a special tool.
Its essence lies in the fact that during the process the ends of the pipes that are connected are heated to a viscosity by a special heating element. After that, the melted ends of both pipes are connected to each other under pressure and allowed to cool down at the junction in a natural way. The ends of the pipes must be cleaned from contamination and degreased before heating.
During operation, it is necessary to pay attention to the heating temperature - it must be kept in the desired mode, the reflow height of the material, the time of heating of the pipe ends and the applied pressure on the joint surface.
After cooling, the weld should be even, projecting to the same height. With this result, you will get the maximum reliability and strength of the seam.
The most popular connection method is butt welding. Pipeline assembly in most cases is carried out by this method. However, it is necessary to take into account another method - electromotive welding, which is no less effective way with each other. During welding in this way, the heating of the surfaces that are joined is due to shaped polyethylene elements. which also melt when heated and solidify the pipes when solidified.
These elements are heated by equipment, the passing current inside which brings to the desired temperature the shaped part. Similar to butt welding, all ends of pipes and parts must be thoroughly cleaned and degreased before starting work.
It is then necessary to check that the fastening elements and pipes are completely immobile from the beginning of welding to the cooling stage. If the branches are to be welded, the clamps must be carefully selected.
Speaking about the advantages of electromotive welding, it is necessary to point out the simplicity of installation, high reliability and strength of joints, small time costs, safety and cost-effectiveness of the method and, in addition, practicality in installation work in hard-to-reach places. This technique has proved to be reliable and simple and has been successfully used for gas pipelines and water pipes.
Connection without welding
Connection with fittings
No doubt, the welding method of connection is reliable and simple, but there are times when it is impossible to use. In such situations it is possible to use a coupler coupling. Couplings, which are produced specifically for polyethylene pipelines, are intended just for a reliable connection of the pipe ends to be joined.
Compression fittings - the so-called these couplings - do not need special equipment for installing polyethylene pipes and can easily be installed by a layman. This method of fastening is especially good in those cases when pipes with a small diameter are used - from 20 to 315 mm.
Since HDPE pipes have low stiffness, pressure pipelines, especially large in diameter, need to be welded together. It fully ensures the absolute tightness of the joints, connecting after the solidification of the pipe tightly with each other in a single unit, which can not be given by a non-welded method in its entirety, because the pipe under the coupling sleeve can undergo deformation with further depressurization.
However, the advantage of compression fittings is the possibility, if necessary, of assembling and disassembling the installed parts, which none of the above welding methods can provide. And the dismantling of joints can be dealt with more than once, and this is by force even not trained for this person. No tools and tools are needed, except for one special key that can unscrew and tighten the nuts on the connecting fittings.
Installation is possible even at low temperatures, and a wide variety of connecting elements of any diameter makes it possible to produce any wiring, branching and turns in the system.
HDPE pipeline for sewerage
The self-assembly of polyethylene pipelines for sewage is quite simple. Pipes with couplings, corners and tees are connected with the use of sealing rubber rings. Pipes with little effort inserted into the socket, if such a seal is not sufficient, the pipes are additionally coated with silicone sealant.
Installation of sewer polyethylene pipelines also does not cause any difficulties: the fasteners on the ceiling or the wall are the simplest locking latches, which must be screwed to the wall with screws. In the event that you do not particularly care about aesthetics, you can simply drive steel pins a little larger in diameter into the holes in the wall, bend their ends and pass the pipes into these improvised staples. With the help of standard fixtures, you can install the pipeline only close to the wall, you can put it a little distance on the pins, which is often much more convenient.
HDPE pipeline for electrical installation
For electrical wiring, the use of both smooth and corrugated polyethylene pipes is equally successful.
In this case, two main features of the IPA are taken into account:
- Elasticity, flexibility.
- Lack of ability to conduct current.
- For wiring the pipeline is laid on the surface of the walls, and hidden (inside the wall), and is used as a cable protection when laying in the soil. In the latter case, corrugated HDPE pipes are more often used. At the same time, special attention is paid to the hermetic docking of pipes.
Correct piping assembly
Tightness can be achieved by one of two options:
- Butt welding or in couplings.
- Hot casing of HDPE pipes in the socket. The heated pipe is inserted with effort into the socket of the previous pipe. So it, locally deformed, fills all internal rough surfaces of the socket, as a result of which the tightness is guaranteed.
Use of polyethylene pipes in the water supply system
Depending on the pressure in the plumbing, the tool you have available and, of course, your motives, inside the room can use not one method of connecting these same pipes.
Application of compression fittings
This is a very popular method of installing small diameter polyethylene pipes for water supply. Compression fittings are produced for pipes with a diameter of up to 110 mm, although in practice they are convenient to use up to a 32 mm pipe, although inside a larger room and not to meet.
Fittings of small diameter are installed manually, even a key is not needed.
The procedure is exactly the same as for the installation of metal-plastic water pipes, only on the site of the split ring a rubber seal is used:
- Prepare the ends of the pipes. They are cut at a right angle, preferably using a special pipe cutter.
- On the pipe put on a sealing rubber ring with a union nut.
- The pipe is inserted into the fitting, then the union nut is screwed onto its thread.
Advantages of such an installation is obvious: it is very simple and makes the connection difficult. Repair polyethylene pipes with such connections can be without complex tools, since a site with a defect is cut from the water pipe, and a new pipe is installed on the empty space at the fittings. At the same time, the connection directly depends on the rubber seal: if it becomes unsuitable, the connection will flow.
Application of fittings for diffusion welding
In this way, polypropylene is also connected. With this option, the fitting of the fitting to the pipe is the same as the installation of polypropylene: the inner surface of the fitting is heated, and on the nozzle of the right size we insert the outer surface of the pipe into the fitting. After a few seconds, the connection is ready.
Using a fitting for welding with a soldering iron
In this case, the connection can no longer be dismantled. While repairing the HDPE pipes, connected by fittings on welding, a special soldering iron will be needed to restore the tightness. However, such compounds practically never flow. Before collecting them, it is necessary to remove the chamfer from the outside of the pipe, since irregularities and scuffing are the reasons why welded joints flow.
Butt Welding
This method of connection is always used when laying HDPE pipes of large diameter. In this case, the technological operations proceed in this way:
- Between the ends of the pipes there is an electric heater.
- After the pipes are melted, the electric heater is removed.
- The connection is ready after the time necessary for the cooling of the polyethylene pipes.
The butt joint is characterized by very high strength (80-90% of the strength of monolithic pipes). The method is undesirable for pipes with walls thinner than 5 mm. However, with the urgent need for HDPE pipes are fused after heating the ends on a conventional gas stove. Although such a trick and leaves a grubby seam outside and inside the pipe, cold water such compounds last for years.
Electric coupling
This method of connection is the same fittings for welding, but in this situation the coupling (any other fitting) is combined with the soldering iron. In the middle of the plastic is a low-temperature spiral, you just need to feed it for heating. This method is simple, fast, but not cheap.