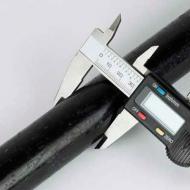
Construction of the pipeline from polyethylene pipes. Laying of pipelines from polyethylene pipes
Add to bookmarks
Construction of the pipeline from polyethylene pipes
Most of the pipelines laid in the cities are still Soviet-era. Deterioration of heating mains, sewerage, gas and water pipelines reaches 70%, which is due to the material from which the pipes are made. This is steel, which is subjected to intense corrosion attack. The construction of gas pipelines from polyethylene pipes is becoming more in demand today. As the life of the pipeline expires, there are many accidents on various pipelines: pipes are bursting at high pressure, numerous leaks are generated that lead to significant water losses. Operational indicators deteriorate: by reducing the cross-section of pipes, their throughput decreases, water becomes contaminated, and its biological parameters are reduced.
Advantages of polyethylene pipes
Pipes made of polyethylene (PE) are a modern alternative to their outdated physically and morally metallic predecessors. They have a number of indisputable advantages compared to products made of steel or cast iron.
- Absence of corrosive damage, which minimizes the costs of installation, maintenance and repair.
- Ease of use: Polyethylene products are easy to cut, so they are simply customized to fit both on the construction site and in the field when laying pipelines.
- High throughput due to the fact that the internal walls of PE products are smooth.
- Pipes made of polyethylene have an elastic structure of internal walls, on which as a result there is no scaling and they are not clogged from within with various suspensions contained in the liquid.
- Polyethylene is chemically inert, successfully resists aggressive attack, therefore, it does not need additional special protection.
- Polyethylene is not electrically conductive, therefore, wandering currents destroying metal pipes are not dangerous to it.
- The bending radius of the polyethylene pipe can be up to 10 of its external diameters depending on the temperature, which reduces the cost of connecting parts and facilitates the design and construction of pipelines.
- The polyethylene pipe has a high flexibility: the minimum bend radius is equal to 25 pipe diameters at 200 ° C.
- Significantly less weight compared to metal pipes, which facilitates installation and laying.
- PE pipes are resistant to temperature changes and have high sanitary and hygienic characteristics.
Scheme of deformation of polyethylene pipes depending on the type of soil.
Important note. Freezing of the ground leads to the movement of pipelines in the vertical plane. These displacements are uneven, resulting in deformations (bends). Forecasting these states, determine how much the bending radius of the polyethylene pipe depends on the level of temperature reduction. In order to determine the radius of bending, it is necessary to make special calculations. Alternatively, refer to the special tables, which indicate the minimum bending radius for a particular type of pipe.
Minimum radius bending pipes made of polyethylene is recommended by the manufacturer for each type and grade of pipes. If you do not get the right bend radius, then you should use bends, tees, etc.
Due to their technological and operational characteristics, polyethylene pipes are widely used: they are used for the construction of new pipelines and for repair of old communications that have served their time.
Sphere of application of polyethylene pipes
Polyethylene products are widely used in modern construction.
They are used in the construction of water pipes, sewerage, gas pipelines. PE pipes are used in pressure and gravity sewage, serve as protective cases for electrical and telephone wires.
With the help of polyethylene pipes, old networks are being reconstructed. Replacement can be done with the destruction of worn out communications, but it is possible to lay new ones in parallel with the old ones, which does not require stopping the water supply of the population and shutting down sewerage. Reconstruction of wells and other communication and sanitary facilities depends on the degree of their deterioration. Partial replacement may be subject to separate parts (necks, shut-off valves, etc.), if necessary, major repairs are carried out with a complete replacement of pipelines.
Installation of polyethylene pipes for sewerage
Sewer networks are internal and external. Their purpose is to collect and transport sanitary and storm sewage, which has a different chemical composition. Any problems on the sewerage sharply affect the quality of life.
Elements and assembly for polyethylene pipes of internal sewerage
Polyethylene pipes for sewerage began to be produced not so long ago, and today they fully meet high requirements due to their inertness to the effects of mineral acids, alkalis and other corrosive substances. PE sewer pipes have a high throughput due to the lack of internal roughness. When installing external sewage systems, frost-resistant PE pipes are used. Installation of internal sewage does not require pipes with such high performance characteristics.
Pipes for sewage are attractive for specialists working on the arrangement of such systems in that their installation is much simpler in comparison with traditional sewerage networks. Installation of internal sewerage communications when using polyethylene pipes does not require complicated special equipment. Polyethylene pipes of small diameter are mounted by means of compression fittings.
The equipment of external sewerage is made by a butt welding method: special welding equipment allows for installation, reducing the number of joints up to five times in comparison with metal pipes for sewerage
Connecting polyethylene pipes
PE products are joined in three main ways:
- contact-butt welding,
- socket welding with embedded electric heaters
- installation by means of compression fittings.
A detachable connection is also possible, which is done by steel pressure flanges. Installation of turns and branching of pipelines is carried out with the use of welded or cast fittings.
Different methods of connection are used depending on the working conditions. If there are conditions for placing the welding equipment, then butt welding is necessary. Butt welding is used when working with pipes of large diameters (from 630 mm).
Limited work space (wells, chambers, trenches) requires electromotive welding with embedded heaters.
If it is necessary to connect pipes up to 63 mm in diameter, compression fittings are used, which creates detachable structures. This connection is easy in operation, has high performance indicators, does not require complicated special equipment. The interconnection of internal piping systems is most often carried out in this way. Their installation is available even for non-professionals.
Piping Laying
Laying of polyethylene pipelines is carried out in two main ways. This is the traditional laying of pipes in an open trench and trenchless laying - the method of deep directional drilling.
Pipelines made of polyethylene with an open method are laid in a trench, the width of which is determined by the need to create conditions for work. The water supply and sewerage equipment requires a trench width of 40 cm more than the outer diameter of the pipeline. These parameters are most often written in the project. Long-length polyethylene pipes are often placed in a trench dug with a narrow-chain chain excavator. In this case, the width of the trench is reduced.
The trench should be properly prepared. Its arrangement depends on the condition of the soil. If the bottom of the trench is solid and dense, then a cushion device is necessary. The bottom is covered with a layer (about 10-15 cm) of sand or other granular material and leveled. At a distance of 2 meters from the inspection well, the cushion is rammed. At the bottom there should not be stones, lumps of frozen soil. When working with loose soil, which has a danger of displacement, it is necessary to strengthen the bottom. In such cases, the bottom of the trench is strengthened by geotextile.
With a flat bottom of the trench with optimal soil characteristics, the pillow is not needed. You can do with a small groove of earth at the base of the pipe at its width and replace it with a softer one.
Backfilling of the trench
The soil removed from the trenching device, in which there are no stones of 20 mm in size, is used for primary dumping. It is produced for the entire length of the tube, about 15 cm high from its top. If it is necessary to compact the soil, the soil must meet certain requirements. You can use gravel fractions (20-20 mm) or crushed stone (4-44 mm). The primer can not be dropped directly onto the pipeline. Layed on the bottom of the trench and the sprinkled pipeline needs to be sealed. The buried soil is trampled by layers of 20 cm on both sides of the pipe, so that its displacement does not occur. Directly above the pipe, the ground is not trampled.
Backfill is made after compaction and getting a tamped layer about 30 cm above the pipe. Backfilling of the trench can be done with extracted soil, the size of the largest stones is not more than 300 mm. Even in the presence of a protective layer about 30 cm thick, the size of the stones in the soil used for backfilling can not be more than 60 mm.
Trenchless laying of the pipeline
In some cases, when pipeline lines intersect with a railway, a busy transport line, a river and another obstacle, an open trench is not possible. The reason may also be the need to minimize the cost of digging a trench. This is the basis for applying the method of trenchless laying of polyethylene pipelines. The method of trenchless laying of horizontally directed drilling (HDD method) has become widespread.
Horizontal drilling is a special way of communicating without opening the soil. The work begins at the point where the pipe leaves the surface. The technology guarantees a high accuracy of the drill output at the intended site to the surface. The method allows to lay underground pipes with a length of more than 100 m and a diameter of up to 630 mm and more. There are two main ways of horizontal drilling: controlled and uncontrolled.
Controllable horizontal drilling is performed by tunneling machines, through flushing and pilot drilling.
Uncontrolled horizontal drilling is performed by two methods: 1) without casing pipes (ram rocket, displacing drilling, auger drilling) and 2) with casing (drilling, piercing, impact drilling, ram drilling).
Methods of horizontal drilling and trenchless laying of polyethylene pipes are considered the most modern technology. To expand the well, a special drilling extension is used. To improve the wiring, the well is treated with a drilling mud, which forms and lubricates the channel itself.
Thus, the characteristics of polyethylene products allow them to be assembled and laid using any currently known method, taking into account those constraints that impose the minimum allowed radius of their bending.
A dragged or pushed polyethylene pipe is able to repeat the configuration of an old track having a radius of curvature of more than 120 diameters of the pipe itself. Metal products have almost no such bending radius.
Organization of installation works
Welding is carried out either according to the basic scheme, or by the route method. The basic method is used in those cases when the object is located near the welding location, where the pipes are pre-connected, and then their ready sections are brought to the pipeline route. The length of the section can reach more than 30 m. In place, they are welded into a single string, which then carefully, so as not to disturb the radius of bending, should be laid in a trench.
Trench welding starts from the trench. Then, installation and welding by mobile welding units is carried out. Pipes of small diameter can be laid in a trench manually. However, most often used pipelayers or cranes. The ready-made thread should be lowered without jerking, evenly, after fixing it with hemp ropes or soft slings, which should be located at a distance of 5-10 meters from each other. The entire welded thread must be lowered into the trench carefully so that the critical bend radius during the stacking process is not exceeded. Preliminary it is necessary to wait at least 2 hours after welding the last link.
Disadvantages of polyethylene pipes
Problems with polyethylene products are associated with the characteristics of all viscoelastic thermoplastics. Their strength largely depends on the degree of bending and compression, and in general it is relatively small. Polyethylene is sensitive to ultraviolet, which has to be compensated with coloring additives (usually a soot) and the use of protective paint. Thermal expansion of polyethylene is quite high and it must be compensated for by constructive G or P-shaped bending of the pipe.
Today, domestic underground pipelines have a length of about 2 million km. Basically, these are steel pipes. The share of polyethylene pipes, for example, is about 10% of the total length of gas pipelines. Other networks also have not very high rates for this parameter. However, there is a strong trend towards the fact that modern pipelines in percentage terms change in favor of polyethylene pipes.
Ministry of Education and Science of the Russian Federation
Federal Agency for Education
East-Siberian State Technological University
Department "Industrial and civil construction"
EXPLANATORY NOTE
TO COURSE PROJECT №1
"Technology of organizing the laying of the pipeline"
Head: KA Boskholov ______________
Completed by D. Yu. Simonov ______________
Group No. 377-1
Admitted to the protection of "__" "__" 2011 ___________
Project Assignment
Introduction
Chapter 2. Calculating labor and machine time
Conclusion
List of sources used
Project Assignment
The laying of a pressure polyethylene water pipeline with diameters of 140 mm and 160 mm, a length of pipes of 5200 running meters, a laying depth of 1.3 meters is carried out. A water supply network is installed on the water supply network, which is located inside prefabricated reinforced concrete wells. They are assembled from prefabricated reinforced concrete rings harvested at the plant of reinforced concrete products.
Introduction
Pipelines are devices that serve to transport liquid, gaseous and bulk substances. Pipelines consist of tightly connected straight sections of pipes, parts, shut-off valves, instrumentation, automation equipment, supports and suspensions, fasteners, gaskets and seals, as well as materials used for thermal and anti-corrosive insulation.
Technological pipelines include all pipelines of industrial enterprises, through which are transported: raw materials, semi-finished products and finished products; steam, water, fuel, reagents; waste products, etc.
Technological pipelines work in difficult conditions. During operation, individual parts of the pipeline are under the pressure of the transported product, which can be from 0.01 to 2500kgs / cm2 and above, under the influence of temperatures ranging from -170 to + 700oC or more, under constant load from the weight of pipes and parts, loads thermal elongation, vibrational, wind and soil pressure.
In addition, in the pipeline elements, periodic loads can arise from uneven heating, pinching of the movable supports and excessive friction in them.
The complexity of manufacturing and installation of process pipelines is determined by:
· The nature and degree of aggressiveness of the transported products (water, oil, steam, gas, alcohols, acids, alkalis, etc.);
· Configuration of equipment and equipment piping, a large number of detachable and non-detachable joints, pipelines, compensators, control and measuring devices, automation equipment and supporting structures;
· Arrangement of pipelines in trenches, canals, trays, racks, overpasses, shelves, technological equipment, as well as at different heights and often in conditions inconvenient for work.
All polyethylene pipes are conditionally divided into several categories depending on their intended use.
First of all, customers are interested in polyethylene pipes for gas pipelines, pipelines and water supply. In this case it is worth considering the fact that polyethylene pipes of pipelines can be used with equal efficiency, both in the development of water systems with constant pressure, and for the installation of sewerage.
Polyethylene water pipes have gained immense popularity around the world, which is due to a number of their unique properties. They have excellent resistance to corrosion, are easy to assemble and very light. Suffice it to say that polyethylene pipes of pipelines have a guaranteed service life of at least 50 years. This figure at times exceeds the analogous figures typical for engineering systems of steel and cast iron.
In addition, polyethylene water pipes are very plastic and absolutely safe for human health and the environment. High ductility allows the use of similar systems in regions with a predominance of low temperatures. In the case of freezing of liquid or other substances supplied through the structure, polyethylene does not break, but only expands, and after thawing acquires its original form.
Despite a number of shortcomings (sensitivity to high temperatures and ultraviolet action), polyethylene pipes of gas pipelines have all chances to become the most used type of pipes in all areas of the national economy. In addition, existing technologies are being finalized and improved, which leads to a continuous increase in the quality characteristics of plastic pipes.
Chapter 1. Technology and organization of works on laying the pipeline
The width of the trench should be determined from the conditions for ensuring the convenience of installation work. When laying water and sewerage, the width of the trench should be 40 cm above the outer diameter of the pipeline. With solid and hard soils on the bottom of the trench, before laying the polyethylene pipes, a bed of sand with a thickness of at least 10 cm should be provided. When laying lengthy polyethylene pipes and digging trenches with a narrow-chain excavator, the width of the trench can be reduced.
The bottom of the trench must be leveled and freed from stones and boulders, should not have frozen areas. With very loose soils, it may be necessary to strengthen the bottom of the trench. In the soil prone to dislodgement, as well as in case of danger of soil washing, the bottom of the trench should be strengthened with a layer of geotextile material to separate such soil from the pipe. The places of excavation of boulders or loose ground in the base should be filled with soil, compacted to the same extent as the ground of the foundation.
Pillows for polyethylene pipes should be arranged for all types of soils. For this purpose, sand or gravel is used (the maximum size of fractions is 20 mm), the thickness of the layer must be at least 10 cm, but not more than 15 cm. The pillow for polyethylene pipes should not be compacted except for the sites 2 meters before the inspection well or To the wall of the well from the side of the inlet pipe. The cushion should be carefully leveled. When laying pipes, pits should be arranged in the places where the butt joints are made.
In order to form and install water supply and drainage networks, it is first of all necessary to use waterways made of polyethylene pipes , taking into account all the advantages of such waterways in front of steel or iron products. An essential flaw in pipes made of metal, especially for steel products, is their short life due to the effects of corrosive processes.
When installing any pipeline system, its performance characteristics will be determined by how carefully and carefully the workers adhered to the technique of installing gutters, of whatever material they were made of - metal or plastic. For each type of pipe there are rules and installation techniques. Laying of pipelines from polyethylene pipes has its own significant differences. First, you need to measure the width of the trench. It should provide excellent convenience for installation and installation of the pipeline. The main thing that must be taken into account is that the width of the ditch should be greater than the diameter of the pipes by about 40-50 cm. Such conditions must be met when laying sewer pipes and when laying water pipes. If the laying of gutters is carried out in strong or dense ground, it is necessary to arrange a sand mound about 10 centimeters wide.
It is extremely necessary to remove from the bottom of the trench any stones, and the bottom must be made smooth and even. It should be ensured that the ground soil on the bottom is not frozen. If the soil for laying the pipeline of polyethylene pipes is loose, then it may be necessary to apply technology to create the effect of strengthening the earth. If there is a probability of soil displacement, geotextiles are laid on the bottom of the ditch to ensure a static position of the water channels in the ground.
The most common installation of a pipeline from polyethylene pipes begins with the laying of a special pillow, which is a kind of material, namely gravel or sand. The thickness of such a pillow can be varied depending on the characteristics of the soil, but on average it is 10-15 centimeters. Seal the pillow only in the vicinity of the manhole. In places where the water pipes are fastened, workers make pits. When the analysis of the soil reveals its ability to strong internal friction, in this case, the pillow can not be stacked. Then, at the base of the track, the hardened soil is seized, and a softer soil is laid out in its place. The seized ground can later be used to fill the pipeline, but it is necessary first to make sure that it does not contain large stones. You can also fill the water supply pipe with sand or fine gravel. First, the backfilling of the pipe is carried out along the entire perimeter, at an altitude of more than 15 cm from its extreme point. If you have to make the soil denser, then fill it in small layers of 20 centimeters. In no case can not ground the ground directly above the drain.
After stacking pipelines made of polyethylene pipes backfilling is most often carried out by the seized land, but it is necessary first to clean it of stones if they exceed 6 cm in size, and if there are boulders, then 30 cm.
Pipes made of polyvinylchloride are fastened together more often by means of glue in the socket. Nevertheless, one must take into account that for gluing it is necessary to scrupulously clean the surfaces and apply the adhesive base very carefully. Do not bend the butt edges. In recent years, for the installation and fastening of drainpipes made of polyethylene materials, flared spikes have become very popular, which are sealed with rubber cuffs of diverse profiles. In this case, drains are produced with sockets, which contain circular grooves inside. If it is necessary to attach polyethylene pipe to steel or cast iron, then it is necessary to use connections from the flange. Where drainage systems from polyethylene gutters are laid through walls of wells, fastening couplings with a single ring of rubber are used as casings.
Welding is made mainly by contact method, it is carried out in the socket or butt-end with shaped sections. When welding polyethylene pipes It is necessary to observe very precisely and to monitor the diameter of the drain and their circumference.
Installation of utility networks can be carried out in several ways. Traditional, and until recently one of the most popular, is the laying of HDPE pipes by trenching. It is a list of operations that are performed in a certain order. The reliability, durability and functionality of communication systems depend on compliance with technology and the quality of work. How this type of installation is carried out, you will learn from this article.
Technology of laying utility networks
Before installing external engineering systems underground, it is necessary to develop a project that reflects the basic parameters of communications. In this case, you should consider:
- soil characteristics;
- the area of the territory where the networks will be laid.
The technology of pipeline laying depends on its purpose, and one of the main characteristics is the depth of occurrence. It is regulated by the provisions of SNiP, and it is determined:
- designation of the engineering network;
- , which depends on the geographical location;
- presence in the ground of hard rocks.
Installation of HDPE pipes for water supply must be carried out at a depth that is not less than 20 cm below freezing of the ground, as the location above can lead to network damage due to low temperatures. If there is no possibility to lay water supply networks at this level, then they should be insulated. Sewer systems should not be buried more than 2.5-3 m.
When laying HDPE pipes in solid and dense soils on the bottom of the trench, preliminary leveled and released from the stones, it is necessary to lay a cushion of sand, the thickness of which should be at least 10 cm. Very loose soil needs strengthening.
Algorithm for laying water supply and sewerage
Works on the installation of water supply and sewerage networks begin with the marking of their location on the site, which is carried out with the help of pegs and twine. Then perform the following operations:
- Excavation. Depending on the volume of earthworks and the possibilities of the owner of the site, it can be carried out manually or with the use of special equipment. In this case, there should be a slope for sewer pipes, equal to 1-2 cm per meter of length.
- Preparation of the bottom of the trench.After removing excess soil, a sand cushion is arranged and compacted with a rammer at the point of joining with the inlet pipe and at a distance of 2 m from the manhole. In addition to sand, fine gravel can also be used. Piling of HDPE pipes on such a foundation will avoid its deformation during further operation.
- Installation of the pipeline.It is performed depending on the selected way of connecting separate elements with the use of the necessary equipment and components.
- Warming of the pipeline.If pipes had to be laid higher than the depth to which the soil freezes, then it is necessary to carry out work on their insulation. To protect the sewer system, you can use a heater in rolls, which wrap the pipeline. As a widely used foam polyurethane, forming a protective shell around the HDPE pipes and reliably protects them from freezing.
- Backfilling.Laying the HDPE pipe in the trench is completed by its closing. To do this, you can use the excavated soil, but you should first remove large stones from it to loosen the dense earth blocks so that they can not damage the communication network. The thickness of the ground layers, which the trench is falling asleep, should not be more than 5 cm. The jigging is performed between the pipe and the walls of the excavation, and above the communications, the compaction of the soil is forbidden.
Cabling
Another option in the world is trenchless technology, for which deep drilling equipment is used. This method is used for the installation of power systems and communication communications. The HDPE pipe in this case serves as a protective case.
Methods of installation of HDPE pipes
The main ways of fixing HDPE pipes in a trench laying are:
- butt welding;
- electrofusion welding.
If it is required that the connection be detachable, then the bell method or compression fittings are used. For turns use welded or cast fittings, tees, bushings for flanges and other shaped products. How to mount HDPE pipes depends on their location and purpose.
Refers to one of the most popular ways of fixing HDPE pipes to each other and is used in those cases where there is enough space for equipment and work. In addition, it is indispensable for the installation of large diameter pipelines. The principle of butt welding is to heat the ends of the pipe and then fix them with each other. To melt the polymer, special equipment is used, while monitoring:
- heating time and temperature;
- the melting point of HDPE;
- value of pressure during operation.
Electrofusion
It is carried out with the help of special designs with a low-temperature electrical spiral inside. After the voltage is applied, it is heated and the pipes are connected to the shaped elements. Electrofusion welding allows to provide high tightness and fixation strength, and is indispensable if the installation of HDPE pipes is carried out in cramped conditions: wells, chambers and narrow trenches.
Compression fittings
With their help receive detachable connections of pipes, whose diameter does not exceed 63 mm. Therefore, most often compression fittings are used when laying internal communications. However, shaped elements with a split ring make it possible to fix pipes of larger diameter.
Fitting of fittings does not require complicated equipment and can be carried out by oneself; it is only necessary to control the applied mechanical force to avoid damage to pipeline parts. In addition, the shaped elements should be positioned so that they are easily accessible.
Connection into the bell
It is used for installation of external non-pressure drainage from HDPE pipes, which are equipped with a sealing ring made of rubber to improve the tightness. To ensure the durability of fixation, it is necessary to clean the plastic from dirt and lubricate the surfaces to be joined with liquid soap or silicone.
For additional protection against moisture, the joints are treated with a sealant.
Compliance with the technology of laying HDPE pipes in the ground will ensure a long and efficient operation of engineering systems without repair work. This will reduce the labor-intensive maintenance of the pipeline and will reduce the cost of its operation.
- Piping Laying
- Backfilling of the trench
- Organization of installation works
- Fast polyethylene pipes
Most of the pipelines laid in the cities are still Soviet-era. Deterioration of heating mains, sewerage, gas and water pipelines reaches 70%, which is due to the material from which the pipes are made. This is steel, which is subjected to intense corrosion attack. The construction of gas pipelines from polyethylene pipes is becoming more in demand today. As the life of the pipeline expires, there are many accidents on various pipelines: pipes are bursting at high pressure, numerous leaks are generated that lead to significant water losses. Operational indicators deteriorate: by reducing the cross-section of pipes, their throughput decreases, water becomes contaminated, and its biological parameters are reduced.
Structure of polyethylene pipes.
Advantages of polyethylene pipes
Pipes made of polyethylene (PE) are a modern alternative to their outdated physically and morally metallic predecessors. They have a number of indisputable advantages compared to products made of steel or cast iron.
Scheme of deformation of polyethylene pipes depending on the type of soil.
Important note. Freezing of the ground leads to the movement of pipelines in the vertical plane. These displacements are uneven, resulting in deformations (bends). Forecasting these states, determine how much the bending radius of the polyethylene pipe depends on the level of temperature reduction. In order to determine the radius of bending, it is necessary to make special calculations. Alternatively, refer to the special tables, which indicate the minimum bending radius for a particular type of pipe.
The minimum bend radius of a polyethylene pipe is recommended by the manufacturer for each type and grade of pipe. If you do not get the right bend radius, then you should use bends, tees, etc.
Due to their technological and operational characteristics, polyethylene pipes are widely used: they are used for the construction of new pipelines and for repair of old communications that have served their time.
LTD DESIGN PRESTIGE
Sphere of application of polyethylene pipes
Polyethylene products are widely used in modern construction.
They are used in the construction of water pipes, sewerage, gas pipelines. PE pipes are used in pressure and gravity sewage, serve as protective cases for electrical and telephone wires.
With the help of polyethylene pipes, old networks are being reconstructed. Replacement can be done with the destruction of worn out communications, but it is possible to lay new ones in parallel with the old ones, which does not require stopping the water supply of the population and shutting down sewerage. Reconstruction of wells and other communication and sanitary facilities depends on the degree of their deterioration. Partial replacement may be subject to separate parts (necks, shut-off valves, etc.), if necessary, major repairs are carried out with a complete replacement of pipelines.
LTD DESIGN PRESTIGE
Installation of polyethylene pipes for sewerage
Sewer networks are internal and external. Their purpose is to collect and transport sanitary and storm sewage, which has a different chemical composition. Any problems on the sewerage sharply affect the quality of life.
Elements and assembly for polyethylene pipes of internal sewerage
Polyethylene pipes for sewerage began to be produced not so long ago, and today they fully meet high requirements due to their inertness to the effects of mineral acids, alkalis and other corrosive substances. PE sewer pipes have a high throughput due to the lack of internal roughness. When installing external sewage systems, frost-resistant PE pipes are used. Installation of internal sewage does not require pipes with such high performance characteristics.
Pipes for sewage are attractive for specialists working on the arrangement of such systems in that their installation is much simpler in comparison with traditional sewerage networks. Installation of internal sewerage communications when using polyethylene pipes does not require complicated special equipment. Polyethylene pipes of small diameter are mounted by means of compression fittings.
The equipment of external sewerage is made by a butt welding method: special welding equipment allows for installation, reducing the number of joints up to five times in comparison with metal pipes for sewerage
LTD DESIGN PRESTIGE
Connecting polyethylene pipes
PE products are joined in three main ways:
A detachable connection is also possible, which is done by steel pressure flanges. Installation of turns and branching of pipelines is carried out with the use of welded or cast fittings.
Types of welding polyethylene pipes
Different methods of connection are used depending on the working conditions. If there are conditions for placing the welding equipment, then butt welding is necessary. Butt welding is used when working with pipes of large diameters (from 630 mm).
Limited work space (wells, chambers, trenches) requires electromotive welding with embedded heaters.
If it is necessary to connect pipes up to 63 mm in diameter, compression fittings are used, which creates detachable structures. This connection is easy in operation, has high performance indicators, does not require complicated special equipment. The interconnection of internal piping systems is most often carried out in this way. Their installation is available even for non-professionals.
LTD DESIGN PRESTIGE
Piping Laying
Laying of polyethylene pipelines is carried out in two main ways. This is the traditional laying of pipes in an open trench and trenchless laying - the method of deep directional drilling.
Pipelines made of polyethylene with an open method are laid in a trench, the width of which is determined by the need to create conditions for work. The water supply and sewerage equipment requires a trench width of 40 cm more than the outer diameter of the pipeline. These parameters are most often written in the project. Long-length polyethylene pipes are often placed in a trench dug with a narrow-chain chain excavator. In this case, the width of the trench is reduced.
Types of laying of polyethylene pipes.
The trench should be properly prepared. Its arrangement depends on the condition of the soil. If the bottom of the trench is solid and dense, then a cushion device is necessary. The bottom is covered with a layer (about 10-15 cm) of sand or other granular material and leveled. At a distance of 2 meters from the inspection well, the cushion is rammed. At the bottom there should not be stones, lumps of frozen soil. When working with loose soil, which has a danger of displacement, it is necessary to strengthen the bottom. In such cases, the bottom of the trench is strengthened by geotextile.
With a flat bottom of the trench with optimal soil characteristics, the pillow is not needed. You can do with a small groove of earth at the base of the pipe at its width and replace it with a softer one.
LTD DESIGN PRESTIGE
Backfilling of the trench
The soil removed from the trenching device, in which there are no stones of 20 mm in size, is used for primary dumping. It is produced for the entire length of the tube, about 15 cm high from its top. If it is necessary to compact the soil, the soil must meet certain requirements. You can use gravel fractions (20-20 mm) or crushed stone (4-44 mm). The primer can not be dropped directly onto the pipeline. Layed on the bottom of the trench and the sprinkled pipeline needs to be sealed. The buried soil is trampled by layers of 20 cm on both sides of the pipe, so that its displacement does not occur. Directly above the pipe, the ground is not trampled.
Backfill is made after compaction and getting a tamped layer about 30 cm above the pipe. Backfilling of the trench can be done with extracted soil, the size of the largest stones is not more than 300 mm. Even in the presence of a protective layer about 30 cm thick, the size of the stones in the soil used for backfilling can not be more than 60 mm.
LTD DESIGN PRESTIGE
Trenchless laying of the pipeline
The scheme of trenchless laying of polyethylene pipes.
In some cases, when pipeline lines intersect with a railway, a busy transport line, a river and another obstacle, an open trench is not possible. The reason may also be the need to minimize the cost of digging a trench. This is the basis for applying the method of trenchless laying of polyethylene pipelines. The method of trenchless laying of horizontally directed drilling (HDD method) has become widespread.
Horizontal drilling is a special way of communicating without opening the soil. The work begins at the point where the pipe leaves the surface. The technology guarantees a high accuracy of the drill output at the intended site to the surface. The method allows to lay underground pipes with a length of more than 100 m and a diameter of up to 630 mm and more. There are two main ways of horizontal drilling: controlled and uncontrolled.
Controllable horizontal drilling is performed by tunneling machines, through flushing and pilot drilling.
Uncontrolled horizontal drilling is performed by two methods: 1) without casing pipes (ram rocket, displacing drilling, auger drilling) and 2) with casing (drilling, piercing, impact drilling, ram drilling).
Methods of horizontal drilling and trenchless laying of polyethylene pipes are considered the most modern technology. To expand the well, a special drilling extension is used. To improve the wiring, the well is treated with a drilling mud, which forms and lubricates the channel itself.
Thus, the characteristics of polyethylene products allow them to be assembled and laid using any currently known method, taking into account those constraints that impose the minimum allowed radius of their bending.
A dragged or pushed polyethylene pipe is able to repeat the configuration of an old track having a radius of curvature of more than 120 diameters of the pipe itself. Metal products have almost no such bending radius.
LTD DESIGN PRESTIGE
Organization of installation works
Welding and installation works with polyethylene pipes are carried out either according to the basic scheme or by the route method. The basic method is used in those cases when the object is located near the welding location, where the pipes are pre-connected, and then their ready sections are brought to the pipeline route. The length of the section can reach more than 30 m. In place, they are welded into a single string, which then carefully, so as not to disturb the radius of bending, should be laid in a trench.
Route welding begins with the laying of pipes along the trench. Then, installation and welding by mobile welding units is carried out. Pipes of small diameter can be laid in a trench manually. However, most often used pipelayers or cranes. The ready-made thread should be lowered without jerking, evenly, after fixing it with hemp ropes or soft slings, which should be located at a distance of 5-10 meters from each other. The entire welded thread must be lowered into the trench carefully so that the critical bend radius during the stacking process is not exceeded. Preliminary it is necessary to wait at least 2 hours after welding the last link.
LTD DESIGN PRESTIGE
Fast polyethylene pipes
Problems with polyethylene products are associated with the characteristics of all viscoelastic thermoplastics. Their strength largely depends on the degree of bending and compression, and in general it is relatively small. Polyethylene is sensitive to ultraviolet, which has to be compensated with coloring additives (usually a soot) and the use of protective paint. Thermal expansion of polyethylene is quite high and it must be compensated for by constructive G or P-shaped bending of the pipe.
Today, domestic underground pipelines have a length of about 2 million km. Basically, these are steel pipes. The share of polyethylene pipes, for example, is about 10% of the total length of gas pipelines. Other networks also have not very high rates for this parameter. However, there is a strong trend towards the fact that modern pipelines in percentage terms change in favor of polyethylene pipes.