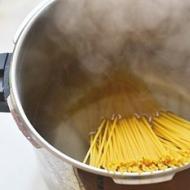
Основные виды механизмов. Рычажные механизмы Смесители с креплением непосредственно на водопроводных трубах
Весьма разнообразны. Одни из них представляют собой сочетание только твердых тел, другие имеют в своем составе гидравлические, пневматические тела или электрические, магнитные и другие устройства. Соответственно такие механизмы называются гидравлическими, пневматическими, электрическими и т.д.
С точки зрения их функционального назначения механизмы обычно делятся на следующие виды:
Механизмы двигателей осуществляют преобразование различных видов энергии в механическую работу (например, механизмы двигателей внутреннего сгорания, паровых машин, электродвигателей, турбин и др.).
Механизмы преобразователей (генераторов) осуществляют преобразование механической работы в другие виды энергии (например, механизмы насосов, компрессоров, гидроприводов и др.).
Передаточный механизм (привод) имеет своей задачей передачу движения от двигателя к технологической машине или исполнительному механизму, преобразуя это движение в необходимое для работы данной технологической машины или исполнительного механизма.
Исполнительный механизм – это механизм, который непосредственно воздействует на обрабатываемую среду или объект. В его задачу входит изменение формы, состояния, положения и свойств обрабатываемой среды или объекта (например, механизмы металлообрабатывающих станков, прессов, конвейеров, прокатных станов, экскаваторов, грузоподъемных машин и др.).
Механизмами управления, контроля и регулирования называются различные механизмы и устройства для обеспечения и контроля размеров обрабатываемых объектов (например измерительные механизмы по контролю размеров, давления, уровней жидкости; регуляторы, реагирующие на отклонение угловой скорости главного вала машины и устанавливающие заданную скорость этого вала; механизм, регулирующий постоянство расстояния между валками прокатного стана, и т.д.).
К механизмам подачи транспортировки, питания и сортировки обрабатываемых сред и объектов относятся механизмы винтовых шнеков, скребковых и ковшевых элеваторов для транспортировки и подачи сыпучих материалов, механизмы загрузочных бункеров для штучных заготовок, механизмы сортировки готовой продукции по размерам, весу, конфигурации и т.д.
Механизмы автоматического счета, взвешивания и упаковки готовой продукции применяются во многих машинах, в основном выпускающих массовую штучную продукцию. Надо иметь в виду, что эти механизмы могут быть и исполнительными механизмами, если они входят в специальные машины, предназначенные для этих целей.
Данная классификация показывает лишь многообразие функционального применения механизмов, которая может быть еще значительно расширена. Однако для выполнения различных функций часто применяются механизмы, имеющие одинаковое строение, кинематику и динамику. Поэтому для изучения в теории механизмов и машин выделяются механизмы, имеющие общие методы их синтеза и анализа работы, независимо от их функционального предназначения. С этой точки зрения выделяются следующие виды механизмов.
Рычажные механизмы. Часть 1
К рычажным механизмам относятся механизмы, состоящие из звеньев совершающих вращательное, поступательное или плоско – параллельное движение. Эти механизмы отличаются простотой, высоким КПД и большой нагрузочной способностью, однако они не могут обеспечить любой закон движения ведомого звена, что в некоторой степени ограничивает их применение в технике.
В технологическом оборудовании широко используются следующие виды рычажных механизмов: механизмы шарнирного четырехзвенника, кривошипно-шатунные механизмы, кулисные механизмы. Рассмотрим примеры и конструктивные особенности рычажных механизмов.
Механизмы шарнирного четырехзвенника
Механизмы шарнирного четырехзвенника в свою очередь делятся на три типа: двухкривошипные, в которых ведущее и ведомое звено могут совершать полный оборот (см. Рис. 1а), кривошипно-коромысловые, в которых ведущее звено кривошип вращается, а ведомое коромысло совершает качательное движение (см. Рис. 1б) и двух коромысловые, в которых и ведущее и ведомое звенья совершают качательное движение (см. Рис. 1в).
Примером двухкривошипного механизма может служить механизм переноса длинномерной заготовки из углового проката со стеллажа на рольганг технологического оборудования, конструктивная схема которого показана на Рис. 2. Он состоит из двух четырехлучевых звездочек 1 и 2, установленных на валах 3 и шарнирно соединенных между собою посредством осей 5 четырьмя ложементами 4, в которые укладываются при переносе заготовки 6, образуя, таким образом, четыре двухкривошипных механизма. При этом валы 3 на подшипниках скольжения расположены в корпусах 7 и 8, которые посредством кронштейнов 9 установлены на общей раме 10.
Еще одним представителем механизмов шарнирного четырехзвенника являются двухкоромысловые механизмы (см. Рис. 3), которые применяется, как правило, для изменения (увеличения, уменьшения) угла качания ведомого коромысла или изменения создаваемого на нем усилия.
На Рис. 3а показан двухкоромысловый механизм, конструкция которого (соотношение длин и взаимное расположение коромысел 1 и 3) позволяет увеличить угол качания β α ведущего коромысла 1. На Рис. 3б показан двухкоромысловый механизм, конструкция которого (соотношение длин и взаимное расположение коромысел 1 и 3) позволяет уменьшить угол качания β ведомого коромысла 3 по отношению к углу качания α ведущего коромысла 1. Если в механизме, показанном на Рис. 3а , ведущим будет звено 3 совершающее вращение с полным оборотом, а в механизме, показанном на Рис. 3б , его ведущее звено 1 будет совершать полный оборот, то эти двухкоромысловые механизмы превратятся в кривошипно-коромысловые. Данные механизмы редко применяются в качестве силовых исполнительных механизмов машин и оборудования, поскольку могут работать только при ограниченной величине углов качания (60 – 90 град.) из-за возрастающей величины потерь при передаче усилий от ведущего звена к ведомому, при увеличении углов качания кривошипов. Такие механизмы обычно используются как вспомогательные, работающие с небольшими скоростями и нагрузками. Рассмотренный тип механизмов часто используется в качестве исполнительного в различного рода кантователях.
Рис. 4. Кантователь для опрокидывания стола формовочной машины.
На Рис 5 показана конструкция сварочного кантователя, поворотные губки
которого являются ведомыми коромыслами шарнирных четырехзвенников имеющих общее ведущие коромысло. Он содержит, установленный на раме 1, приводной пневмоцилиндр 2, шток 3 которого посредствам двуплечего рычага 7, ведомое плечо которого является ведущим коромыслом двух шарнирных четырехзвенников содержащих тяги 8 и 9, шарнирно соединенные с устновленными на общей оси 4 поворотными губками 5 и 6, являющимися ведомыми коромыслами этих четырехзвенников.
Работает кантователь следующим образом. После окончания сварки первого шва изделия 11 подается команда на включение пневмоцилиндра 2, шток 3 которого втягивается и сводит поворотные губки 5 и 6, устанавливая, при этом, свариваемое изделие 11 в вертикальное положение (в это время опорные ролики 10 перекатываются по полке изделия). В результате этого центр тяжести свариваемого изделия 11 перемещается на противоположную сторону опорной призмы (на Рис 5 не показана) и при последующем разведении рычагов 5 и 6, что происходит при выдвижении штока 3 пневмоцилиндра 2, изделие укладывается в положение удобное для сварки второго шва.
конструктивного исполнения механизмов шарнирного
четырехзвенника (см. Рис. в таб.) с описание их работы
Кривошипно-шатунные механизмы
Кривошипно-шатунные механизмы из всех видов рычажных механизмов получили наибольшее распространение в технике благодаря простоте кинематики, позволяющей сравнительно легко преобразовывать вращательное движение в поступательное, что позволяет использовать их в исполнительных механизмах технологического оборудования, например, в механических прессах, и поступательное движение во вращательное, что позволяет их использовать как исполнительный меха- низм двигателя внутреннего сгорания. Кривошипно-шатунный механизм состоит из, установленного в станине с возможностью вращения кривошипа 1 (коленчатого или эксцентрикового вала), шарнирно соединенного с ним шатуна 2, который шарнирно соединен с ползуном 3, осуществляющим при вращении кривошипа 1 возвратно-поступательное движение в направляющих станины 4 (см. Рис. 9).
Рис. 9. Кривошипно-шатунный механизм.
В данном разделе полной версии статьи содержится 9 примеров
конструктивного исполнения кривошипно – шатунных
Кулисные механизмы
Кулисные механизмы – это механизмы, содержащие два специфических звена: кулису и кулисный камень (см. Рис. 16), каждое из которых, совершая вращательное или качательное движение, поступательно перемещаются друг относительно друга. Наличие двух таких звеньев в механизме приводит к различной скорости перемещения ведомого звена, при его прямом и обратном ходе, что в отдельных случаях является преимуществом механизма, а в отдельных случаях недостатком и в целом определяет область его использования. Существует два основных типа кулисных механизмов различающихся по тому, какое движение совершает кулиса, это механизмы с качательным и вращательным движением кулисы
Рис. 16. Типы кулисных механизмов
На Рис. 16а показан механизм с качательным движением кулисы
состоящий из кривошипа 1, на оси 2 которого размещается кулисный камень 3, имеющий возможность поступательного перемещения в пазу кулисы 4, шарнирно установленной на неподвижной стойке посредством оси 5 и совершающей качательное движение при вращении кривошипа 1. При этом кулиса 4 совершает прямой ход при повороте кривошипа 1 на угол а
, а обратный ход при повороте кривошипа на угол В
, что приводит к различию скоростей прямого и обратного хода по причине неравенства этих углов. На Рис. 16б показан механизм с вращательным движением кулисы
состоящий из кривошипа 1, на оси 2 которого размещается кулисный камень 3 и кулисы 4, шарнирно установленной на неподвижной стойке посредством оси 5 и совершающей при вращении кривошипа 1 вращательное движе-ние. При такой схеме кулисного механизма различие скорости прямого и обратного хода кулисы также определяется разницей углов а
и В
.
По сравнению с механизмом шарнирного четырехзвенника используемого для таких же целей (см. Рис. 3), кулисный механизм позволяет проще обеспечить компоновку ведущего кривошипа и ведомой кулисы разместив их симметрично относительно общей оси, что бывает необходимо при проектировании. Но, при этом кулисный механизм имеет увеличенные потери за счет дополнительного трения скольжения в кулисной паре и поэтому находит применение в основном в мало нагруженных, вспомогательных механизмах технологического оборудования.
В данном разделе полной версии статьи содержится 6 примеров
конструктивного исполнения кулисных
механизмов (см. Рис. в таб.) с описанием их работы
Рычажные механизмы с дополнительными
конструктивными элементами
При использовании рычажных механизмов в составе технологического оборудования и оснастки для обеспечения эффективной работы в него встраиваются дополнительные конструктивные элементы, которые позволяют решать следующие задачи:
− регулировать величину хода выходного звена (ползуна, рычага, кулисы),
− регулировать исходное (конечное) положение выходного звена,
− предохранять детали механизма от поломки,
− сообщать выходному звену сложное движение
− включать и выключать работу механизма,
Рассмотрим примеры конструктивного выполнения таких рычажных механизмов. Регулирование величины хода выходного звена рычажного механизма осуществляется двумя способами, изменением соотношения плеч рычага, или изменением величины эксцентриситета ведущего кривошипа.
Рис 26 Конструкция устройства, позволяющего регулировать длину его ведущего плеча.
На Рис 26 показана конструкция устройства, встроенного в рычаг малонагруженного рычажного механизма, позволяющего регулировать длину его ведущего плеча. В этот рычаг, состоящий из ведущего 1 и ведомого 2 плеч и установленный на оси 3, встроен палец 6, шарнирно, посредствам оси 5 соединенный с ведущей тягой 4 и фиксируемый в требуемом положении в пазу 10, а в его резьбовое отверстие пропущен регулировочный винт 7. При этом, ведомое плечо 2 рычага шарнирно посредствам оси 8 соединено с ведомым звеном рычажного механизма. При выполнении регулировки длины ведущего плеча 1 рычага производится раскручивание гайки 9, затем перемещение в ту или другую сторону пальца 6 по пазу ведущего плеча 1 рычага регулировочным винтом 7 и после этого выполняется последующее стопорение пальца 6 гайкой 9.
Рис 27 Конструкция кривошипно – шатунного механизма с устройством для регулировки величины хода его выходного звена
На Рис 27 показана конструкция кривошипно – шатунного механизма со встроенным устройством для регулировки величины хода его выходного звена, которое выполнено в виде промежуточного двуплечего рычага с регулируемой длиной ведущего плеча, Он содержит ведущий кривошипный вал 1, на мотылевой шейке которого установлен шатун 2, шарнирно соединенный посредствам оси 3 с промежуточным двуплечим рычагом 5, установленным на станине посредствам оси 6, а с помощью оси 7 соединенным с ведомой тягой 8. При этом на промежуточном рычаге 5 посредствам оси 9 шарнирно установлен ходовой винт 10, на котором расположена гайка (гайка на Рис 34 не показан) шарнирно соединенная с осью 3 шатуна 2 и имеет возможность, как ползушка, перемещаться в радиусном пазу 4 промежуточного рычага 5. При вращении ходового винта 10 шатун 2 поворачивается на угол αi что приводит к изменению величины ведущего плеча промежуточного рычага 5, а изменяющееся при этом, соотношение длин его ведомого и ведущего плеч позволяет менять величину хода ведомой тяги 8 механизма. Рассмотренное устройство для регулировки хода выходного звена механизма выгодно отличается от рассмотренного ранее тем, что оно позволяет при выполнении регулировки сохранять исходное положение выходного звена (тяги 8), что обеспечивается наличием в промежуточном рычаге 5 радиусного паза 4, центр которого совпадает с осью кривошипного вала 1, поэтому при выполнении регулировки поворот шатуна 2 не меняет положение промежуточного рычага 5.
В данном разделе полной версии статьи содержится 12 примеров
конструктивного исполнения рычажных механизмов
с дополнительными конструктивными элементами
(см. Рис. в таб.) с описание их работ
ы
Зубчато – рычажные механизмы.
Комбинация рычажных механизмов с зубчатыми передачами позволяет создать механизмы с новыми нехарактерными для обоих свойствами. Чаще всего такие механизмы используются для получения выстоя выходного звена, но в ряде случаев они могут позволять получать различные траектории движения выходного звена, а также изменять величину и скорость его перемещения
Рис 36 Конструкция зубчато – рычажного механизма позволяющая получить удвоенное число возвратно-поступательного перемещения ведомого звена по отношению к ведущему.
На Рис 36 показана конструкция зубчато – рычажного механизма позволяющая получить удвоенное число возвратно-поступательного перемещения ведомого звена по отношению к ведущему. Ведущим элементом этого привода является тяга 1, которая сообщает качательное движение рычагу 2, связанному с зубчатым колесом 3 и свободно поворачивающимся с этим колесом на оси 4. Зубчатое колесо 3 сообщает вращение колесу 5, связанному с рычагом 7, установленным на оси 6. Палец 10 рычага 7, перемещаясь в пазу кулисы 9, сообщает движение тяге 8. Оси 4 и 6 смонтированы в неподвижном корпусе 11, установленном на станине. На Рис 36б,в тяга 1 показана в крайних правом и левом положениях, что соответствует началу и середине цикла ее движения. Кулиса 9 в обоих случаях занимает одно и то же положение, поскольку она совершает полный цикл и возвращается в исходное положение. Рычаг 2 перемещается тягой 1 из положения, показанного на Рис 36а влево, вследствие чего, зубчатое колесо 3 совершает определенную часть оборота. Зубчатое колесо 5, находящееся в зацеплении с колесом 3, совершает такой же поворот в противоположном направлении. Рычаг 7, соединенный с колесом 5 поворачивается вместе с ним, а палец 10 перемещается вниз по пазу кулисы 9. До пересечения пальцем 10 центра оси 6, кулиса поворачивается вправо и доходит до крайнего положения (см. Рис 36в). При дальнейшем движении тяги 1 палец 10 опускается ниже центра оси 6 и перемещает кулису 9 в обратном направлении, т. е. влево. В момент достижения тягой 1 крайнего левого положения кулиса 9 также занимает свое крайнее левое положение, делая двойной ход за время совершения тягой 1 только хода вперед. За время совершения тягой 1 обратного хода кулиса 9 совершает еще один двойной ход.
В данном разделе полной версии статьи содержится 4 примера
конструктивного исполнения зубчато – рычажных
механизмов (см. Рис. в таб.)
Полная версия статьи, включает 24 страниц текста и 41 чертеж.
ЛИТЕРАТУРА.
1. Игнатьев Н. П. Основы проектирования Азов 2011г.
2. Игнатьев Н. П. Проектирование механизмов Азов 2015г.
Статья написана на основании информации из соответствующих разделов работы автора «Основы проектирования» изданной в 2011г и работы автора «Проектирование механизмов» , изданной в 2015г.
Для приобретения полной версии статьи добавьте её в корзину,
Стоимость полной версии статьи 200 рублей.
ФЕДЕРАЛЬНОЕ АГЕНТСТВО ПО ОБРАЗОВАНИЮ РФ
ГОСУДАРСТВЕННОЕ ОБРАЗОВАТЕЛЬНОЕ УЧРЕЖДЕНИЕ ВЫСШЕГО ПРОФЕССИОНАЛЬНОГО ОБРАЗОВАНИЯ
«ТЮМЕНСКИЙ ГОСУДАРСТВЕННЫЙ НЕФТЕГАЗОВЫЙ УНИВЕРСИТЕТ»
ИНСТИТУТ ТРАНСПОРТА
Кафедра Детали машин
ОБЗОР ОСНОВНЫХ ВИДОВ МЕХАНИЗМОВ
МЕТОДИЧЕСКИЕ УКАЗАНИЯ
к практическим занятиям по Теории механизмов и машин для студентов специальностей НР-130503, ПСТ-130501, НБ-130504, МОП-130602, АТХ-190601, СТЭ-190603, ПДМ-190205, СП-150202, ПТИ-260703, ТМ-151001, МКC-151002, МХП-240801, МСО-190207
очной и заочной полной и сокращенной форм обучения
Тюмень 2007
Утверждено редакционно-издательским советом
Тюменского государственного нефтегазового университета
Составители: доцент, к.т.н. Забанов Михаил Петрович
профессор, д.т.н. Бабичев Дмитрий Тихонович
ассистент, Панков Дмитрий Николаевич
© государственное образовательное учреждение высшего профессионального образования
«Тюменский государственный нефтегазовый университет»
В процессе занятия необходимо ознакомиться с основными группами и видами механизмов, их графическими изображениями. Научиться представлять реальный механизм в виде схемы.
В отчете необходимо изобразить и описать классические виды механизмов.
Ведущей отраслью современной техники является машиностроение. Прогресс машиностроения определяется созданием новых высокопроизводительных и надежных машин. Решение этой важнейшей проблемы основывается на комплексном использовании результатов многих научных дисциплин и, в первую очередь, теории механизмов и машин.
По мере развития машин содержание термина "машина" изменялось. Для современных машин дадим следующее определение: машина есть устройство, создаваемое человеком для преобразования энергии, материалов и информации с целью облегчения физического и умственного труда, увеличения его производительности и частичной или полной замены человека в его трудовых и физиологических функциях.
По выполняемым машинами функциям их делят на следующие классы:
1) Энергетические машины
2) Транспортные машины
3) Технологические машины
4) Контрольно-управляющие машины
5) Логические машины
6) Кибернетические машины
Определение термина "механизм" неоднократно менялось по мере того, как появлялись новые механизмы.
Механизм есть система тел, предназначенная для преобразования движения одного или нескольких твердых тел в требуемые движения других тел. Если в преобразовании движения кроме твердых тел участвуют жидкие или газообразные тела, то механизм называется соответственно гидравлическим или пневматическим. С точки зрения функционального назначения механизмы делятся на следующие виды:
1) Механизмы двигателей и преобразователей
2) Передаточные механизмы
3) Исполнительные механизмы
4) Механизмы управления, контроля и регулирования
5) Механизмы подачи, транспортировки и сортировки обрабатываемых изделий и объектов
6) Механизмы автоматического счета, взвешивания и упаковки готовой продукции
Основным признаком механизма является преобразование механического движения. Механизм входит в состав многих машин, т. к. для преобразования энергии, материалов и информации требуется обычно преобразование движения получаемого от двигателя. Нельзя отождествлять понятия "машина" и "механизм". Во-первых, кроме механизмов в машине всегда имеются дополнительные устройства, связанные с управлением механизмами. Во-вторых, есть машины, в которых нет механизмов. Например, в последние годы созданы технологические машины, в которых каждый исполнительный орган приводится в движение от индивидуального электро- или гидродвигателя.
При описании механизмов, они были разделены на отдельные группы по признаку их конструктивного оформления (рычажные, кулачковые, фрикционные, зубчатые и др.)
Механизмы образуются последовательным присоединениям звеньев к начальному механизму.
ЗВЕНО – одна или несколько неподвижно соединенных друг с другом деталей, входящих в механизм и движущихся, как одно целое .
ВХОДНОЕ ЗВЕНО – звено, которому сообщается движение, преобразуемое механизмом в требуемые движения других звеньев. Входное звено соединено с двигателем либо с выходным звеном другого механизма.
ВЫХОДНОЕ ЗВЕНО – звено, совершающее движение, для выполнения которого предназначен механизм. Выходное звено соединено с исполнительным устройством (рабочим органом, указателем прибора), либо со входным звеном другого механизма.
Звенья соединяются друг с другом подвижно посредством кинематических пар: вращательных (шарнир) и поступательных (ползун).
ТРАЕКТОРИЯ движения точки (звена) – линия перемещения точки в плоскости. Это может быть прямая линия или кривая.
РЫЧАЖНЫЕ МЕХАНИЗМЫ
Рычажными механизмами называют механизмы, в которые входят жесткие звенья, соединенные между собой вращательными и поступательными кинематическими парами. Простейшим рычажным механизмом является двухзвенный механизм , состоящий из неподвижного звена-стойки 2 (Рис.1.1 ) и подвижного рычага 1 , имеющего возможность вращаться вокруг неподвижной оси (обычно это начальный механизм).
Рис.1.1 Двухзвенный рычажный механизм
К двухзвенным рычажным механизмам относятся механизмы многих ротационных машин: электромоторов, лопастных турбин и вентиляторов. Механизмы всех этих машин состоят из стойки и вращающегося в неподвижных подшипниках звена (ротора).
Более сложными рычажными механизмами являются механизмы, состоящие из четырех звеньев, так называемые четырехзвенные механизмы .
На Рис.1.2 показан механизм шарнирного четырехзвенника, состоящего из трех подвижных звеньев 1, 2, 3 и одного неподвижного звена 4. Звено 1 , соединенное со стойкой, может совершать полный оборот и носит название кривошипа. Такой шарнирный четырехзвенник, имеющий в своем составе один кривошип и одно коромысло называется кривошипно-коромысловым механизмом , где вращательное движение кривошипа посредством шатуна преобразуется в качательное движение коромысла. Если кривошип и шатун вытянуты в одну линию, то коромысло займет крайнее правое положение, а при наложении друг на друга – левое.
Рис. 1.2 Механизм шарнирного четырехзвенника
Примером такого механизма является механизм представленный на Рис.1.3 , где звено 1 – кривошип (входное звено), звено 2 – шатун, звено 3 – коромысло. Точка M S двигаясь по кривой описывает траекторию . Одни траектории могут быть воспроизведены рычажными механизмами теоретически точно, другие – приближенно, с достаточной для практики степенью точности.
Рассматриваемый механизм, называемый симметричным механизмом Чебышева, часто применяют в качестве кругового направляющего механизма, у которого АВ = ВС = ВМ = 1. При указанных соотношениях
Рис. 1.3 Кривошипно-коромысловый механизм
точка М шатуна АВ описывает траекторию, симметричную относительно оси n - п . Угол наклона оси симметрии к линии центров СО определяется: ÐМСО = π – Ω / 2. Часть траектории точки М является дугой окружности радиуса О 1 М, что может быть использовано в механизмах с остановкой выходного звена.
Другим примером четырехзвенника является широко распространенный в технике кривошипно-ползунный механизм (Рис. 1.4 ).
Рис. 1.4 Кривошипно-ползунный механизм
В этом механизме вместо коромысла устанавливается ползун, движущийся в неподвижной направляющей. Этот кривошипно-шатунный механизм применяют в поршневых двигателях, насосах, компрессорах и т.д. Если эксцентриситет е равен нулю, то получим центральный кривошипно-ползунный механизм или аксиальный. При е не равном нулю кривошипно-ползунный механизм называется нецентральным или дезаксиальным. Здесь вращение кривошипа ОА через шатун АВ преобразуется в возвратно-поступательное движение ползуна. Естественно крайние положения ползуна, будут при расположении кривошипа и шатуна в одну линию.
Если в рассмотренном механизме заменить неподвижную направляющую на подвижную, которая называется кулисой, то получим четырехзвенный кулисный механизм с кулисным камнем. Примером такого механизма может служить кулисный механизм строгального станка (Рис.1.5 ). Кривошип 1 , вращаясь вокруг оси, через кулисный камень 2 заставляет кулису 3 совершать качательное движение. При этом кулисный камень относительно кулисы движется возвратно-поступательно.
Рис. 1.5 Четырехзвенный кулисный механизм
Крайние положения кулисы будут при перпендикулярном расположении к ней кривошипа. Построить такие положения просто: изображается окружность радиусом равным длине кривошипа (траектория движения точки А ), и проводятся касательные из оси вращения кулисы.
Таким образом звенья могут совершать поступательное , вращательное или сложное движения.
В серийном и мелкосерийном производстве проектируют оснастку с использованием универсальных зажимных механизмов (ЗМ) или специальных однозвенных с ручным приводом. В тех случаях, когда требуются большие силы закрепления заготовок, целесообразно применять механизированные зажимы.
В механизированном производстве используют зажимные механизмы, у которых прихваты автоматически отводятся в сторону. Этим обеспечивается свободный доступ к установочным элементам для очистки их от стружки и удобство переустановки заготовок.
Рычажные однозвенные механизмы с управлением от гидро- или пневмопривода используют при закреплении, как правило, одной корпусной или крупной заготовки. В таких случаях прихват отодвигают или поворачивают вручную. Однако лучше использовать дополнительное звено для отвода прихвата из зоны загрузки заготовки.
Зажимные устройства Г-образного типа применяют чаще для закрепления корпусных заготовок сверху. Для поворота прихвата во время закрепления предусматривают винтовой паз с прямолинейным участком.
Рис. 3.1.
Комбинированные зажимные механизмы используют для закрепления широкой номенклатуры заготовок: корпусов, фланцев, колец, валов, планок и пр.
Рассмотрим некоторые типовые конструкции зажимных механизмов.
Рычажные зажимные механизмы отличаются простотой конструкции (рис. 3.1), значительным выигрышем в силе (или в перемещении), постоянством силы зажима, возможностью закрепления заготовки в труднодоступном месте, удобством эксплуатации, надежностью.
Рычажные механизмы используют в виде прихватов (прижимных планок) или в качестве усилителей силовых приводов. Для облегчения установки заготовок рычажные механизмы выполняют поворотными, откидными и передвижными. По конструкции (рис. 3.2) они могут быть прямолинейными отодвигаемыми (рис. 3.2, а)
и поворотными (рис. 3.2, б),
откидными (рис. 3.2, в)
с качающейся опорой, изогнутыми (рис. 3.2, г)
и комбинированными (рис. 3.2,
Рис. 3.2.
На рис. 3.3 приведены универсальные рычажные ЗМ с ручным винтовым приводом, используемые в индивидуальном и мелкосерийном производствах. Они просты по конструкции и надежны.
Опорный винт 1 устанавливают в Т-образный паз стола и крепят гайкой 5. Положение зажимного прихвата 3 по высоте регулируют винтом 7 с опорной пятой 6, и пружиной 4. Сила закрепления на заготовку передается от гайки 2 через прихват 3 (рис. 3.3, а).
В ЗМ (рис. 3.3, б) заготовку 5 крепят прихватом 4, а заготовку 6 прихватом 7. Сила закрепления передается от винта 9 на прихват 4 через плунжер 2 и регулировочный винт /; на прихват 7 - через закрепленную в нем гайку. При изменении толщины заготовок положение осей 3, 8 легко регулируется.

Рис. 3.3.
В ЗМ (рис. 3.3, в) корпус 4 зажимного механизма крепят к столу гайкой 3 посредством втулки 5 с резьбовым отверстием. Положение изогнутого прихвата 1 но высоте регулируют опорой 6 и винтом 7. Прихват 1 имеет люфт между конической шайбой, установленной иод головкой винта 7, и шайбой, которая находится выше стопорного кольца 2.
В конструкции дугообразный прихват 1 во время крепления заготовки гайкой 3 поворачивается на оси 2. Винт 4 в данной конструкции не крепится к столу станка, а свободно передвигается в Т-образном пазу (рис. 3.3, г).
Используемые в зажимных механизмах винты развивают на торце силу Р, которая может быть рассчитана по формуле

где Р - усилие рабочего, приложенное к концу рукоятки; L - длина рукоятки; г ср - средний радиус резьбы; а - угол подъема резьбы; ср - угол трения в резьбе.
Момент, развиваемый на рукоятке (ключе), для получения заданной силы Р
где М, р - момент трения на опорном торце гайки или винта:

где /- коэффициент трения скольжения: при закреплении / = 0,16...0,21, при раскреплении / = 0,24...0,30; D H - наружный диаметр трущейся поверхности винта или гайки; с/ в - диаметр резьбы винта.
Приняв a = 2°30" (для резьбы от М8 до М42 угол а меняется от 3°10" до 1°57"), ф = 10°30", г ср = 0,45с/, Д, = 1,7с/, d B = d и/= 0,15, получим приближенную формулу для момента на торце гайки М гр = 0,2dP.
Для винтов с плоским торцом М т р = 0,1с1Р+ н, а для винтов со сферическим торцом М Л р ~ 0,1 с1Р.
На рис. 3.4 приведены другие рычажные зажимные механизмы. Корпус 3 универсального зажимного механизма с винтовым приводом (рис. 3.4, а) крепят к столу станка винтом / и гайкой 4. Прихват б во время крепления заготовки поворачивают на оси 7 винтом 5 по часовой стрелке. Положение прихвата б с корпусом 3 легко регулируется относительно неподвижного вкладыша 2.

Рис. 3.4.
Специальный рычажный зажимной механизм с дополнительным звеном и пневмоприводом (рис. 3.4, б) используют в механизированном производстве для автоматического отвода прихвата из зоны загрузки заготовок. Во время раскрепления заготовки / шток б перемещается вниз, при этом прихват 2 поворачивается на оси 4. Последняя совместно с серьгой 5 поворачивается на оси 3 и занимает положение, показанное штриховой линией. Прихват 2 отводится из зоны загрузки заготовок.
Клиновые зажимные механизмы бывают с односкосым клином и клиноплунжерные с одним плунжером (без роликов или с роликами). Клиновые зажимные механизмы отличаются простотой конструкции, удобством наладки и эксплуатации, способностью к самоторможению, постоянством силы зажима.
Для надежного закрепления заготовки 2 в приспособлении 1 (рис. 3.5, а) клин 4 должен быть самотормозяшимся за счет угла а скоса. Клиновые зажимы применяют самостоятельно или в качестве промежуточного звена в сложных зажимных системах. Они позволяют увеличивать и изменять направление передаваемой силы Q.
На рис. 3.5, б показан стандартизованный клиновой зажимной механизм с ручным приводом для закрепления заготовки на столе станка. Зажим заготовки осуществляется клином /, перемещающимся относительно корпуса 4. Положение подвижной части клинового зажима фиксируется болтом 2 , гайкой 3 и шайбой; неподвижной части - болтом б, гайкой 5 и шайбой 7.

Рис. 3.5. Схема (а) и конструкция (в) клинового зажимного механизма
Усилие зажима, развиваемое клиновым механизмом, рассчитывают но формуле

где ср и ф| - углы трения соответственно на наклонной и горизонтальной поверхностях клина.

Рис. 3.6.
В практике машиностроительного производства чаще используют оснастку с наличием роликов в клиновых зажимных механизмах. Такие зажимные механизмы позволяют уменьшить вдвое потери на трение.
Расчет силы закрепления (рис. 3.6) производится по формуле, аналогичной формуле для расчета клинового механизма, работающего при условии трения скольжения на контактирующих поверхностях. При этом углы трения скольжения ф и ф, заменяем на углы трения качения ф |1р и ф пр1:

Чтобы определить соотношение коэффициентов трения при скольжении и
качении, рассмотрим равновесие нижнего ролика механизма: F l - = T - .
Так как Т = Wf
F i =Wtgi
р цр1 и / = tgcp, получим tg(p llpl = tg верхнего ролика вывод формулы аналогичен. В конструкциях клиновых зажимных механизмов используют стандартные ролики и оси, у которых D
= 22...26 мм, a d
= 10... 12 мм. Если принять tg(p =0,1; d/D
= 0,5, тогда коэффициент трения качения будет / к = tg 0,1 0,5 = 0,05 =0,05. Рис. 3.
На рис. 3.7 приведены схемы клиноплунжерных зажимных механизмов с двухонорным плунжером без ролика (рис. 3.7, а); с двухопорным плунжером и роликом (рис. 3.7, (5); с одноопорным плунжером и тремя роликами (рис. 3.7, в); с двумя одноопорными (консольными) плунжерами и роликами (рис. 3.7, г).
Такие зажимные механизмы надежны в работе, просты в изготовлении и могут обладать свойством самоторможения при определенных углах скоса клина. На рис. 3.8 показан зажимной механизм, применяемый в автоматизированном производстве. Заготовку 5 устанавливают на палец б
и крепят прихватом 3.
Сила закрепления на заготовку передается от штока 8
гидроцилиндра 7 через клин 9,
ролик 10
и плунжер 4.
Отвод прихвата из зоны загрузки во время съема и установки заготовки осуществляет рычаг 1,
который поворачивает на оси 11
выступ 12.
Прихват 3
легко перемешается от рычага 1
или пружины 2, так как в конструкции оси 13
предусмотрены прямоугольные сухари 14,
легко перемещаемые в пазах прихвата. Рис. 3.8.
Для увеличения силы на штоке пневмопривода или другого силового привода применяют шарнирно-рычажные механизмы. Они являются промежуточным звеном, связывающим силовой привод с прихватом, и применяются в том случае, когда для крепления заготовки требуется большая сила. По конструкции их делят на однорычажные, двухрычажные одностороннего действия и двухрычажные двустороннего действия. На рис. 3.9, а
показана схема шарнирно-рычажного механизма (усилителя) одностороннего действия в виде наклонного рычага 5
и ролика 3,
соединенного осью 4
с рычагом 5 и штоком 2 пневмоцилиндра 1.
Исходная сила Р,
развиваемая пневмоцилиндром, через шток 2, ролик 3 и ось 4
передается на рычаг 5.
При этом нижний конец рычага 5
перемещается вправо, а его верхний конец поворачивает прихват 7 вокруг неподвижной опоры б
и закрепляет заготовку силой Q.
Значение последней зависит от силы W
и соотношения плеч прихвата 7. Силу W
для однорычажного шарнирного механизма (усилителя) без плунжера определяют по уравнению Сила IV
, развиваемая двухрычажным шарнирным механизмом (усилителем) (рис. 3.9, б),
равна Силу If"
2
,
развиваемую двухрычажным шарнирно-плунжерным механизмом одностороннего действия (рис. 3.9, в),
определяют по уравнению В приведенных формулах: Р-
исходная сила на штоке механизированного привода, Н; a - угол положения наклонного звена (рычага); р - дополнительный угол, которым учитываются потери на трение в шарнирах ^p = arcsin/^П;/- коэффициент трения скольжения на оси ролика и в шарнирах рычагов (f ~
0,1...0,2); (/-диаметр осей шарниров и ролика, мм; D
- наружный диаметр опорного ролика, мм; L -
расстояние между осями рычага, мм; ф[ - угол трения скольжения на осях шарниров; ф 11р - угол трения качения на опоре ролика; tgф пp =tgф-^; tgф пp 2 - приведенный коэффициент жере; tgф np 2 =tgф-; / - расстояние между осью шарнира и серединой на- трения, учитывающий потери на трение в консольном (перекошенном) плун- 3/ , правляющей втулки плунжера (рис. 3.9, в),
мм; а
- длина направляющей втулки плунжера, мм. Рис. 3.9.
действия Однорычажные шарнирные зажимные механизмы применяют в тех случаях, когда требуются большие силы закрепления заготовки. Это объясняется тем, что во время крепления заготовки угол а наклонного рычага уменьшается и сила зажима увеличивается. Так, при угле а = 10° сила W
на верхнем конце наклонного звена 3
(см. рис. 3.9, а)
составляет JV ~
3,5Р,
а при а = 3° W~
1 IP,
где Р
- сила на штоке 8
пневмоцилиндра. На рис. 3.10, а
приведен пример конструктивного исполнения такого механизма. Заготовку / крепят прихватом 2.
Сила закрепления на прихват передается от штока 8
пневмоцилиндра через ролик 6
и регулируемое по длине наклонное звено 4,
состоящее из вилки 5
и серьги 3.
Для предотвращения изгиба штока 8
для ролика предусмотрена опорная планка 7. В зажимном механизме (рис. 3.10, б)
пневмоцилиндр расположен внутри корпуса 1
приспособления, к которому винтами прикреплен корпус 2
зажимного Рис. 3.10.
механизма. Во время закрепления заготовки шток 3
пневмоцилиндра с роликом 7 перемещаются вверх, а прихват 5
со звеном б
поворачивается на оси 4.
При раскреплении заготовки прихват 5 занимает положение, показанное штриховыми линиями, не мешая смене заготовки.
Основные виды рычажных механизмов.
1. Кривошипно-ползунный механизм.
а) центральный (рис.1);
б) внеосный (дезоксиальный) (рис.2);
е - эксцентриситет
Рис. 2
1-кривошип, т.к. звено совершает полный оборот вокруг своей оси;
2-шатун, не связан со стойкой, совершает плоское движение;
3-ползун (поршень), совершает поступательное движение;
1 - кривошип;
2 - камень кулисы (втулка) вместе с зв.1 совершает полный оборот вокруг А (w1 и w2 одно и тоже), а также движется вдоль зв.3, приводя его во вращение;
3 - коромысло (кулиса).
В процессе проектирования конструктор решает две задачи:
· анализа (исследует готовый механизм);
· синтеза (проектируется новый механизм по требуемым параметрам);
Лекция 2.
Глава 1. Анализ рычажных механизмов .
В данной главе будут рассмотрены вопросы:
1. структурный анализ механизма (изучение строения механизма);
2. изучение классов и видов кинематических пар.
3. определение числа степеней свободы механизма и определение наличия или отсутствия избыточных связей; в случае наличия - дать рекомендации по способу их устранения;
4. кинематический анализ механизма.
Примечание :
Кинематическая пара существует, если не происходит деформации звеньев, образующих эту пару, и не должно происходить отрыва звеньев одно от другого, образующих кинематическую пару.
Примечание:
Ограничения, накладываемые на независимые движения звеньев, образующих кинематическую пару, называются - условия связи S.
Число степеней свободы механизма
где Н - подвижность .
Любое незакрепленное тело в пространстве имеет 6 степеней свободы, на плоскости - 3.
Классификация кинематических пар проводят либо числу связей, либо по числу подвижностей:
Число связей Класс КП Число подвижностей
S=1 P I H=5
S=2 P II H=4
S=3 P III H=3
S=4 P IV H=2
S=5 P V H=1
Существует 5 классов кинематических пар.
Примеры различных КП смотри рис. 4-95.
Кинематические пары по характеру контакта звеньев, образующих КП, разделяют на:
1. низшие:
· вращательные;
· поступательные;
2. высшие.
Контакт звеньев в низшей КП осуществляется по поверхности. Контакт звеньев в высшей КП - либо по линии, либо в точке.
§1.2 Определение числа степеней свободы рычажных механизмов.
1.2.1 Плоские механизмы.
В плоском механизме все звенья движутся в одной плоскости, все оси параллельны друг другу и перпендикулярны плоскости механизма.
ФОРМУЛА ЧЕБЫШЕВА : W пп =3n -2p н -p в ,
Где n - число подвижных звеньев механизма, р н - число низших КП, р в - число высших КП.
Рис.1.2.1
1.2.2 Пространственные механизмы.
В пространственном механизме оси непараллельны, звенья могут двигаться в разных плоскостях.
W пр = 6n - (S 1 + S 2 + S 3 + S 4 + S 5)
Допустим, что механизм, изображенный на рис.1.2.1 - пространственный и все кинематические пары 5-го класса, т.е. одноподвижны A V ,B V ,C V ,D V , тогда
W пр = 6n - (5p V +4p IV +3p III +2p II+ p I)
W пр = 6 . 3 - 5 . 4 = -2 à статически неопределимая ферма.
Для получения W действ =0, необходимо добавить 3 движения.
q= W действ - W пр = 1 - (-2) = 3,
где q - избыточные связи .
Для того чтобы их устранить, надо изменить класс некоторых кинематических пар, при этом нельзя изменять класс КП А. Поэтому, сделаем КП В - сферическим шарниром, т.е. 3-го класса (добавим 2 подвижности), а КП С - 4-го класса (добавим 1 подвижность). Тогда
W пр = 6 . 3 - (5 . 2 + 4 . 1 + 3 . 1) = 18 - 17 = 1
ФОРМУЛА СОМОВА-МАЛЫШЕВА: W пр = 6 . n - ΣS i + q
§1.3 Кинематический анализ рычажных механизмов.
1.3.1 Основные понятия и определения.
Зависимость линейных координат в какой-либо точке механизма от обобщенной координаты - линейная функция положения данной точки в проекциях на соответствующие оси координат .
Зависимость угловой координаты какого-либо звена механизма от обобщенной координаты - угловая функция положения данного звена.
Первая производная линейной функции положения точки по обобщенной координате - линейная передаточная функция данной точки в проекциях на соответствующие оси координат (иногда называют «аналог линейной скорости…»)
полная скорость т. С будет
Первая производная угловой функции положения звена по обобщенной координате - передаточное отношение .
Вторая производная линейной функции положения по обобщенной координате - аналог линейного ускорения точки в проекциях на соответствующие оси .
Вторая производная угловой функции положения звена по обобщенной координате - аналог углового ускорения звена .
1.3.2 Аналитический способ определения кинематических параметров рычажных механизмов.
Дано: w 1 , l AB , l BS 2 , l BC , l AC
Определить: v i , a i , w 2 , e 2 .
Для исследования плоских рычажных механизмов для решения данной задачи целесообразно использовать метод проецирования векторного контура на оси координат.
Для определения функции положения точки С представим длины звеньев в виде векторов.
Условие замкнутости данного контура:
(3)
рис.1.3.2 из (3) следует, что
(4)
Лекция 3.
Продифференцируем (3) по обобщенной координате:
(5)
Продифференцируем (2) по обобщенной координате:
Если необходимо определить функции положения центра масс, то вы делим векторный контур ABS 2
Условие замкнутости данного векторного контура имеет вид:
(6)
(7)
Продифференцируем (7) по обобщенной координате и получим аналоги линейных скоростей точек S 2 в проекциях на оси х и у:
(9)
Глава 2. Анализ машинного агрегата.
В данной главе будут рассмотрены следующие вопросы:
1. Силы и моменты, действующие в машинном агрегате.
2. Переход от расчетных схем машинных агрегатов к динамическим моделям.
3. Расчет усилий в кинематических парах основного механизма рабочей машины.
4. Определение законов движения главного вала (входного звена) рабочей машины под действием приложенных сил и моментов при различных режимах работы машинного агрегата.
§2.1 Силы и моменты, действующие в машинном агрегате.
2.1.1 Движущиеся силы и моменты F д и М д .
Работа движущих сил и моментов за цикл положительна: А д >0.
Цикл - промежуток времени, по истечению которого все кинематические параметры принимают первоначальное значение, а технологический процесс, происходящий в рабочей машине, начинает повторяться вновь.
2.1.2 Силы и моменты сопротивления (F с, M с).
Работа сил и моментов сопротивления за цикл отрицательна: А c <0.
2.1.3 Силы тяжести (G i).
Работа силы тяжести за цикл равна нулю: А Gi =0.
2.1.4 Расчетные силы и моменты (Ф Si, M Фi).
Ф Si, M Фi - Главные векторы сил инерции и главные моменты от сил инерции.
2.1.5 Реакции в кинематических парах (Q ij).
§2.2 Понятие о механических характеристиках.
Механическая характеристика 3-х фазного асинхронного двигателя.
Индикаторная диаграмма ДВС
H - ход поршня в поршневой машине
(расстояние между крайними
положениями поршня)
Индикаторная диаграмма насоса
Как правило, из паспорта известен диаметр поршня, по нему можно определить площадь S п = p . d 2 /4, тогда сила: F=p . S п
Правило знаков сил и моментов :
· Сила считается положительной, если она по направлению совпадает с направлением движения того звена, к которому эта сила приложена.
· Момент считается положительным, если его направление совпадает с направлением угловой скорости вращения данного звена.
Имея механическую характеристику поршневой машины и учитывая правило знаков, то можно перестроить в график сил (см. лабораторную работу №4).
Основной вывод:
В течение всего цикла работы поршневой машины сила, приложенная к поршню, будет изменяться как по величине, так и по направлению, это в свою очередь приводит к колебаниям угловой скорости главного вала рабочей машины.
§2.3 Понятие о расчетной схеме машинного агрегата и переход от нее к динамической модели.
На расчетной схеме машинного агрегата отмечают основные силовые факторы, действующие в машинном агрегате; основные массы звеньев, влияющих на закон движения машинного агрегата; и основные жесткости валов. На рис.5-92 показан переход от реальной схемы к расчетной схеме (а) и от нее к динамической модели.