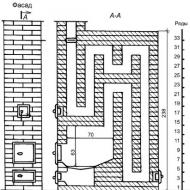
Jak prawidłowo zamontować złączkę rury. Zastosowanie złączek zaciskowych. Rodzaje osprzętu
Dodaj do zakładek
Prawidłowe połączenie rur z polietylenu: rodzaje połączeń i metody instalacji
Obecnie rury PE są szczególnie popularne na rynku materiałów budowlanych. Są one wykorzystywane do budowy różnych rurociągów technologicznych, narzędzi inżynieryjnych do celów przemysłowych i domowych.
Rury polietylenowe są wykorzystywane do budowy różnych rurociągów technologicznych, narzędzi inżynieryjnych do celów przemysłowych i domowych.
Najczęściej są one wykorzystywane do dostarczania zimnej wody, transportu różnych chemikaliów, a także jako nieprzystosowane kanały dla sieci elektrycznych i telefonicznych. Ważne jest, aby dobrze połączyć rury z polietylenu. Poniżej rozważymy główne rodzaje i kategorie odłączalnych i jednoczęściowych połączeń dla rurociągów PE.
Istnieją dwa rodzaje połączeń rurociągów z polietylenu:
- Połączenie nierozłączne metodą zgrzewania doczołowego lub mufowego. Przeprowadzając to połączenie rur z polietylenu, podgrzewanie końców rurociągów odbywa się z późniejszym dokowaniem pod ciśnieniem w celu utworzenia ciągłego szwu.
- Odłączalne połączenie za pomocą zagniatanych połączeń, złączki zaciskowe (złączka tulei zaciskowej) i kołnierze stalowe. Ten rodzaj dokowania jest prosty, ale jest mniej praktyczny i wymaga dodatkowych kosztów związanych z zakupem okuć.
Spawanie ze sprzęgłami elektrotermicznymi
Aby wykonać ten rodzaj spawania wyrobów walcowanych z polietylenu, konieczne jest posiadanie specjalnych łączników i sprzętu spawalniczego. Łączniki do spawania mają elementy grzejne w swoim korpusie, które następnie kurczą (spają) sprzęgło. Ta metoda jest stosowana do spawania polietylenu walcowanego w ciasnych warunkach (doły, wykopy). Sprzężenie elektryczne jest w stanie wytrzymać ciśnienie 1,6 MPa. Wadą tej metody jest to, że wymaga znacznie więcej kosztów materiału niż tyłek.
Schemat łączenia rur za pomocą sprzęgła elektrotermicznego.
Proces spawania można podzielić na kilka etapów:
- centrowanie rury i sprzęgła na wymaganej osi;
- przygotowanie, czyszczenie i odtłuszczanie zewnętrznych powierzchni rur na styku;
- dysza sprzęgająca i połączenie spawarki;
- unieruchomienie połączenia;
- spawanie z ogrzewaniem, topieniem polietylenu i skurczem złącza;
- wyłączenie i chłodzenie sprzęgła.
Połączenie doczołowe z zastosowaniem ciepła
Ten typ spawania rur PE jest stosowany do średnic powyżej 50-63 mm. Połączenie stykowe wykonuje się w kilku etapach:
- Przed spawaniem osie spawanych rurociągów są wyrównane w maszynie centrującej.
- Po przymocowaniu końcowe części rurociągu są wypoziomowane i oczyszczone z tłuszczów, kurzu i brudu.
- Obróbka końcówek na maszynie tnącej.
- Weryfikacja równoległości z obowiązkowym sprawdzaniem luki międzyplanarowej.
- Ogrzewanie końcowych części rur za pomocą narzędzia termicznego.
- Spawanie, a następnie chłodzenie.
- Usuwanie narzędzi, kontrola zewnętrznej powierzchni spawanego szwu.
Połączenie za pomocą stalowych kołnierzy
W niektórych przypadkach, gdy spawanie nie jest możliwe, montuje się kołnierze. Sprzęgło kołnierzowe odnosi się do odłączalnych typów połączeń i jest najbardziej odpowiednie do łączenia produktów PE z kształtkami rurociągów i stalowymi rurociągami. Połączenia kołnierzowe rur wykonywane są za pomocą tulei wciąganych, które są szczelnie zespawane z końcami rur PE lub za pomocą kołnierzy wykonanych z metalu. Między kołnierzami musi być zapakowany materiał uszczelniający (guma, poliester itp.). Zaletą tej metody instalacji jest to, że w przyszłości możliwe będzie odłączenie kołnierzy i wykonanie czyszczenia systemu. Kołnierze rur wodnych mogą być płaskie i profilowane (z kołnierzem, stopem lub stożkiem).
Połączenie wtykowe za pomocą złączek zaciskowych
Połączenie rur bez spawania możliwe jest za pomocą ściskanych elementów montażowych. Często metoda ta jest stosowana do rur o małej średnicy (do 63 mm) i systemów o dużej liczbie odgałęzień, ponieważ każde spawanie pociąga za sobą wzrost kosztów instalacji. Osiągnięcie szczelności wynika z wewnętrznego uszczelnienia odpornej na zużycie gumy i ciętej metalowej tulei. Do wykonania pracy potrzebny jest zestaw kluczy profilowych i specjalny nóż pod kątem prostym. Tuleja może wytrzymać ciśnienie 2,5 MPa. Montaż łącznika jest łatwy i prosty, najważniejsze jest to, że wymiary łączników dokładnie odpowiadają rozmiarom rur wodociągowych.
Nawożenie rur jest mniej powszechne. Walcowanie jest połączone z dzwonem, a szczelność uzyskuje się poprzez uszczelnienie dzwonu gumowym pierścieniem. Takie mocowanie jest bardziej odpowiednie dla systemów bezciśnieniowych na bazie polietylenu. Na koniec chciałbym zauważyć, że przy wyborze rodzaju połączenia rur PE z armaturą, należy wziąć szczególną odpowiedzialność za dobór narzędzi i sprzętu do instalacji.
Teraz możesz łatwo wybrać odpowiednie metody instalacji konwencjonalnych i profilowych rurociągów z polietylenu bez żadnych problemów.
Ze względu na szeroką popularność różnych rodzajów rur z polietylenu, rośnie zapotrzebowanie na elementy dokujących zwane okuciami. Złączki rurowe HDPE ułatwiają instalację w krótkim czasie. W chwili obecnej przedsiębiorstwa wytwarzają wiele różnych związków. Okucia do rur HDPE wykonane są z różnych rodzajów polietylenu, miedzi lub mosiądzu.
Stosuje się kształtki do rur HDPE:
- Do łączenia rur o tej samej średnicy.
- Do łączenia rur o różnych średnicach.
- Aby uporządkować konsekwencje dostarczone przez schemat rurociągu.
- Do montażu zwojów rur.
- Aby zainstalować wtyczkę na rurze PE.
- Do łączenia rur o różnych kształtach.
Miejsca łączenia rur PE powinny być:
- Niezawodny.
- Trwałe.
- Wodoodporny.
- Odporny na ewentualne skutki działania pierwiastków chemicznych.
Klasyfikacja wyposażenia
Profesjonalni instalatorzy rurociągów rozróżniają złącza rurowe HDPE:
- Sposób montażu: ściskany, spawany, spawany elektrycznie.
- Sztywności: elastyczne i sztywne.
- Złącze: odłączalne i jednoczęściowe.
Istnieje kolejna klasyfikacja elementów łączących:
- Bezpośredni, używany do dokowania rur HDPE o tej samej średnicy.
- Redukcja, stosowana do łączenia rur o różnych średnicach.
Przeanalizujemy bardziej szczegółowo pierwszą klasyfikację okuć.
Okucia do różnych metod łączenia rur
W zależności od wybranej metody instalacji rurociągu rozróżnij:
- złącza spawane;
- elektrycznie spawane elementy łączące;
- złączki zaciskowe.
Spawane elementy łączące
Złączki spawane mogą być produkowane na dwa sposoby:
- metodą niskiego ciśnienia, która występuje pod wysokim ciśnieniem (elementy odlewnicze);
- zgrzewanie doczołowe małych segmentów rurowych (złączek spawanych).
Złącza spawane są dostępne w średnicy od 63 mm do 315 mm.
Tego typu złączki są przeznaczone do łączenia rur ze spawaniem. Niski koszt połączeń spawanych powoduje szeroki zakres ich zastosowania. Praktycznie wszystkie gałęzie i wtyczki dostarczone przez projekt rurociągu mogą być wykonane ze złączami spawanymi.
Najczęściej złączki spawane są stosowane do instalacji gazociągów i instalacji, w których temperatura transportowanej cieczy nie przekracza 40 ° C.
Elektro-spawane elementy łączące
Złączki zgrzewane elektrycznie lub termistorowe służą do mocowania konstrukcji rurociągu w trudno dostępnych miejscach, czyli tam, gdzie nie jest możliwe przeprowadzenie konwencjonalnego zgrzewania doczołowego.
Wyposażony w drut grzewczy umieszczony na częściach łączących. Pod wpływem temperatury spirale rozgrzewają się i topią rurę polietylenową. Po schłodzeniu uzyskuje się silny spaw.
Złącza kompresyjne
Złączki zaciskowe do rur HDPE są przeznaczone do łączenia rur bez stosowania spawania. Za pomocą takich elementów stykowych uzyskuje się odłączalne połączenie.
Okucia tego rodzaju składają się z:
- obudowa z polietylenu;
- o-ringi umieszczone w punktach połączenia;
- pierścienie zaciskowe, chroniące połączenie przed uszkodzeniem mechanicznym;
- tuleja, dociskanie rury;
- nakrętki zabezpieczające, bezpiecznie zamykające miejsce dokowania.
Wyprodukowane z różnych materiałów. Średnica złączy waha się od 16 mm do 110 mm.
Cechy mocowania za pomocą złączek zaciskowych
Aby prawidłowo połączyć rury lub wykonać niezbędne gałęzie z łącznikami zaciskowymi, postępuj zgodnie z następującymi instrukcjami:
- Rura HDPE jest przygotowywana, a złączki zaciskowe są poluzowywane o kilka zwojów.
- Rura jest oznaczona znacznikiem wskazującym głębokość, do której rura powinna zostać włożona do złączki. Przed montażem zaleca się nasmarować obszar łączonej rury wodą lub lekkim roztworem mydła.
- Przed narysowanym znaczkiem rura jest wkładana do przygotowanego łącznika. W celu pełnego wprowadzenia rury PE do pierścienia uszczelniającego, wymagany jest wysiłek. W przeciwnym razie połączenie nie zostanie zapieczętowane.
- Nakrętka nakrętki jest dokręcana aż do końca nici.
Przy prawidłowym montażu złączek zaciskowych uzyskuje się wystarczająco mocne i szczelne połączenie.
Rozdzielanie okuć dla sztywności połączenia
Ze względu na stopień sztywności, okucia wyróżniają się:
- Trudne. Takie połączenia całkowicie wykluczają możliwość przesuwania rur.
- Elastyczny, który pozwala wzdłużne przesunięcie rur do 3 - 5 mm i obrót rur pod małym kątem. Jeśli używasz elastycznego łącznika, wszystkie właściwości niezbędne dla punktu połączenia pozostają niezmienione.
Połączenia elastyczne są najbardziej odpowiednie do układania rurociągów w gruncie, ale są również bardziej kosztowne. Dlatego są używane tylko w przypadkach skrajnej konieczności.
Do instalacji najprostszych systemów rurociągów częściej stosowane są okucia twarde.
Rodzaje osprzętu
Podczas instalacji rurociągu mogą być wymagane zarówno odłączalne połączenia, jak i jednoczęściowe połączenia. Wynika to z obecności rury łączącej i jej zastosowania. Na przykład rury HDPE do dostarczania wody: armatura w pierwszym etapie instalacji służy do podłączenia rurociągu do przepompowni. W pewnym momencie może być konieczna wymiana pompy, a odłączane połączenie uprości niezbędną pracę tak bardzo, jak to możliwe.
Odłączane połączenia
W większości przypadków instalacja odbywa się za pomocą opisanych powyżej złączek zaciskowych. Istnieją jednak inne sposoby aranżowania tego połączenia:
- Połączenie kołnierzowe. Odlew lub mosiężny kołnierz jest mocowany do rury za pomocą spawania. Ten rodzaj połączenia jest stosowany głównie do rur o dużej średnicy lub do łączenia rury polietylenowej z metalową rurą.
- Połączenie gwintowane. Mocowanie rur odbywa się za pomocą wcześniej przygotowanych gwintów na rurach i kształtkach. Jest uważany za najmniej wiarygodny. Może być stosowany do układania przewodów kablowych lub systemów o niskim ciśnieniu płynu.
- Połączenie flare. Jest używany niezwykle rzadko. Dokonuje się tego przez zamocowanie jednego końca rury w rozszerzeniu złączki lub na drugim końcu rury. Najczęściej używany jest do układania rurociągów na kable.
Kształtki mosiężne do rur HDPE można stosować do rozłączalnych połączeń.
Połączenia nierozłączne
Połączenia nierozłączne są najczęściej używane do łączenia konstrukcji podziemnych lub betonowych, ponieważ ten typ jest uważany za najbardziej niezawodny. Spawanie rur może odbywać się w następujący sposób:
- Pośladek. Najpopularniejsza metoda łączenia rur o tej samej średnicy;
- Spawanie gniazdowe. W przypadku tej metody łączenia rur stosowane są łączniki o średnicy wewnętrznej równej temu samemu parametrowi rurowemu.
- Zgrzewanie na prasie lub krawędziach. Służy do dokowania rur ze strukturami, na przykład studniami.
- Spawanie elektrooporowe. Występuje za pomocą sprzęgów elektrycznych i jest uważana za najbardziej niezawodną metodę łączenia.
Okucia formowane i spawane elektrycznie służą do wyposażenia w połączenie jednoczęściowe.
Rodzaje osprzętu
Wszystkie kształtki różnią się pod względem cech konstrukcyjnych i odpowiednio do ich zastosowania. W zależności od tego okucia można podzielić na:
- Łączniki występujące w trzech głównych typach:
- Równoprzepustowy, łączący rury o tej samej średnicy.
- Kompensujące, używane głównie do przełączania na rury o mniejszej średnicy.
- Kołnierzowe, stosowane do łączenia rur o dużej średnicy.
- Adaptery. Z ich pomocą do rurociągu podłączane są różne zawory lub inny rodzaj rury, na przykład metalowa.
- Krany. Służy do zmiany kierunku rur, obróć system. Standardowe łuki są dostępne z możliwością obrotu o 45º, 66º lub 90º. Niektóre firmy zajmują się produkcją okuć według parametrów klienta. Jeżeli do montażu systemu wymagane jest zgięcie o różnym stopniu kąta, to takie dopasowanie można zawsze zamówić u producenta.
- Sedelka. Przeznaczone są do układania różnych gałęzi. Siodło na rurze HDPE może mieć dwa typy:
- Zaciska, zaciska rury ze wszystkich stron.
- Podkładki użyte do przecięcia nowego rurociągu w istniejącym systemie.
- Przejścia i koszulki. Służą do instalacji rozgałęzionych rurociągów i podłączenia do sieci innych urządzeń.
- Czapki. Służy do czasowego blokowania dopływającej cieczy lub gazu do rury.
Pewne rodzaje łączników są przeznaczone do montażu określonego projektu rurociągu.
Okucia są produkowane w celu ułatwienia montażu rur z polietylenu. Prawidłowo dobrany zestaw elementów łączących w jak największym stopniu skraca czas wymagany do instalacji systemu rurociągów i znacznie ułatwia pracę przy podłączaniu rur.
Łączniki są nazywane złączkami zaprojektowanymi do pojedynczego zadania - łącząc ze sobą segmenty rur i przekształcając je w pojedynczy rurociąg.
Złącza są różne, a główne różnice między nimi dotyczą zastosowanych materiałów i samego projektu.
W tym artykule rozważymy sprzęgi PND, które tworzą wewnętrzne i zewnętrzne systemy zaopatrzenia w wodę lub kanalizacji.
Treść artykułu
Funkcje i cel
HDPE jako materiał jest rodzajem polietylenu. Polietylen jest nazywany pochodną polimeru, w rzeczywistości jest nim.
Produkty polimerowe w naszych czasach zajmują czołowe pozycje na rynku, co jest dość naturalne, biorąc pod uwagę ich powszechne znaczenie oraz niezwykłe cechy.
Polietylen jest również tańszą wersją polimeru, przeznaczoną głównie do układania kanałów i technicznych systemów zaopatrzenia w wodę.
HDPE jest odszyfrowany jako polietylen o niskim ciśnieniu. Jest produkowany w specjalnych komorach w warunkach niskiego ciśnienia i z góry określonych temperatur. HDPE jest znacznie mocniejszy niż zwykły polietylen, nie ściera się, rury z niego mają doskonałą sztywność obwodową.
Zatem HDPE rur i kształtek nadal dobrze wytrzymują wpływ zewnętrznych dowolnego rodzaju łatwo spawać urządzenie dyfuzyjne o gramaturze niewiele.
Mufy z HDPE - są integralną częścią produktów HDPE. Bez tego połączenia rur HDPE okaże się koszmarem gdy każdy segment miał być zamontowane w położeniu roboczym i spawane ręcznie.
Specyfika interakcji między materiałami nakłada na nas pewne ograniczenia. W przypadku rur z HDPE można stosować złączki i złączki tego samego materiału o tej samej średnicy.
Na przykład rozsądnie jest odłożyć złączki o średnicy 63 mm i tym samym materiałem do produktów HDPE o średnicy 63 mm. Tylko w ten sposób będziesz mieć pewność, że nic się nie zawali z czasem, a działające połączenie będzie trwać przez maksymalny czas.
Jak już zauważyliśmy, sprzężenia muszą w pełni spełniać charakterystykę stosowanych na nich rur, a także warunki panujące w rurociągu.
Rury w nowoczesnych systemach łączności nie są bynajmniej jedynym elementem działającym. Każdy rurociąg przekazuje przewoźnika. Przewoźnik jest przewożony pod pewną presją i w określonej ilości. Aby nie przeciążać systemu po raz kolejny, wszystkie elementy rurociągu dobierane są bardzo ostrożnie. Dotyczy to również sprzęgów.
Tak więc przy wyborze złącza z HDPE należy koniecznie obejrzeć, że:
- utrzymywał wystarczający poziom ciśnienia;
- zbliżony do średnicy;
- miał tę samą klasę materiału;
- zbliżył się do zakresu temperatur roboczych.
Te cztery warunki nie są jedynymi - ale najważniejsze. Każdemu wyposażeniu w sprzedaży towarzyszy dokumentacja, w której wskazano jej właściwości.
Standardowe IPA ciśnienie sprzęgła jest utrzymywana między 10 i 25 bar, w zależności od modelu, począwszy od ich średnicy 30-63 mm i rozciąga się do 110 mm, to jest tylko rura wewnętrzna, zewnętrzne rury HDPE zebrano złączki o średnicy kilkuset milimetrów.
Jednym z najbardziej krytycznych warunków jest temperatura pracy. HDPE jako materiał - po prostu doskonały, ale przy wysokich temperaturach w swojej pierwotnej wydajności nie może sobie poradzić. Produkty z niego zaczynają się topić i trwale deformować.
Dlatego PND stara się nie wykorzystywać ogrzewania i ciepłej wody jako komponentów do rurociągów. To samo dotyczy złączek HDPE.
Rodzaje i wyróżnienia
Rozważmy podstawowe wersje złączek HDPE przeznaczonych do łączenia rur. Ich główną różnicą jest projekt. Różne elementy wyposażenia są przeznaczone do różnych sytuacji, a ich konstrukcja jest inna.
Sprzęgło polimerowe sprężające
Pod względem projektów są podzielone na:
- kompresja;
- spawane;
- spawane elektrycznie.
Te trzy grupy są najczęściej używane. Poznamy ich lepiej.
Kompresja
Bardzo podobne do gwintowanych, tylko słusznie są uważane za ulepszoną ich odmianę. Złączka zaciskowa jest wyposażona w specjalną nakrętkę, która napręża połączenie i czyni go bardziej niezawodnym.
Oprócz nakrętki jest w nich dużo uszczelek, a sam projekt jest znacznie ulepszony w porównaniu ze standardowymi gwintowanymi produktami.
Niemniej jednak złącza HDPE z kompresją są bardzo powszechne. Ich średnice zaczynają się od 63 mm i osiągają 120-150 mm. To wszystko jest czymś więcej - jest rzadkością, ponieważ produkty do kompresji wciąż nie mają zalet spawania.
Przegląd złącz kompresyjnych HDPE (wideo)
Spawane
Spawane złącze jest złączem, które jest połączone z rurą poprzez spawanie. Stalowe i metalowe kęsy są spawane za pomocą spawarki. Ten rodzaj połączenia ma swoje zalety i wady.
Zalety to szczelność, możliwość spawania złącza w dowolnym miejscu, ogólna wytrzymałość itp. Przeciw - niezdolność do samodzielnego wykonania pracy. Przynajmniej musisz mieć spawarkę, ochronę i przynajmniej minimalne umiejętności.
Bez spawacza podczas pracy z metalem nie można tego zrobić. Kolejną rzeczą jest praca z PND. Polimery są spawane poprzez proste ogrzanie ich części do temperatury topnienia, a następnie połączenie ich we wstępnie ogrzanym stanie.
W przypadku spawania jakościowego wystarczy mieć pod ręką aparat dyfuzyjny. Reszta to kwestia techniki. Powstałe węzły nie są gorsze od metalu pod względem szczelności lub wytrzymałości, ale są realizowane wielokrotnie szybciej i łatwiej, a co najważniejsze - całkowicie własnymi rękami.
Spawane elektrycznie
Złącza elektrospawane różnią się nieco od standardowych. Sprzęgło elektryczne - okucie, przeznaczone do montażu linii praktycznie w trybie automatycznym. Oznacza to, że działa on samodzielnie, wystarczy podłączyć urządzenie i zainstalować je we właściwym miejscu.
Sprzęgło elektryczne ma kształt podobny do zwykłej odmiany. Składa się on również z solidnego korpusu HDPE, ma określoną średnicę, na przykład 63 mm. Główną różnicą jest wbudowana obudowa kabla do ogrzewania.
Wykonują 90% całej pracy. Kable te wnikają w korpus złączki, a ich wyjścia są instalowane w dwóch miejscach i nazywane są zaciskami. Podłącz bieżący podajnik lub przenośny transformator do terminali. Prąd płynący w pewnych warunkach, prowokuje przewody grzejne, a z kolei ciepły polietylen wokół siebie.
W pewnym momencie polietylen osiąga temperaturę topnienia. Będzie to początek procesu spawania złącza elektrycznego. Wtedy wszystko dzieje się zgodnie ze standardową procedurą. Polimer w stopionej formie wchodzi w symbiozę z polimerem rury, tworząc stałe połączenie monolityczne. Nie potrzebujesz nawet spawarki.
Wystarczy podłączyć bieżący podajnik do terminali, a następnie usunąć go, gdy proces się zakończy. Po 30 minutach sprzęgło będzie w pełni chwytać i będzie gotowe do pracy.
W ramach tego programu bardzo wygodnie jest pracować, szczególnie dla osób, które są zaangażowane w zewnętrzne systemy wodociągowe i kanalizacyjne. Lokalne produkty mają ogromną średnicę. Łączenie ich ręcznie jest trudne i niewdzięczne. Obecność HDPE znacznie upraszcza pracę osoby, zwiększa jej wydajność.
Dodaj do zakładek
- All-in-one (styki doczołowe ze specjalną spawarką i elektrooptowaniem).
- Dzielony (kołnierzowy i kołnierzowy ze specjalną uszczelką).
Jeżeli podczas pracy zostanie zastosowane ciśnienie na rurociągu, stosuje się zgrzewanie doczołowe lub zgrzewanie w skrzyni. Jednak połączenie kołnierza w jego niezawodności nie ustępuje wcześniejszym dwóm metodom.
Zwrócić uwagę na fakt, że siła rur polietylenowych w połączeniu z ich plastyczność, a ponadto, wysoka niezawodność ich używać niemal niezbędny w obszarach o wysokiej aktywności sejsmicznej, w tych miejscach, gdzie ziemia jest okresowo ruch obserwowanych.
Połączenie rur odbywa się za pomocą spawania doczołowego.
Kiedy pojawia się pytanie, w jaki sposób jest najbardziej efektywny, pożądane jest nadanie pierwszeństwa jednej z następujących metod spawania, która wydaje się dla ciebie najbardziej optymalna. Jeśli wolisz zgrzewanie doczołowe, musisz pamiętać, że jest on wytwarzany przy użyciu specjalnego narzędzia.
Jego istotą jest fakt, że podczas procesu końce połączonych rur są ogrzewane do lepkości za pomocą specjalnego elementu grzejnego. Następnie roztopione końce obydwu rur są ze sobą połączone pod ciśnieniem i w naturalny sposób stygnie się w złączu. Końce rur muszą zostać oczyszczone z zanieczyszczeń i odtłuszczone przed ogrzaniem.
Podczas pracy, uwaga jest skierowana do temperatury grzewczej - musi być utrzymywane w pożądanym trybie wysokość stopienia materiału w czasie ogrzewania końców rur, a ciśnienie wywierane na powierzchnię łącznika.
Po schłodzeniu spoina powinna być równa, wystając na tę samą wysokość. Dzięki temu wynikowi uzyskasz maksymalną niezawodność i wytrzymałość szwu.
Najpopularniejszą metodą łączenia jest zgrzewanie doczołowe. Montaż rurociągu w większości przypadków odbywa się tą metodą. Należy jednak wziąć pod uwagę inną metodę - spawanie elektromotoryczne, które nie jest mniej efektywne ze sobą. Podczas spawania w ten sposób ogrzewanie łączonych powierzchni jest spowodowane kształtowymi elementami polietylenowymi. który również topi się po ogrzaniu i zestaleniu rur po zestaleniu.
Elementy te są ogrzewane przez sprzęt, którego przepływający prąd doprowadza do pożądanej temperatury ukształtowaną część. Podobnie jak w przypadku zgrzewania doczołowego, wszystkie końce rur i części muszą być dokładnie oczyszczone i odtłuszczone przed rozpoczęciem pracy.
Następnie należy sprawdzić, czy elementy mocujące i rury są całkowicie nieruchome od początku spawania do stopnia chłodzenia. Jeśli gałęzie mają być spawane, zaciski muszą być starannie wybrane.
Mówiąc o zaletach elektrooporowego, konieczne jest, aby zwrócić uwagę na łatwość montażu, wysoka niezawodność i trwałość połączeń, niskim kosztem czasu, bezpieczeństwa i skuteczności tej metody, a ponadto praktyczne dla prac montażowych w ciasnych przestrzeniach. Ta technika okazała się niezawodna i prosta i została z powodzeniem zastosowana w przypadku gazociągów i rur wodociągowych.
Połączenie bez spawania
Połączenie z łącznikami
Nie ulega wątpliwości, że metoda spawania jest niezawodna i prosta, ale czasami nie można jej użyć. W takich sytuacjach można zastosować sprzężenie sprzęgu. Łączniki, które są produkowane specjalnie do rurociągów polietylenowych, są przeznaczone tylko do niezawodnego połączenia łączonych końców rur.
Złączki zaciskowe - tak zwane sprzęgi - nie wymagają specjalnego wyposażenia do instalowania rur z polietylenu i mogą być łatwo instalowane przez laika. Ten sposób mocowania jest szczególnie dobry w przypadkach, gdy stosowane są rury o małej średnicy - od 20 do 315 mm.
Ponieważ rury z HDPE mają niską sztywność, rurociągi ciśnieniowe, zwłaszcza o dużej średnicy, muszą być ze sobą spawane. Pełni umożliwia absolutnej szczelności spoin łączących rury po zestaleniu szczelnie ze sobą w jednej jednostce, która nie może ustąpić bessvarochny w całości, ponieważ w związku z tym złącza rurowego może ulegać deformacji z dalszym rozprężeniu.
Jednakże zaletą gwintowanymi jest możliwość, w razie potrzeby demontażu części zespołu, który w sposób nie może dać żadnej jednej z powyższych metod spawania. A demontaż stawów można załatwić więcej niż jeden raz, a to siłą nawet nie przeszkoleni dla tej osoby. Żadne narzędzia i narzędzia nie są potrzebne, z wyjątkiem jednego specjalnego klucza, który może odkręcić i dokręcić nakrętki na złączach.
Instalacja jest możliwa nawet w niskich temperaturach, a szeroka gama elementów łączących o dowolnej średnicy umożliwia wytwarzanie przewodów, rozgałęzień i zwojów w systemie.
Rurociąg HDPE do kanalizacji
Samoorganizacja rurociągów z polietylenu do ścieków jest dość prosta. Rury ze złączami, narożnikami i trójnikami są połączone za pomocą gumowych pierścieni uszczelniających. Rury z niewielkim wysiłkiem wkładane do gniazda, jeżeli takie uszczelnienie nie jest wystarczające, rury są dodatkowo pokryte silikonowym szczeliwem.
Montaż rur polietylenowych kanalizacji nie powoduje żadnych trudności: albo na suficie lub na ścianie są najprostsze przystawki zamki, które muszą być przykręcone do ściany za pomocą śrub. W przypadku jeśli nie szczególnie dbać o estetykę, można po prostu dysk A stalowych wałkach otwory nieznacznie większą średnicę w ścianie, wyginać końce i wkręcić rurę do tych prowizorycznych szelkami. Z pomocą zwykłych lamp może być zainstalowany rurociąg bliską tylko na ścianie, można umieścić go na krótkiej odległości do kołka, który jest często o wiele bardziej wygodne.
Rurociąg HDPE do instalacji elektrycznej
W przypadku przewodów elektrycznych zastosowanie zarówno gładkich, jak i falistych rur z polietylenu jest równie skuteczne.
W tym przypadku uwzględniono dwie główne cechy IPA:
- Elastyczność, elastyczność.
- Brak umiejętności prowadzenia prądu.
- W celu okablowania rurociąg jest układany na powierzchni ścian i ukryty (wewnątrz ściany) i służy jako ochrona kabli podczas układania w glebie. W tym drugim przypadku częściej stosuje się rury karbowane z HDPE. Jednocześnie szczególną uwagę zwraca się na hermetyczne dokowanie rur.
Prawidłowy montaż rur
Szczelność można osiągnąć za pomocą jednej z dwóch opcji:
- Zgrzewanie doczołowe lub w złączach.
- Gorąca obudowa z rur HDPE w gnieździe. Ogrzewana rura jest wkładana z wysiłkiem do gniazda poprzedniej rury. Tak więc, lokalnie zdeformowane, wypełnia wszystkie wewnętrzne nierówne powierzchnie gniazda, w wyniku czego gwarantuje się szczelność.
Zastosowanie rur polietylenowych w systemie zaopatrzenia w wodę
W zależności od ciśnienia w wodzie, trzeba narzędzie dostępne i, oczywiście, na swoich zamiarach, w domu mogą korzystać z więcej niż jedną metodę łączenia tych samych rur.
Zastosowanie złączek zaciskowych
Jest to bardzo popularna metoda instalowania rur z polietylenu o małej średnicy do doprowadzania wody. złączki są wykonane z rur o średnicach do 110 mm, ale w praktyce jest to wygodne w użyciu rury 32 mm, chociaż wewnątrz większy rozmiar, a nie do spełnienia.
Okucia o małej średnicy są instalowane ręcznie, nawet klucz nie jest potrzebny.
Procedura jest dokładnie taka sama, jak w przypadku montażu rur wodociągowych z metalu i tworzywa sztucznego, tylko w miejscu pierścienia rozciętego stosuje się uszczelkę gumową:
- Przygotuj końce rur. Są one cięte pod kątem prostym, najlepiej za pomocą specjalnego przecinaka do rur.
- Na rurze założyć gumowy pierścień uszczelniający z nakrętką łączącą.
- Rura jest wkładana do złączki, a następnie nakrętka złączkowa jest nakręcana na gwint.
Zalety takiej instalacji są oczywiste: jest bardzo prosta i utrudnia połączenie. Polietylen naprawy rur z takich połączeń jest możliwe bez skomplikowanych narzędzi, aby część wada jest wycięty z wody, a zamontowane na pustej przestrzeni na nowych przewodów rurowych. Jednocześnie połączenie zależy bezpośrednio od gumowej uszczelki: jeśli stanie się nieprzydatne, połączenie przepłynie.
Zastosowanie kształtek do spawania dyfuzyjnego
W ten sposób połączony jest również polipropylen. W tym przykładzie wykonania, połączenie złączki z rurą, nie różni się od instalacji z polipropylenu: wewnętrzna powierzchnia łącznika jest ogrzewany i lutu na wkładce dyszy o odpowiednim rozmiarze w zewnętrznej powierzchni rurowego. Po kilku sekundach połączenie jest gotowe.
Wykorzystanie złączki do spawania za pomocą lutownicy
W takim przypadku połączenia nie można już rozmontować. Podczas naprawy rur HDPE, połączonych za pomocą okuć podczas spawania, do przywrócenia szczelności będzie potrzebna specjalna lutownica. Jednak takie związki praktycznie nigdy nie płyną. Przed ich montażem, powinny być na zewnątrz skosu rury jako wstrząsami i łobuzami - z powodów, dzięki którym spoin przepływu.
Spawanie czołowe
Ta metoda łączenia jest zawsze używana podczas układania rur HDPE o dużej średnicy. W takim przypadku operacje technologiczne postępują w następujący sposób:
- Pomiędzy końcami rur znajduje się grzałka elektryczna.
- Po stopieniu rur grzejnik elektryczny zostaje usunięty.
- Połączenie jest gotowe po czasie niezbędnym do ochłodzenia rur polietylenowych.
Złącze doczołowe charakteryzuje się bardzo wysoką wytrzymałością (80-90% wytrzymałości rur monolitycznych). Ta metoda jest niepożądana w przypadku rur o ścianach cieńszych niż 5 mm. Jednak przy pilnym zapotrzebowaniu na rury z HDPE są one stopione po podgrzaniu końcówek na konwencjonalnej kuchence gazowej. Chociaż taka sztuczka i pozostawia brudny szew na zewnątrz i wewnątrz rury, zimna woda takie związki przetrwają lata.
Sprzężenie elektryczne
Ten sposób łączenia jest taki sam, jak w przypadku spawania, ale w tej sytuacji sprzężenie (dowolne inne dopasowanie) jest połączone z lutownicą. W środku plastiku znajduje się spirala niskotemperaturowa, wystarczy ją podać do podgrzania. Ta metoda jest prosta, szybka, ale nie tania.