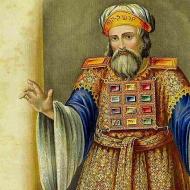
Сборка сварка котла в отопительную печь. Трубы для коллекторов и трубопроводов. Ремонт заклепочных соединений
К атегория:
Общие сведения о кранах и котлах
Материалы и способы изготовления котлов
Паровой котел работает под значительным давлением, поэтому является весьма ответственным агрегатом и должен обеспечивать надежность в работе.
Чем выше рабочее давление и температура, при которой работает котел, тем в более тяжелых условиях находится металл, из которого изготовлен котел.
Хорошо иметь возможность вставлять большие ковши дерева или угля в котел - дольше и мягче будет гореть. Но лучше, если камера сгорания коротка и выше, чем длинная и низкая. Усовершенствованная инженерия, желательно с английским названием, которая, безусловно, работает лучше, чем старомодный лоскут, позволяющий воздуху проникать в решетку. Эта известная система аэрации представляет собой ряд отверстий в боковых стенках котла, который продувает воздух в бункер.
Федеральный горный и промышленный надзор России
Это имеет смысл, если вы его сжигаете. Это трудное топливо, и этот способ вентиляции является выгодным в этом случае. Для всех других видов топлива это проклятие. Легко мигает древесный уголь или древесина, когда они получают воздух во всем объеме горелки, что означает невозможность сжигания огромного количества внезапно высвобождаемых газов, то есть дыма и потерь.
Основные требования к металлу котлов:
1) высокая теплоустойчивость - способность металла сохранять прочность в условиях высокой температуры и больших напряжений;
2) высокая вязкость - способность металла сохранять свои механические свойства при меняющихся или повторных нагрузках;
3) пониженная склонность к старению - способность металла сохранять свои механические свойства в течение длительного времени;
4) устойчивость металла против коррозии - под воздействием воды и пара;
5) стабильность структуры - устойчивость металла против структурных изменений, снижающих его механические свойства;
6) плотность, однородность строения металла, отсутствие в нем внутренних дефектов: плен, трещин и посторонних включений.
То есть, пока уровень топлива не будет достаточно высоким, чтобы покрыть большую часть отверстий. Однако в момент сжигания горелки и открытия верхних отверстий большая часть воздуха, подаваемого воздуходувкой, убегает, вызывая чрезмерную вентиляцию и охлаждение печи.
Площадь здания, в котором может нагреваться котел
Многие производители продолжают давать ориентировочную площадь поверхности здания, которая может нагревать котел данной мощности. Некоторые из них дают несколько вариантов в зависимости от степени разогрева дома, другие - одно значение, если ваш дом - хижина.
Поэтому элементы котла, находящиеся под давлением, изготовляются исключительно из стали (ГОСТ 5520-62). Эта сталь, кроме высоких требований относительно ее химического состава, подвергается более тщательному контролю и дополнительным испытаниям на ударную вязкость и чувствительность к старению.
Листовая сталь марок Ст. 2 и Ст. 3 предназначена для котлов и сосудов, работающих при температуре не выше 120°С. Для котлов, работающих при более высоких температурах, применяется сталь марок 15К и 20К.
В любом случае не следует инструкциям производителя при выборе мощности котла. Они ведут в поле, потому что они слишком авансированы. Это не производитель, чтобы выбрать мощность котла. В любом случае, если вы читаете условия гарантии, часто там прямо написано, что влияние любого неправильного выбора производителя энергии не отвечает.
Подробнее о правильном выборе мощности котла вы прочтете. На страницах некоторых производителей или даже в инструкциях по использованию котлов можно найти информацию о конструкции, а оборудование котла может отличаться от реальности. Как только производитель вводит новые усовершенствования, он не успевает за обновлениями и инструкциями на сайте!
Детали котла, не находящиеся непосредственно под давлением, могут изготовляться из углеродистых сталей обыкновенного качества (ГОСТ 380-60) или качественной конструкционной углеродистой стали (ГОСТ В 1050-60).
Котельные трубы - пароперегревательные, кипятильные, дымогарные и жаровые - изготовляются из стали марки 10 (ГОСТ 8733-58-и 8731-58). Все трубы подвергаются гидравлическим испытаниям, а также технологическим пробам на сплющивание и раздачу. Для дымогарных труб испытание на раздачу может быть заменено на бортование.
Конечно, нет лавины улучшений, и только у производителя есть клиент с глубоким уважением. Если вы хотите купить его, вы придете, чтобы попросить обновленные спецификации. Чемпионат Вестфалии Вестфалии был на пике, одновременно с тремя версиями одной и той же модели котла, без каких-либо объяснений.
К сожалению, котел - это то, что мы найдем в магазине, и не обязательно в соответствии с рекламными материалами. Более крупные производители относятся к клиенту более серьезно и публикуют довольно полные и обновленные данные. Чем меньше производитель и местный, тем больше стоит поднять его до текущих технических характеристик котлов или лучше всего пойти в магазин и увидеть продукт на месте.
Электросварные трубы, изготовляемые в соответствии с ГОСТ 1753-53 и дополнительными к нему техническими условиями № 14-32,. находят все более широкое применение в котлостроении. Раньше части котла соединялись исключительно посредством заклепок. Клепка являлась основной и весьма ответственной операцией в котельных работах. В настоящее время трудоемкие клепальные работы сохранились лишь при ремонте старых котлов клепаной конструкции. Вновь строящиеся котлы изготовляются сварной конструкции, в которых все элементы соединяются электросваркой.
Котел для работы только с номинальной мощностью
Заводское сток - это декларация о том, что котел подходит только для номинальной мощности и должен устанавливаться только в узле теплового буфера. Эта игра дает продюсеру много проблем. Прежде всего, проблема сертификации отсутствует. В то время как номинал не имеет проблем с соблюдением требований настоящего стандарта, это трудно, как минимум.
Но когда производитель говорит, что его котел подходит только для работы с номинальной мощностью, проблема исчезает! Продукт тестируется только на номинальной мощности, соответствует стандарту, тиснению и разрешению ногтей. И как это выглядит в средней котельной? Очевидно, мало кто внимательно прочитал руководство, где упоминание о необходимости работать только на номинальной основе вписано в небольшой шрифт. Устанавливает такой котел без теплового буфера и горит, как и большинство, т.е. номинальная мощность достигается только в январе.
Электродуговая сварка элементов металлическим электродом (метод Славянова) представляет собой процесс последовательного местного расплавления кромок основного металла электрической дугой, возникающей между электродом и основным металлом. Температура, возникающая в результате образования электрической дуги, достигает 5500 °С.
Электродуговая сварка может производиться электродами трех видов: – простыми электродами - стальная проволока; – тонкообмазанными - электроды, покрытые тонким слоем мела, чем достигается устойчивость дуги; – электродами с толстой обмазкой - обмазкой сложного состава, содержащей шлакообразующие, раскисляющие, легирующие и другие компоненты, повышающие механические свойства наплавленного металла и качество сварного соединения в целом.
За последнее десятилетие широкое распространение получила автоматическая сварка под слоем флюса по методу акад. Патона, обеспечивающая высокое качество сварного шва и наибольшую производительность при выполнении сварочных работ. Сущность процессов сварки под слоем флюса заключается в том, что электрическая дуга непрерывно горит под толстым слоем порошкообразного флюса. Благодаря этому свариваемый металл защищен от окисления кислородом окружающего воздуха, процесс расплавления электрода и основного металла происходит равномернее, сварной шов получается ровным, плотным и однородным с хорошим проваром по всей глубине шва. Непрерывность ведения сварки под слоем флюса осуществляется при помощи специального приспособления, в котором изделия и электроды автоматически непрерывно перемещаются относительно друг друга, при этом происходит непрерывная подача электрода по мере его расплавления и слой флюса автоматически создается впереди движущегося электрода.
Для получения сварного соединения высокого качества свариваемые детали должны быть соответственно подготовлены: очищены от ржавчины и масла (до металлического блеска), кромки деталей соответствующим образом разделаны. Подготовка кромки под сварку производится согласно чертежам и зависит от характера соединения и толщины свариваемых элементов.
На рис. 24 и 25 представлены основные типы сварных соединений котла крана ПК-ЦУМЗ-15.
Одним из основных моментов, задержавших применение сварки в ответственных изделиях, какими являются паровые котлы, долгое время были затруднения в контроле качества сварного соединения.
Рис. 24. Примеры электросварных стыковых соединений: а -соединение огневой решетки с барабаном топки; б -соединение дымовой решетки с наружным барабаном котла; 1- огневая решетка; 2 - барабан топки; 3 -дымовая решетка; 4 - наружный барабан котла
Рис. 25. Соединение грязевого и шуровочного колец с барабаном топки и наружным барабаном котла:
1-наружный барабан котла; 2 -барабан топки; 3-грязевое кольцо; 4 --шуро-вочное кольцо; 5-предохранительный лист шуровочного кольца; 6 - лапа котла
В результате несовершенства способов контроля не было достаточной гарантии в том, что внутри сварного шва отсутствуют такие пороки, как пористость, газовые раковины, посторонние включения и малозаметные трещины, снижающие прочность соединения. По мере совершенствования технологии производства сварочных работ и методов контроля область применения сварки все более расширяется, в том числе и в котлостроении, но при этом следует иметь в виду, что ответственную сварку производят лишь сварщики, получившие на это разрешение после сдачи проб; пробы периодически повторяются.
Контроль сварного соединения заключается в следующем: – проверяют исходные материалы: исходный металл, подлежащий сварке, металл электрода, состав обмазки и флюса; – проводят испытания специальных контрольных образцов на растяжение и определение ударной вязкости; – анализируют химический состав наплавленного металла; – производят рентгеновские снимки, отражающие все внутренние пороки шва; – гидравлически испытывают сваренные изделия, работающие под давлением; – сварочный шов осматривают снаружи.
К атегория: - Общие сведения о кранах и котлах
9.1. Общие положения
9.1.1. При изготовлении монтаже реконструкции и ремонте стальных водогрейных, паровых котлов должна применяться технология сварки, аттестованная в соответствии с требованиями НД.
9.1.2. Присадочные материалы применяемые при сварке, должны обеспечивать временное сопротивление разрыву наплавленного металла не ниже нижнего предела временного сопротивления разрыву основного металла (по ГОСТ или ТУ для данной марки стали) а относительное расширение и ударная вязкость должны быть не ниже величин указанных в соответствующих НД на присадочные материалы.
9.1.3. Для выполнения сварки должны применяться исправные установки аппаратура и устройства, обеспечивающие соблюдение требований НД.
9.1.4. К сварке элементов котлов допускаются сварщики, аттестованные согласно Правилам аттестации сварщиков, при этом сварщики могут быть допущены только к тем видам работ, которые указаны в удостоверении сварщика
9.1.5. Руководство работами по сбору котлов и их элементов сварке и контролю качества сварных соединений должно быть возложено на специалиста прошедшего проверку знаний настоящих Правил.
9.2. Сварочные материалы
9.2.1. Сварочные материалы, применяемые для сварки котлов, должны соответствовать требованиям стандартов и технических условий, что должно подтверждаться сертификатом завода.
9.2.2. Марки, сортамент условия хранения и подготовка к использованию сварочных материалов должны соответствовать требованиям НД на сварку.
9.2.3. Перед использованием сварочных материалов (электродов, сварочной проволоки, флюсов, защитных газов) необходимо проверить их качество по технической документации на изделие, инструкцией по сварке и контролю сварных соединений, действующим стандартом паспортами или техническими условиями на сварочные материалы:
электроды - требованиям ГОСТ 9466;
сварочная проволока - требованиям ГОСТ 2246;
углекислый газ - требованиям ГОСТ 8050;
флюсы сварочные - требованиям ГОСТ 9087.
9.3. Подготовка и сборка деталей для сварки
9.3.1. Подготовка кромок и поверхностей под сварку должна выполняться механической обработкой либо путем термической резки или строжки (кислородной воздушно-дуговой, плазменно-дуговой) с последующей механической обработкой (резцом, фрезой, абразивным инструментом) Глубина механической обработки после термической резки (строжки) должна быть указана в НД зависимости от восприимчивости конкретной марки стали к термическому циклу резки (строжки).
9.3.2. При сборке стыковых соединений труб без подкладных колец с односторонним расчисткой кромок и свариваемых без подварки корня шва смещение (несовпадения) внутренних кромок не должны превышать значений, установленных НД.
9.3.3. Кромки деталей, подлежащих сварке, и участки, прилегающие к ним, должны быть очищены от окалины, краски, масла и других загрязнений согласно требованиям НД.
Прихватка собранных под сварку элементов должна выполняться с использованием тех же сварочных материалов, которые будут использованы (или допускаются к использованию) для сварки данного соединения.
9.4. Аттестация технологии сварки
9.4.1. Технология сварки при изготовлении, монтаже и ремонте котлов допускается к применению после подтверждения ее технологичности на реальных изделиях, проверки всего комплекса нужных свойств сварных соединений и освоения эффективных методов контроля их качества.
9.4.2. Аттестация технологии сварки проводится каждым предприятием до начала ее применения с целью проверки соответствия сварных соединений требованиям Правил и НД. Аттестация должна проводиться для каждой группы однотипных сварных соединений, выполняемых на данном предприятии.
9.4.3. Аттестация проводится аттестационной комиссией, созданной на предприятии согласно программе, разработанной этим предприятием и утвержденной председателем комиссии.
Программа должна предусматривать проведение неразрушающего и разрушающего контроля контрольных сварных соединений и оценку качества сварки по результатам контроля.
Порядок проведения аттестации, в том числе и той применявшейся на предприятии до вступления в силу настоящих Правил, определяется НД.
Если при аттестации технологии сварки получены неудовлетворительные результаты из любого вида испытаний аттестационная комиссия должна принять меры для выявления причин несоответствия полученных результатов установленным требованиям и решить, следует провести повторные испытания или данная технология не применима для сварки производственных соединений и нуждается доработку
Разрешение на применение технологии сварки, прошедшей аттестацию на предприятии, выдается органами Госнадзорохрантруда на основании выводов головной организации по сварке
9.5. Технология сварки
9.5.1. При изготовлении котлов сварки элементов, предназначенных для работы под давлением, должен выполняться при температуре воздуха не ниже 0 ° С. В процессе монтажа и ремонта допускается сварка при минусовой температуре окружающей среды с соблюдением специальных условий предусмотренных технологической документацией.
9.5.2. После сварки шов и прилегающие участки должны быть очищены от шлака, брызг металла и других загрязнений.
Внутренний рубчик в стыках труб, выполненных контактной сваркой, должен быть удален для обеспечения проходного сечения.
9.6. Контроль качества сварных соединений
9.6.1. Предприятие-изготовитель, монтажное или ремонтное предприятие применяет следующие виды и объемы контроля своей продукции, которые бы гарантировали выявление недопустимых дефектов, ее высокое качество и надежность в эксплуатации. При этом объем контроля должен соответствовать требованиям настоящих Правил.
9.6.2. Контроль качества сварки и сварных соединений включает:
проверку имеющейся документации по аттестации персонала;
проверку исправности сборочно сварочного термического и контрольного оборудования, аппаратуры, приборов и инструментов;
контроль качества основных материалов; контроль качества сварочных материалов и материалов для дефектоскопии;
операционный контроль технологии сварки;
неразрушающий контроль качества сварных соединений;
разрушающий контроль качества сварных соединений;
контроль исправления дефектов.
Виды контроля определяются конструкторской организацией в соответствии с требованиями настоящих Правил, НД на изделие и сварку и указываются в конструкторской документации котла.
9.6.3. Основными видами неразрушающего контроля металла и сварных соединений являются:
визуальный и измерительный;
радиографический; рентгенотелевизионных;
ультразвуковой;
капиллярный или магнитопорошковый;
измерения твердости;
прогонка металлического шара;
гидравлические испытания.
Кроме этого, могут применяться другие методы (акустическая эмиссия, токовихревой контроль и др.).
9.6.4. При разрушающем контроле должны проводиться испытания механических свойств, металлографические исследования.
9.6.5. Специалисты неразрушающего контроля должны быть аттестованы в соответствии с Правилами аттестации специалистов неразрушающего контроля, утвержденных приказом Госнадзорохрантруда Украины от 23 июля 1996N 125.
9.6.6. Изделие признается годным если при любом виде контроля в нем не будут обнаружены внутренние и внешние дефекты, выходящие за пределы допустимых норм, установленных настоящими Правилами и НД на изделие и сварку.
9.6.7. Внешний осмотр сварных соединений производится по всей их длине.
Перед внешним осмотром сварные швы и прилегающие к ним поверхности основного металла на ширину не менее 20 мм по обе стороны швов должны быть очищены от шлака и других загрязнений, затрудняющих осмотр.
Нормы оценки качества сварного соединения по результатам внешнего осмотра и измерения должны быть указаны в технических условиях на изготовление изделия, в инструкциях по сварке и контролю сварных соединений.
9.6.8. Механические испытания сварных соединений должны проводиться в соответствии с требованиями ГОСТ 6996 и ГОСТ 9454.Обязательными видами механических испытаний являются испытания на растяжение, изгиб и сплющивание.
Испытания на растяжение не являются обязательными для поперечных сварных соединений по условиям сплошного контроля этих соединений неразрушающими методами.
9.6.9. Для контроля качества сварных стыковых соединений в трубчатых элементах изделий одновременно и их сваркой в тех же производственных условиях изготавливаются контрольные стыки, из которых вырезаются образцы для проведения механических испытаний. Форма и размеры образцов для механических испытаний, а также их вырезка должны соответствовать ГОСТ 6996.
9.6.10. Количество контрольных сварных соединений должна быть не менее одной на всех однотипных производственных сварных соединениях, выполненных каждым сварщиком в течение 6 месяцев.
9.6.11. Результаты механических испытаний сварных образцов должны быть такими: временное сопротивление разрыву наплавленного металла в МПа (кгс/см2) должен быть не меньше нижней границы временного сопротивления разрыву основного металла, установленного государственным стандартом или ТУ для данной марки стали;
угол загиба не менее 100 для соединений, выполненных электросваркой, и не менее 70 для соединений, выполненных газовой сваркой.
Показатели механических свойств сварных соединений должны определяться как среднее арифметическое от результатов полученных при испытании отдельных образцов, и быть не ниже указанных норм. При этом показатели механических свойств считаются неудовлетворительными, если результаты одного из образцов отличаются от установленных норм более чем на 10% в сторону снижения.
9.6.12. При получении неудовлетворительных результатов по одному из видов механических испытаний разрешается проведение повторных испытаний образцов вырезанных из той же контрольной пластины или из сварного шва изделия. Повторные испытания проводятся лишь по тому виду механических испытаний, давших неудовлетворительные результаты. Для проведения повторных испытаний применяется двойное количество образцов.
Если неудовлетворительные результаты получены и при повторных испытаниях, швы считаются неудовлетворительными.
9.6.13. Объем контроля сварных соединений ультразвуковым или радиографическим средствами определяется НД на изготовление но должен быть не менее:
для деталей с толщиной стенки более 30 мм - 25% длины шва;
для толщин до 30 мм - 10% длины шва.
При этом обязательному радиографическому контролю подлежат все места сопряжения стыковых продольных и поперечных сварных соединений.
Для толщины стенки до 13 мм допускается проводить 100% радиоскопический контроль вместо 10% радиографического.
Швы признаются неудовлетворительными, если просвечиванием будут выявлены следующие дефекты:
трещины всех видов и направлений расположенных в металле швов по линии сплавления и около шовной зоны основного металла;
непровары в корне и по сечению шва;
непровары в вершине шва соединений, доступных к сварке с одной стороны без прокладок, глубиной более 15% толщины основного металла;
поры шлаковые включения сверх установленных НД.
Методы устранения дефектов и порядок контроля исправленных участков устанавливаются техническими условиями на изготовление.
9.7. Гидравлическое испытание
9.7.1. Гидравлическое испытание котлов и их элементов производится с целью проверки их плотности и прочности всех элементов котлов на заводах-изготовителях специально выделенными работниками ОТК заводов
9.7.2. Пробное давление при гидравлическом испытании должно быть:
1,5 рабочих давления, но не менее 0 2 МПа (2 кгс/см2).
Давление воды при испытании должно контролироваться двумя манометрами, один из которых должен быть контрольным.
Для гидравлических испытаний должна применяться вода с температурой не ниже 5 ° С и не выше 40 ° С.
Время выдержки котла под пробным давлением должно быть не менее 10 минут. Падение давления при испытаниях не допускается.
Использование сжатого воздуха или газа для подъема давления не допускается.
После снижения пробного давления до рабочего проводят тщательный осмотр всех элементов котла, сварных соединений по всей их длине.
9.7.3. Считается, что котел выдержал гидравлическое испытание, если не обнаружено:
трещин или признаков разрыва;
течи в сварных, вальцовочных заклепочных соединениях и в основном металле;
видимых остаточных деформаций.